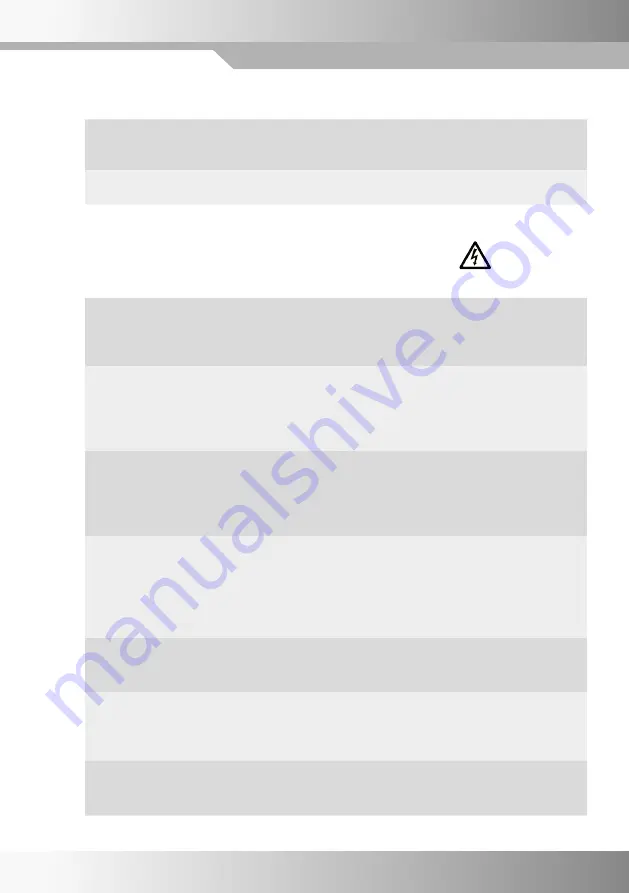
12
PUTTING THE EQUIPMENT INTO OPERATION
Should be done in sequence.
Check that
the motor rotates in the right direction in relation to the wheel's direction
of rotation.
In the event of a fault, switch two phases to the motor.
Setting max speed
Set the “High speed” DIP switch to the ON position.
Adjust "Max rpm" so that the wheel rotates at 10-12 rpm
(or as per wheel manufacturer directions).
After a test run, set the DIP switch to OFF.
Setting min speed
Set the “Low Speed” DIP switch in the ON position.
Adjust "Min rpm" so that the wheel rotates at 0.2-1 rpm
(or as per wheel manufacturer directions).
After a test run, set the DIP switch to OFF.
Checking the cleaning
function
Switch off the voltage.
Make sure the cleaning DIP switch is set to ON
and the input signal is disconnected.
When power is switched on, the wheel will rotate at minimum rpm for
10 seconds.
Checking the
rotation monitor
The yellow Rotation LED will flash when the magnet passes
the magnetic sensor, regardless of DIP switch position.
Setting the threshold
value
Make sure the control centre is connected. Jump "Run" 5-6.
Set the minimum output signal on the control centre.
If the rotor continues to turn, increase the threshold value until it stops.
Finish by
allowing the control unit to drive the wheel at maximum and minimum
rotation rpm and checking that wheel rpm is correct.
13
Check that
the DIP switch is set for the type of signal the control equipment outputs.
See “DIP switch” setting, page 7.
Check that
the cleaning function and rotation sensor DIP switch are set to ON.
Continued from previous page
Summary of Contents for MiniMax
Page 2: ......
Page 17: ...PERSONAL NOTES 15...
Page 18: ...16 PERSONAL NOTES...
Page 19: ...17 PERSONAL NOTES...