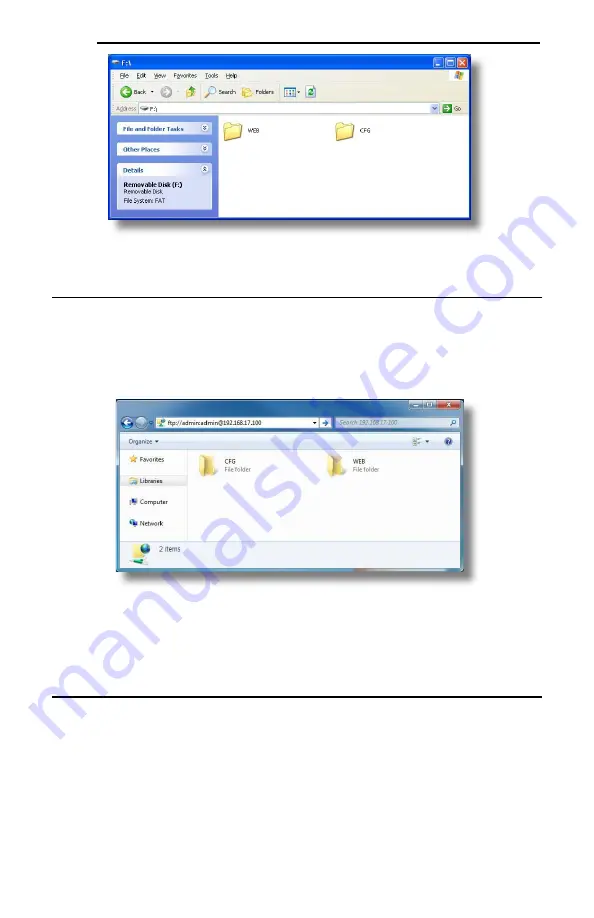
ICC
47
Figure 25: USB File Access via Windows Explorer
8.3
FTP with Windows Explorer
To use FTP with Microsoft Windows Explorer, first open either
“Windows Explorer” or “My Computer”.
Please note that the indicated procedure, prompts and capabilities outlined here can vary depending on
such factors as the installed operating system, firewalls and service packs.
In the “Address” field, type in “ftp://admin:admin@” and then the IP address of the target interface card
(if the user name and password have been changed from its default, then replace the first “admin” with
the new user name and the second “admin” with the password.) Refer to Figure 26.
Figure 26: FTP via Windows Explorer
Note that the behavior of Windows Explorer FTP will vary from PC to PC. If you are having issues
connecting FTP, there are other FTP client tools available such as Windows Command Prompt, Core
FTP, FileZilla, SmartFTP etc. that can also be used to reliably
access the card’s file system.
8.4
Loading New Web Server Content
The interface card’s web server resides in the file system and can be updated in the field. This section
will discuss how to update the web server.
Besides the new “WEB” folder containing the new web server, the update requires a USB or FTP
connection as described earlier in this section. To update the web server, complete the following steps:
1.
Navigate to the
card’s file system (see section 8.2 or 8.3).
2.
Backup the “WEB” folder if desired by copying it to the local computer.
3.
Delete the “WEB” folder from the card’s file system.
4.
Copy the new “WEB” folder to the card’s file system.