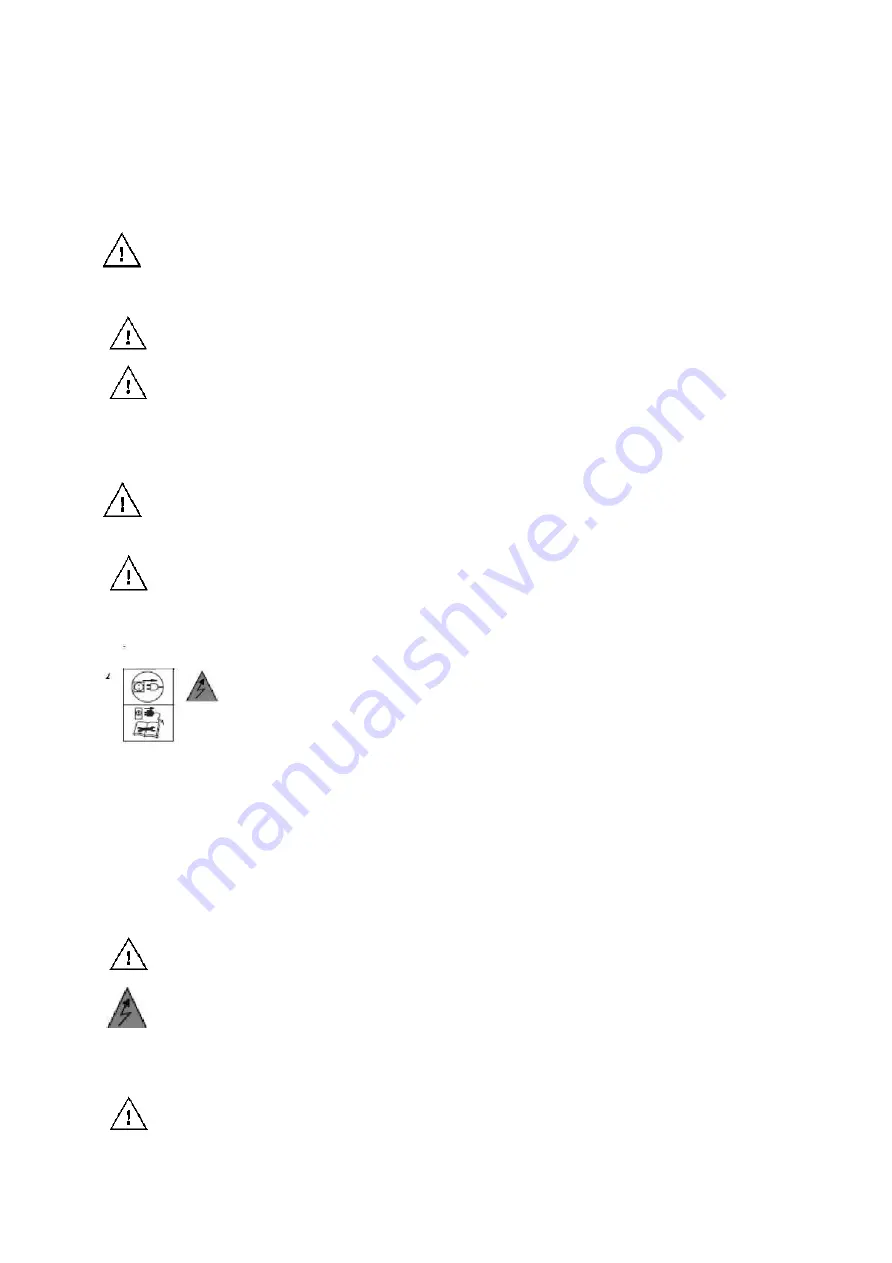
2
For these pumps the maximal sand content in water cannot exceed 5%. It must be
remembered that even the life of pumps with increased resistance against sand will be
significantly shorter when the pump will pump water with sand contamination. The wear and
tear of elements that pump sand is not subject to warranty repair. This is regarded as operating
wear and tear.
The pump is not adjusted to pump caustic, flammable, destructive or explosive substances
(e.g. petrol, nitro, oil, etc.), foodstuffs or salty water. Failure caused by pumping of the same
type of liquid is not subject to warranty repair.
The maximal temperature of the pumped water is 35
o
C.
The pump is not adjusted to pump water containing excessive amounts of mineral
elements causing deposition of scale on the pumping elements. The use of the pump in
such conditions results in premature wear and tear of the operating elements of the
pump. In such a case, only paid repair of the pump is available.
The pump cannot pump water containing oils and petroleum derivatives. The pump operation
in such water can lead to destruction of rubber elements, e.g. cables or sealing, and result in
leakage in the pump and motor failure. In such a case, only paid repair of the pump is
available.
Pumped water cannot contain any long-fibrous contamination.
PUMP INSTALLATION:
Prior to any installation works, power supply must be disconnected. Provide
security against accidental switch-on. Pumps 3ti, 3t2i, 3SDm, 4SD i 4SDm,
4ISP, 4ISPm, 6ISP, 3STm due to their dimensions can be delivered in two
elements. One element is a hydraulic part of the pump, the other is a motor.
Prior to connection of two elements, the clamping screws must be unscrewed
from the strip protecting the cable. Next, the screws clamping the strainer
must be unscrewed and the strainer removed. The clamping nuts with
washers must be unscrewed and removed. When the motor is placed in a
vertical position, the hydraulic element must be mounted on the motor shaft
ended with splines is placed in the clutch of the pump. If, in the course of
mounting, there are any difficulties with coupling, the motor shaft must be
turned to make the splines match the motor clutch. A hydraulic element,
correctly mounted on the motor, is fully supported by the top bearing body of
the motor. The aggregate prepared in this manner can be screwed with screw
nuts and washers. Screw nuts must be tightened crosswise. The minimal
moment of tightening screw nuts for motors 4” is 18 Nm.
If the screws are not tightened accurately, it can result in their unscrewing on operation
and motor “sinking” in the borehole. Upon installation of hydraulic element on the
motor, placing the power supply cable on the pump, the strainer must be installed and
screwed prior to the installation of the strip protecting the cable.
The lowering of the pump into the borehole without a surge protector can result in
destruction of cable isolation which can be the cause of pump failure or electrocution of
the operators.
For pumps SD, SDm, SCM, ISPm, ISP, STm, due to th necessity to ensure motor
cooling on operation, the diameter of a borehole where the pump operates cannot
exceed the values presented in the table below. The values are in mm. The diameters
are consistent with the pump efficiency.
Summary of Contents for 3SDm
Page 8: ......