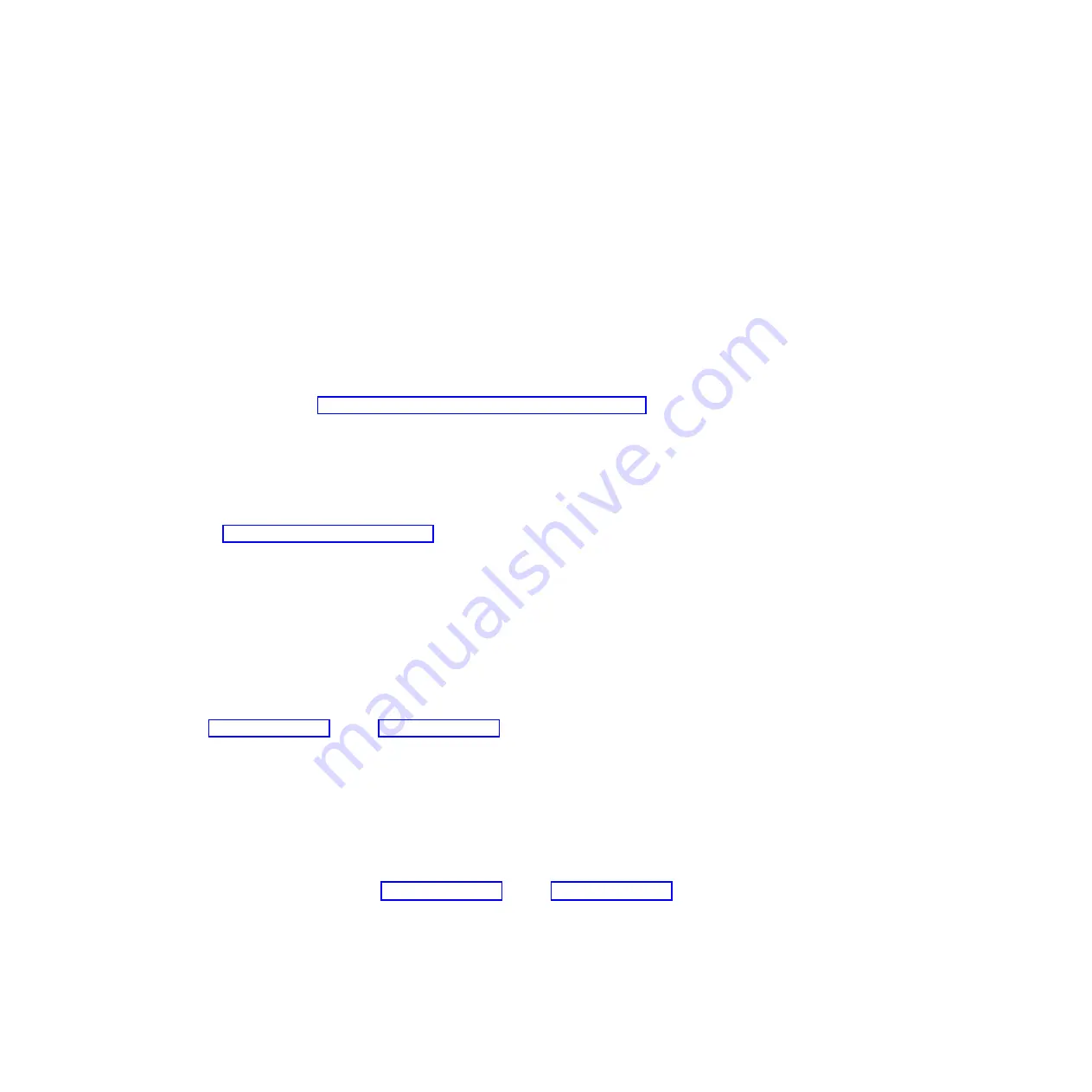
Water delivery specifications for secondary loops
This section describes the various hardware components that make up the delivery
system secondary loop that provides the chilled, conditioned water to the heat
exchanger. The delivery system includes pipes, hoses, and the required connection
hardware to connect the hoses to the heat exchanger. Hose management in
raised-floor and non-raised-floor environments is also described.
The heat exchanger can remove 100% or more of the heat load from an individual
rack when it is running under optimum conditions.
The primary cooling loop is considered to be the building chilled-water supply or a
modular chiller unit. The primary loop must not be used as a direct source of
coolant for the heat exchanger.
Procurement and installation of the components that are needed to create the
secondary cooling loop system are required for this design and are your
responsibility. See “Secondary cooling loop parts and services” on page 10 for
information about suppliers of hoses and coolant distribution units. The main
purpose of this section is to provide examples of typical methods of secondary loop
setup and operating characteristics that are needed to provide an adequate, safe
supply of water to the heat exchanger.
Attention:
The overpressure safety device must meet the following requirements:
v
Comply with
ISO 4126-1
(Information about obtaining this document is at
http://webstore.ansi.org/default.aspx. Search on document number
iso 4126–1
.)
v
Be installed so that it is easily accessed for inspection, maintenance, and repair
v
Be connected as close as possible to the device that it is intended to protect
v
Be adjustable only with the use of a tool
v
Have a discharge opening that is directed so that discharged water or fluid will
not create a hazard or be directed toward any person
v
Be of adequate discharge capacity to ensure that the maximum working pressure
is not exceeded
v
Be installed without a shutoff valve between the overpressure safety device and
the protected device
Figure 5 on page 16 through Figure 8 on page 19 show typical cooling solutions
with the most flexibility possible. Read the following guidelines before you design
the installation:
v
A method for monitoring and setting the total flow rate delivered to all of the heat
exchangers is required. This can be a discrete flowmeter that is built into the flow
loop or a flowmeter within the secondary loop of the coolant distribution unit
(CDU).
v
After you set the total flow rate for all of the heat exchangers by using a
flowmeter as previously described, it is important to design the plumbing so that
it provides the flow rate that you want for each heat exchanger and provides a
way to verify the flow rate. Figure 5 on page 16 through Figure 8 on page 19
illustrate the use of circuit setters to adjust the flow rate to each heat exchanger.
Other methods, such as inline or external flowmeters, can provide a more
accurate method for setting the flow rate through the individual shutoff valves.
14
Rear Door Heat eXchanger V2: Installation and Maintenance Guide
Summary of Contents for Rear Door Heat eXchanger V2
Page 1: ...Rear Door Heat eXchanger V2 Type 1756 Installation and Maintenance Guide...
Page 2: ......
Page 3: ...Rear Door Heat eXchanger V2 Type 1756 Installation and Maintenance Guide...
Page 38: ...28 Rear Door Heat eXchanger V2 Installation and Maintenance Guide...
Page 64: ...54 Rear Door Heat eXchanger V2 Installation and Maintenance Guide...
Page 90: ...80 Rear Door Heat eXchanger V2 Installation and Maintenance Guide...
Page 98: ...88 Rear Door Heat eXchanger V2 Installation and Maintenance Guide...
Page 101: ...website continued support line telephone numbers 79 Index 91...
Page 102: ...92 Rear Door Heat eXchanger V2 Installation and Maintenance Guide...
Page 103: ......
Page 104: ...Part Number 00D2434 Printed in USA 1P P N 00D2434...