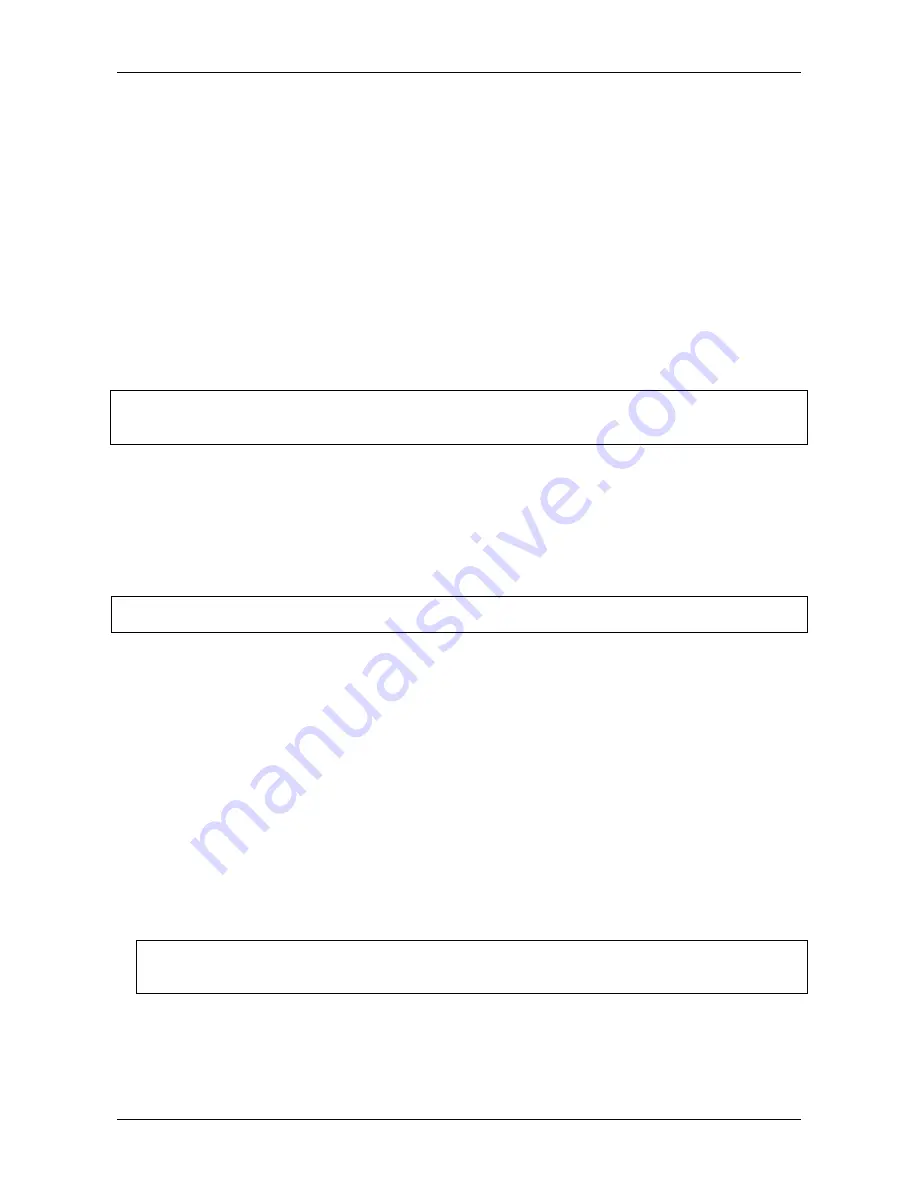
MONOLITE
19
7 OPERATION
7.1 OPERATION
CHECKS
The heating system must be used suitably, ensuring on the one hand, optimum combustion with reduced
emission to the atmosphere of carbon monoxide, hydrocarbons and soot, and on the other avoiding all dam-
age to persons and property.
The pressurisation must remain within the limit values shown in the technical data table.
The burner switch should always remain on; this ensures that the boiler water temperature remains near the
value set by the thermostat.
In the case of flue gas leaks from the front of the boiler (door and burner plate), the closure tie rods
of the single parts must be adjusted; if this is not sufficient, replace the gaskets.
WARNING
Do not open the door and do not remove the fume chamber while the burner is in operation. In all
cases wait a few minutes after stopping the burner for the insulation to cool.
7.2
TEMPORARY BOILER STOP
To stop the boiler temporarily, set the main switch on the control panel to “OFF”. The electrical parts will now
be free of tension.
7.3
PROLONGED BOILER STOP
Close the gas valve that is fitted upstream of the boiler.
WARNING:
during long stoppages in winter, and in order to avoid frost damage, drain both the sanitary wa-
ter* and the heating system water; drainage of the latter can be avoided by adding antifreeze.
Boiler with water heater
7.4
PERIODICAL USER CHECKS
-
Check periodically that there is no air in the heating system, and if necessary open the blow-off valve at
the top of the boiler.
-
Periodically check the boiler pressure.
7.5
MAINTENANCE AND CLEANING
All maintenance and cleaning can only be carried out only after closing the fuel supply and switching off the
electrical supply.
As economic operation depends on the cleanliness of the heat exchanger surfaces and on burner adjust-
ment, it is well to:
-
Have the burner settings checked by professionally qualified personnel;
-
Analyse the system water and allow for adequate water treatment to avoid the formation of cal-
careous incrustations that initially reduce boiler efficiency, and then lead to damage;
IMPORTANT
It is recommended to check periodically possible scale deposits through the side inspection
plugs (see par. Technical Data): if necessary, carry out chemical washing.
-
Check that the cladding and the flue gas sealing gaskets are in good order and if not, replace;
-
Periodically check the efficiency of the regulation and safety instruments on the system.
Summary of Contents for MONOLITE JB Series
Page 2: ......
Page 12: ...MONOLITE 10 4 3 1 SEALED HOT WATER HEATING SYSTEM WITH EXPANSION VESSEL Mod 45 125 Mod 160 270...
Page 23: ......