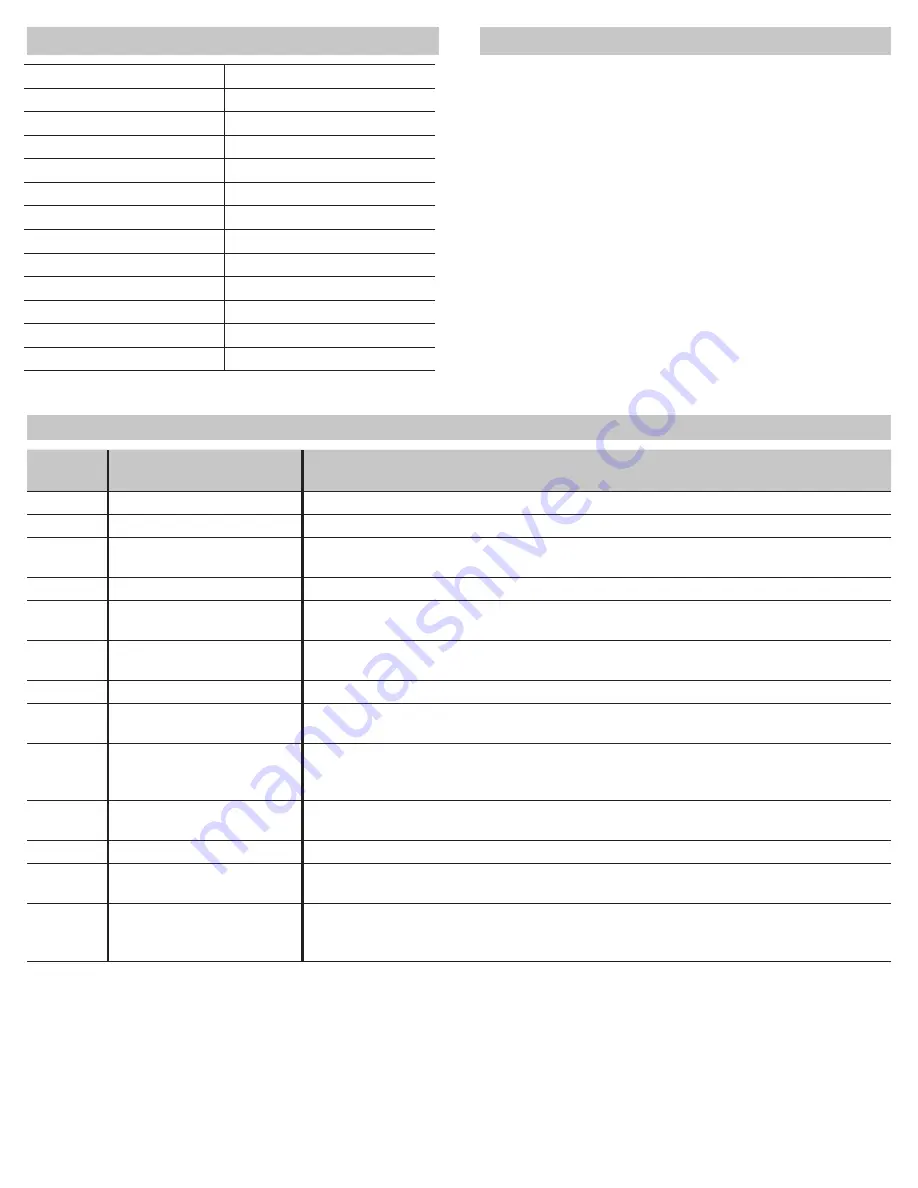
To review the fault history; press and hold the Fault Recall
button and release once the LED goes out. The previous
five fault codes will be displayed. The LED will turn off
momentarily and then go solid after the last fault has been
displayed.
The ICM2812 will not respond to thermostat calls while the
fault history is being displayed
.
To clear the fault history; press and hold the Fault Recall
button and release once the LED starts flashing. The LED will
turn off momentarily and then go solid after the fault history
has been cleared.
The fault history will not erase while the ICM2812 is
performing a heating or cooling call.
Fault Recall Button
Input
18-30 VAC, 60Hz
Ignition Activation Period
3 seconds
Ignitor Warmup
19 seconds
Inducer Inter-purge
60 seconds
Inducer Post-Purge
25 seconds
Inducer Pre-purge
30 seconds
Trial for Ignition
4 seconds
Trials
3
Cool Blower OFF delay
45 seconds
Cool Blower ON delay
6 seconds
Heat Blower OFF delay
100/150 seconds
Heat Blower ON delay
30 seconds
Lockout
60 minutes
ICM2812 Timing
LED Fault Codes
LED
Status
Description
Trouble Shooting Tips
ON
Normal operation
N/A
OFF
Control board failure
Check for proper input voltage and check the fuse; if not resolved replace the control.
1
Ignition failure (soft lockout)
Clean or replace the flame sensor, check the igniter for proper operation & input voltage,
check the transformer’s common is grounded to earth ground.
2
Pressure switch stuck closed
Check for contaminated or defective pressure switch.
3
Pressure switch stuck open
Check for obstructed pressure switch tubing or defective pressure switch. Check for
oxidation on terminals, broken wires, or defective inducer motor .
4
Limit switch fault
Checked for blocked airflow, blocked ductwork, and dirty filter. Check or replace high limit
switch if defective.
5
Flame out of sequence
Check for intermittent or defective gas valve and check for dirty or defective flame sensor.
6
Roll out switch fault
Check for a cracked heat exchanger, defective rollout switch , broken wires on the roll out
switch, or replace roll out switch if required.
7
Weak flame
Weak flame is caused by carbon build up on the flame sensor, poor grounds, or improper
placement of the flame sensor . Clean or replace the flame sensor, reassure grounds,
ensure the flame sensor is fully enveloped in the flame.
8
Mis-wired gas valve
Check for shorted or mis-wired gas valve, check harness wires for any shorts or breaks,
and check the pressure switch for proper operation.
9
Unused
N/A
10
Hot and neutral reversed
Check for proper polarity of the incoming voltage on the primary and secondary sides of the
transformer.
11
Brownout
A brownout fault indicates a low voltage condition. Check the voltage on the primary
and secondary sides of the transformer and ensure there is no excessive load on the
transformer.