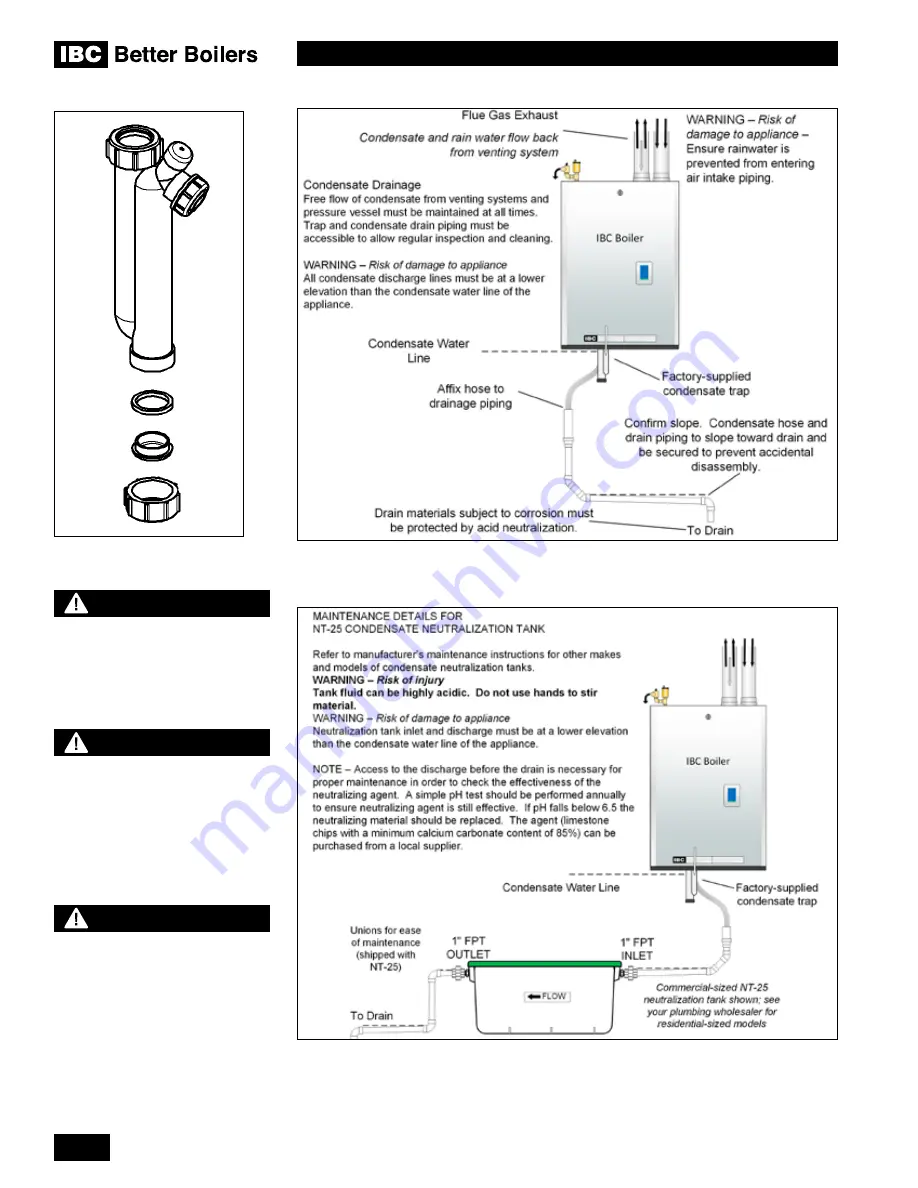
INSTALLATION AND OPERATION INSTRUCTIONS
1-20
SL 26-260 G3, SL 40-399 G3 MODULATING GAS BOILERS
Figure 25: Condensate neutralization tank
Figure 24 Condensate trap drainage
WARNING
If condensates are to be
discharged into building drain
piping materials that are subject
to corrosion, a neutralization
package must be used.
CAUTION
When a condensate
neutralization package
is installed, the pH of the
condensate discharge must be
measured on a regular schedule
to ensure the neutralizing agent
is active and effective.
Figure 23: Condensate trap
disassembly for cleaning
DANGER
The water in the condensate
neutralizer can cause severe
burns to the skin. Use extreme
caution when servicing the
condensate neutralizer. Wear
protective gloves and eyewear.