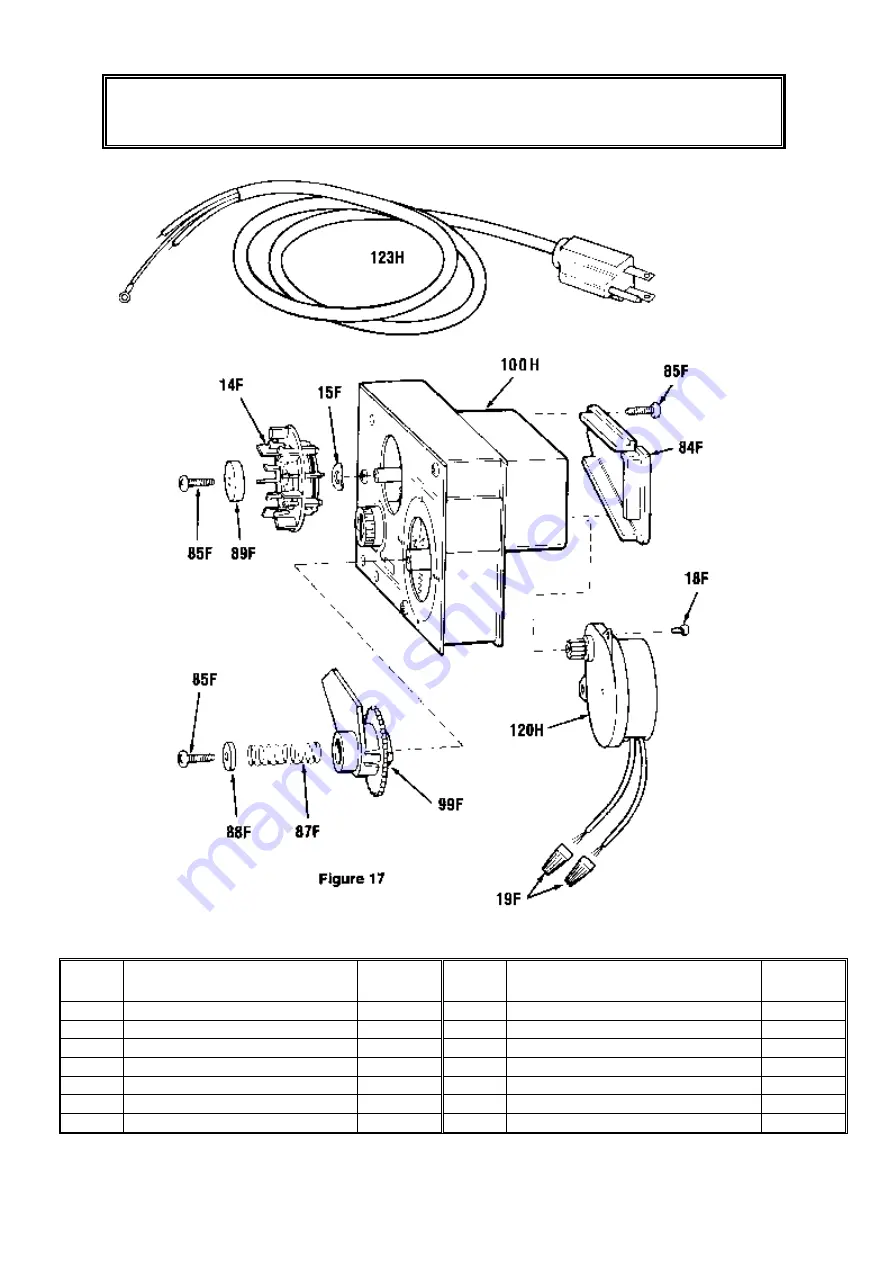
Page 27
TIMER REPLACEMENT PARTS
Item
Description
No.
Required
Item
Description
No.
Required
14F-6
6-Day skipper wheel assembly
1
87F
Spring
1
14F-7
7-Day skipper wheel assembly
1
99F-3
6-Day tripper gear
1
85F
Screw
2
99F-4
7-Day tripper gear
1
89F
Plastic washer
1
120H
Motor - specify voltage; frequency
1
15F
Bowed washer
1
18F
Screw - motor mounting
2
85F
Screw
1
19F
Wire nut
2
88F
Plastic washer
1
123H
Cord
1
Summary of Contents for AS30500
Page 13: ...Page 13 BRINE TANK SETUP ...
Page 14: ...Page 14 ...
Page 15: ...Page 15 Series 172 Commercial Industrial Control System Water Softener ...
Page 19: ...Page 19 ...
Page 20: ...Page 20 ...
Page 23: ...Page 23 ...
Page 25: ...Page 25 REPLACEMENT PARTS ...