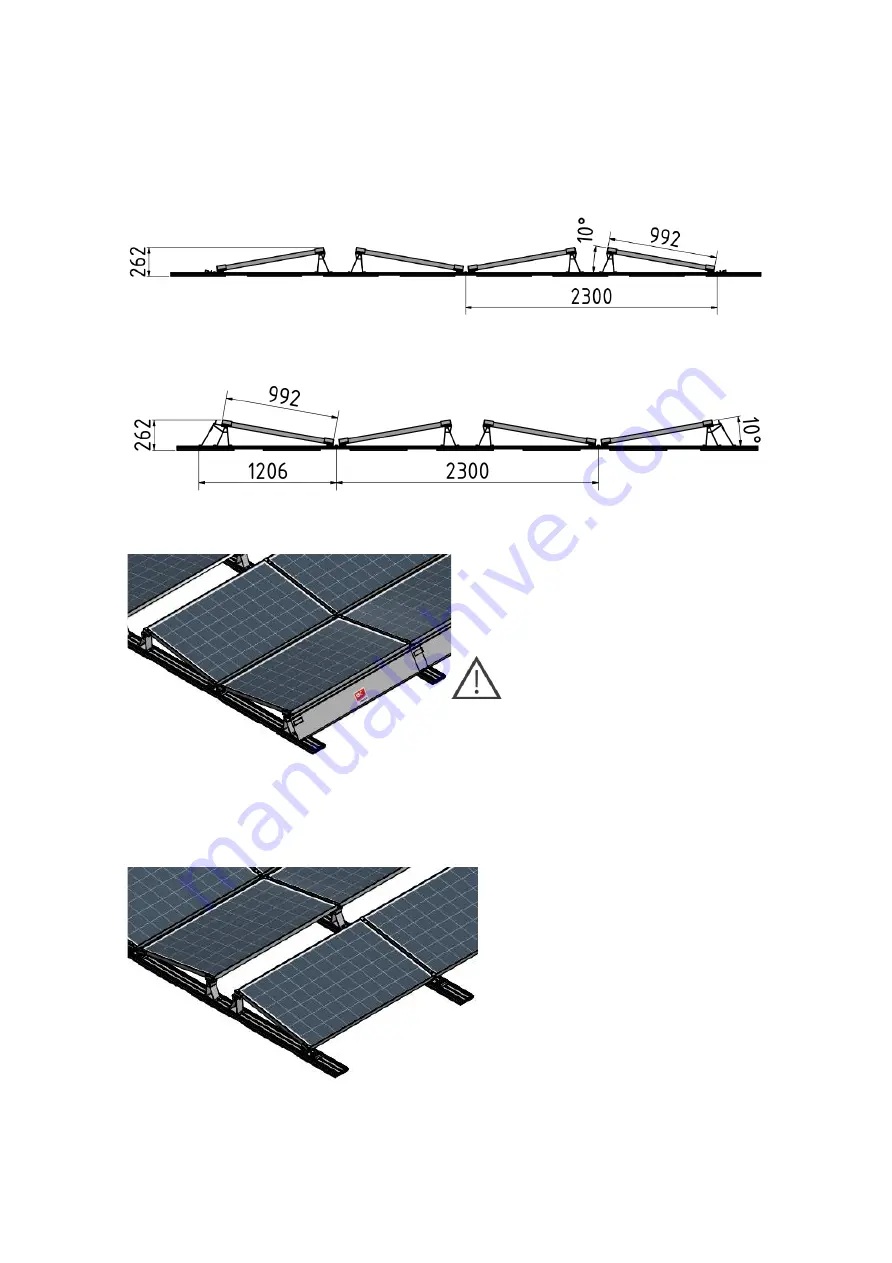
28
Version 20.01, 20-July-2020
AeroFix East-west orientation - AeroFix 10-EW
Determining the position of the supports
Define
the position of the „lower support“. The
distance from the leading edge of the base rail to
the „support bottom“ must be at least 1250 mm
when using a wind deflector.
Important information:
If you end with a wind plate you will need
the AeroFix 10-
S “support top” instead
the AeroFi 10-
EW “support top”
Define
the position of the “lower support”.
The “support bottom” must be fully supported
on the base rail.
Fig. 34 AeroFix 10-EW with wind plate finish
Fig. 33 AeroFix 10-EW with module finish
Fig. 35 AeroFix 10 with wind deflector finish
Fig. 36 AeroFix 10 with module finish
Summary of Contents for AeroFix Series
Page 1: ...1 Installation instructions IBC AeroFix AeroFlat Version 20 01 Date 20 July 2020...
Page 9: ...9 Version 20 01 20 July 2020 4 2 AeroFlat Parallel to the roof Fig 6 AeroFlat...
Page 17: ...17 Version 20 01 20 July 2020 Fig 15 Installation base rails Fig 16 Installation base rails...
Page 42: ...42 Version 20 01 20 July 2020 Fig 61 Wind plate assembly Fig 62 Fixation wind plate...
Page 53: ...53 Version 20 01 20 July 2020 Fig 81 Schematic system dimensions...
Page 68: ...68 Version 20 01 20 July 2020...
Page 71: ...71 Version 20 01 20 July 2020 13 4 Checklist IBC AeroFix...
Page 72: ...72 Version 20 01 20 July 2020...