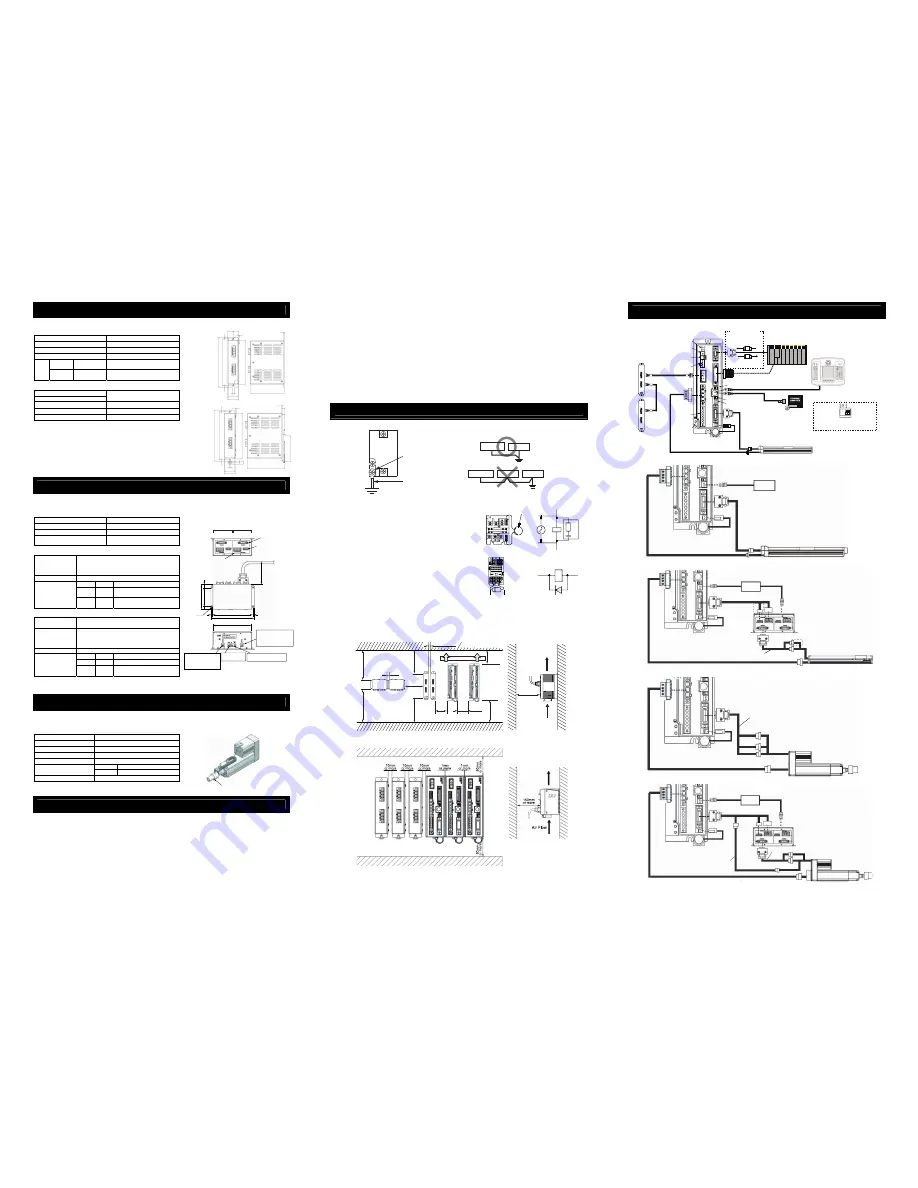
CB-RCS2-PLLA
RCS2-RA13R
(with Loadcel)
Absolute Battery
(for Absolute Type)
24V DC
Power Supply for Brake
Absolute Battery
(for Absolute Type)
Actuator
The following models are excluded:
•
RCS2-RA13R with brake or loadcell equipped
•
NS Actuators with brake equipped
24V DC
Power Supply for Brake
For LS (option)
Brake Box
CB-RCS2-PLA010
(enclosed to Brake Box)
For LS (option)
•
NS Actuators (with Brake
㧕
•
RCS2-RA13R (with Brake
㧕
Connect to back side
Absolute Battery
(for Absolute Type)
1 6 .8 5 17.15
1 .5
φ
5
4.
5
145
154
136
R2
.5
4.
5
1 0 6 .5
5
3 0 .7
3 4
1 .5
1 .5
Ø5
4.5
145
154
136
4.5
1 1 5
5
3 0 .7
3 4
1 .5
4
4
8 .5
(77 from DIN rail center)
(9)
Regenerative Resistor Unit (Option) : RESU(D)-1, RESU(D)-2
This is a unit that converts the regenerative current to heat when the motor decelerates.
[Specification]
[Appearance]
Item Specification
Body Size
W35.6mm
×
H158mm
×
D115mm
Body Weight
0.7kg
Internal Regenerative Resistor
235
Ω
80W
2nd unit
or later
RESU-1
RESUD-1
Controller Connection Cable
(Model Code CB-ST-REU010) 1m
Acce
s
so
rie
s
First Unit
RESU-2
RESUD-2
Controller Connection Cable
(Model Code CB-SC-REU010) 1m
[Reference Connectable Quantity]
Motor Wattage
Horizontal Mount/Vertical Mount
Connectable Number of
Regenerative Resistor Units
To 100W
(Note 3)
Not Required
101 to 400W
1
401 to 750W
2
(Note 1) This is a reference for the case when the actuator is ran
forward and backward on 1,000mm stroke with the operation duty 50%
under the rated acceleration/deceleration speed and rated load.
(Note 2) It is necessary to have the regenerative resistor listed above when the
operation duty is above 50%.
The maximum quantity of the external regenerative resistor units that
can be connected is as stated below:
•
2 units for less than 400W
•
4 units for 400W or more
(Note 3) It is necessary to have one unit for LSA/LSAS-N10S Type.
Brake Box (Option) : RCB-110-RA13-0
This is applied on NS Actuator and RCS-RA13R with brake.
1 unit of Brake Box possesses brakes for 2 shafts.
[Specification]
[Appearance]
Item Specification
Body Size
W162
×
H94
×
D65.5mm
Power Voltage and Current
24V DC
±
10% 1A
Connection Cable
Encoder Cable
(Model Code CB-RCS2-PLA010) 1m
[24V Power Supply Connector]
Connector on
Cable Side
(Enclosed in
standard package)
MC1.5/2-STF-3.5 (Phoenix Contact)
Applicable Cable
AWG28 to 16
Pin No. Signal
Explanation
1
0V
Power Supply Grounding for
Brake Excitation
Terminal
Assignment
2
24VIN
For Brake Excitation and
24V Power Supply
[Connectors 1 and 2 for external brake release switch connection]
Connected
Equipment
Brake Release Switch
Connector on
Cable Side
(Please prepare
separately)
XAP-02V-1
(Contact BXA-001T-P0.6) (JST)
Switch Rating
30V DC Minimum Current 1.5mA
Pin No. Signal
Explanation
1
BKMRL Brake Release Switch Input
Terminal
Assignment
2 COM
Power Supply Output for Brake
Release Switch Input
(Note) Short circuit of pin No. 1 and 2 of this connector releases the brake compulsorily.
Same as the brake release switch on SCON main unit, it is possible to release the brake.
Do not keep the compulsory release condition while in automatic operation.
Loadcell (Dedicated Option for SCON-CA)
This is the pressing force measurement unit that is used for the force control.
This is used by connecting to the actuator corresponding to the force control.
[Specification]
Item Specification
Loadcell System
Strain Gauge
Rated Capacity
20000N
Allowable Overload
200%R.C
*1
Loadcell Accuracy
±
1%R.C
*1
Zero
±
0.2%R.C/10
°
C
Temperature Drift
Output
±
0.1%R.C/10
°
C
Applicable Temperature Range
0 to 40
°
C
*1 R.C.: Rated Capacity
[Refer to RCS2-RA13R Instruction Manual for details of how to attach and the dimensions.]
Installation Environment, Storage Environment
This product is capable for use in the environment of pollution degree 2
*1
or equivalent.
*1 Pollution Degree 2: Environment that may cause non-conductive pollution or transient conductive
pollution by frost (IEC60664-1)
1. Installation Environment
Do not use this product in the following environment
•
Location where the surrounding air temperature exceeds the range of 0 to 40
°
C
•
Location where condensation occurs due to abrupt temperature changes
•
Location where relative humidity exceeds 85%RH
•
Location exposed to corrosive gases or combustible gases
•
Location exposed to significant amount of dust, salt or iron powder
•
Location subject to direct vibration or impact
•
Location exposed to direct sunlight
•
Location where the product may come in contact with water, oil or chemical droplets
•
Environment that blocks the air vent [Refer to Installation and Noise Elimination]
When using the product in any of the locations specified below, provide a sufficient shield.
•
Location subject to electrostatic noise
•
Location where high electrical or magnetic field is present
•
Location with the mains or power lines passing nearby
2. Storage and Preservation Environment
The storage and preservation environment should comply with the same standards as those for the
installation environment. In particular, when the machine is to be stored for a long time, pay close
attention to environmental conditions so that no condensation forms. Unless specially specified,
moisture absorbency protection is not included in the package when the machine is delivered. In
the case that the machine is to be stored and preserved in an environment where condensation is
anticipated, take the condensation preventive measures from outside of the entire package, or
directly after opening the package.
Installation and Noise Elimination
1. Noise Elimination Grounding (Frame Ground)
2. Precautions regarding wiring method
1) Wire is to be twisted for the 24V DC power supply.
2) Separate the signal and encoder lines from the power
supply and power lines.
3. Noise Sources and Elimination
Carry out noise elimination measures for power devices on
the same power path and in the same equipment.
The following are examples of measures to eliminate noise
sources.
1) AC solenoid valves, magnet switches and relays
[Measure] Install a Surge absorber parallel with the coil.
2) DC solenoid valves, magnet switches and relays
[Measure] Mount the windings and diodes in parallel.
Select a diode built-in type for the DC relay
4. Heat Radiation and Installation
Design and Build the system considering the size of the controller box, location of the controller and
cooling factors to keep the ambient temperature around the controller below 40
°
C. Apply screws sized
M4 × 10mm when attaching the product with screws.
SCON-C/CA
SCON-CAL/CGAL
Connection Diagram
SCON-C/CA
●
Standard
●
For Models Equipped with brake Except for RCS2-RA13R and NS Actuators
●
RSC2-RA13R Equipped with Brake, with no Loadcell, or NS Actuators with Brake
●
RCS2-RA13R Equipped with no Brake, with Loadcell in SCON-CA
●
RCS2-RA13R Equipped with Brake and Loadcell in SCON-CA
Attached to RCS2-RA13R
Loadcell
94
70
12
5
5
152
162
142
4-
φ
5
LS Input Connector
Encoder Input Connector
Encoder Output Connector
Primary
Shaft
min100
12
Connector 2 for
External Brake Release
Switch Connection
(for the primary shaft)
Power Supply
Input Connector
POWER ON LED
(turns in green while on)
Connector 2 for
External Brake Release
Switch Connection
(for the secondary shaft)
Secondary
Shaft
CB-LDC-LTL
CB-RCS2-PLLA
RCS2-RA13R
(with Loadcell and Brake)
CB-RCS2-PLA (enclosed to Brake Box)
24V DC
Brake Box
RCB-110-RA13-0
Connect to back side
Absolute Battery
(for Absolute Type)
Power Supply for Brake
10mm or more
50mm
or more
50mm
or more
50mm
or more
50mm
or more
50mm
or more
50mm
or more
100mm
or more
30mm
or more
10mm
or more
100mm
or more
150mm
or more
Air Flow
Air Flow
Fan
Brake Box
Regenerative
Resistor Unit
Place a fan to make the
ambient temperature even
Earth Terminal
Connect using FG connection
terminal on the main unit.
Copper Wire :
Connect to an ground cable with
diameter 1.6mm or more.
Controller
Class D grounding
(Formerly Class-III grounding :
Grounding resistance at 100
Ω
or less)
Do not share the ground wire with or connect
to other equipment. Ground each controller.
Controller
Other
equipment
Controller
Other
equipment
Other
equipment
Surge absorber
Relay
coil
Relay coil
R
C
+24V
0V
+24V
0V
+
-
Screw
Attachment
Type
RESU-1
RESU-2
DIN rail
Attachment
Type
RESUD-1
RESUD-2
Regenerative Resistor Unit
(REU-2 : option)
Required depending
on usage condition
LED Indication
Axis Number
Setting Switch
Pulse Train Mode
Changeover Switch
System
I/O Connector
CB-SC-REU010
CB-ST-REU010
Regenerative Resistor Unit
(REU-1 [for secondary unit] : option)
Power Supply
Connector
FG Connection
Terminal
Absolute Battery
(for Absolute Type)
Mode Changeover Switch
Brake Release Switch
Brake Power Supply Connector
AK-04 (option)
Converts PLC open
collector output into
differential pulse output
JM-08 (option)
Converts SCON differential
pulse output into open
collector output
Flat Cable
(Accessories)
PLC
(Please prepare separately)
Touch panel teaching (option)
or Teaching pendant (option)
PC Software (option)
Detail View of Pulse Train Mode Changeover Switch
Pulse Train Mode Changeover Switch No. 1
ON: to select Pulse Train Control Mode
OFF: to select Positioner Mode
Actuator
The following models are excluded:
·
RCS2-RA13R with brake or loadcell equipped
·
NS Actuators with brake equipped
AK-04
JM-08
Wiring for Pulse
Train Control Mode
SW
ADRS
1 2
ON
↓