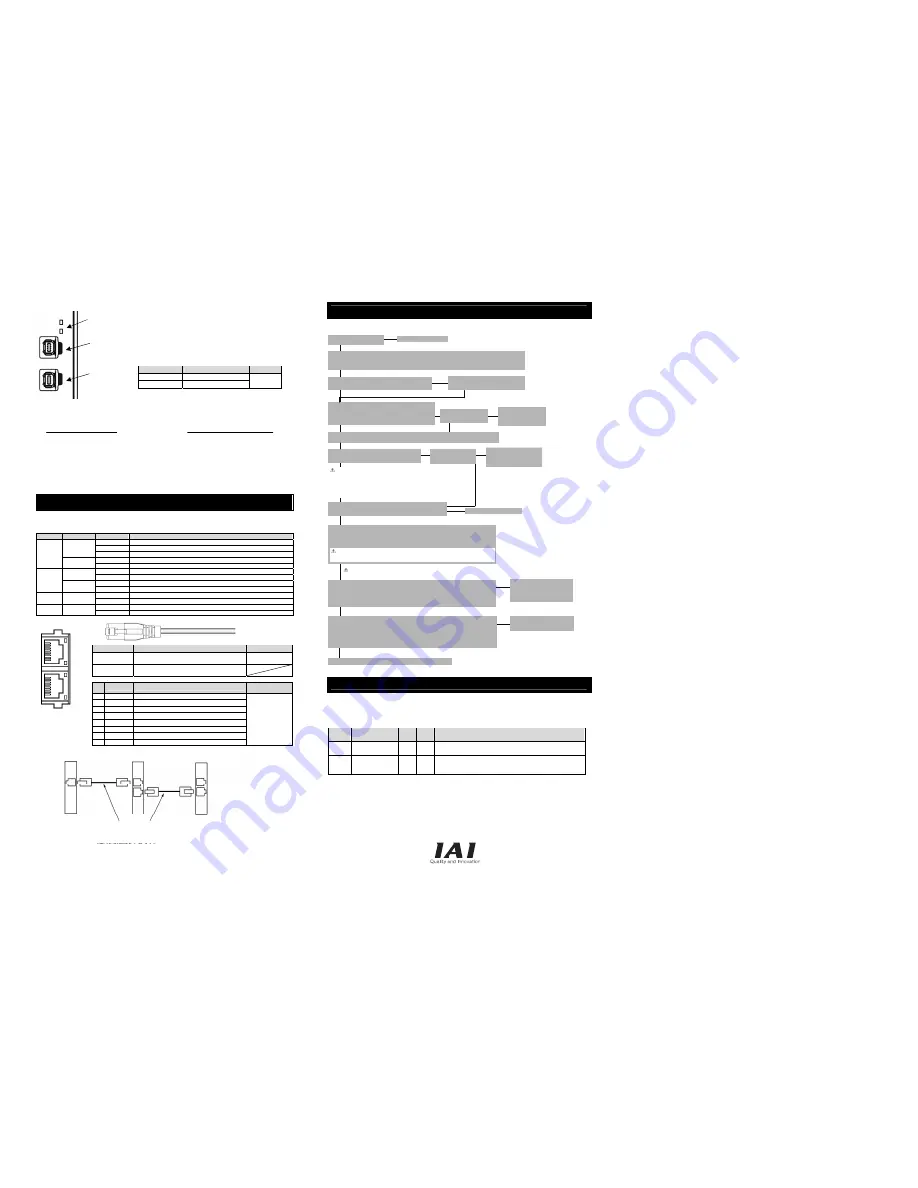
●
Interface Area
●
Node Address Setting
Node address can be set with the parameter.
Set Parameter No. 85 “NADR : Fieldbus Node Address” with using the
PC software for RC.
Available range for Setting : 3 to 239 [hex] (setting at delivery : 3)
●
Data Length Setting
Establish the setting in Parameter No. 86 “FBRS : Fieldbus
Communication Speed” in RC PC software considering the data length
to be used.
Setting Value
Data Length
Baud Rate
0 32
bytes
1 (at the delivery)
48 bytes
100Mbps
●
Electronic Gear Ratio
Setting
Set the electronic gear numerator in Parameter No. 65 “CNUM : Electronic Gear Numerator” and the electronic gear
denominator in No. 66 “CDEN : Electronic Gear Denominator”. In the RC PC software
Establish the settings to satisfy the following condition:
Stroke [mm]
Electronic Gear Ratio Denominator
Ball Screw Lead Length [mm]
Electronic Gear Ratio Numerator
●
Pulse Count Direction Setting
Set the value in Parameter No. 62 “FPIO : Pulse Count Direction” to be the same as what is set in No. 5 “ORG :
Home-Return Direction” in the RC PC software.
(Note)
Reboot the power on the controller after the parameter settings are completed, and make sure to put the
switchover switch on the front face of the controller back to the AUTO side.
●
Wiring
Connect the dedicated cable for MECHATROLINK.
CC-Link IE (Dedicated for SCON-CB/CGB)
●
Specification
Refer to the CC-Link IE Instruction Manual
●
Status LED
LED
Color
Illumination Status
Explanation
Steady Light
Cyclic transmission in process
Blinking
Cyclic transmission paused
GN: D LINK
Off
Cyclic transmission not conducted, parallel off, Power not supplied
Steady Light
Received data in error
NS
OR: L ERR
Off
Received data in normal conditions, Power not supplied
Steady Light
Operation in normal conditions
GN: RUN
Off
Hardware error occurred, Power not supplied
Steady Light
Error being occurred (Node Error / Station Number Setting Error)
MS
OR: ERR
Off
Operation in normal conditions, Power not supplied
Steady Light
Linkup in process
LINK GN
Off
Link-down in process, Power not supplied
Steady Light
Received data in error
L.ER OR
Off
Received data in normal conditions, Power not supplied
●
Interface Area
Connector Name
CC-Link IE Connector
Remarks
Cable Side
Ethernet ANSI/TIA/EIA-568-B Category 5e and above
8P8C modular plug equipped with shield (RJ45)
Please prepare
separately
Controller Side
Ethernet ANSI/TIA/EIA-568-B Category 5e and above
8P8C modular Jack equipped with shield (RJ45)
Pin
No. Signal Name
Description
Applicable cable
diameter
1 TP0+
Data
0+
2 TP0-
Data
0-
3 TP1+
Data
1+
4 TP2+
Data
2+
5 TP2-
Data
2-
6 TP1-
Data
1-
7 TP3+
Data
3+
8 TP3-
Data
3-
It is recommended to
prepare a straight
STP cable in
Category 5e or above
for the Ethernet
cable.
●
Wiring
Starting Procedures
When using this product for the first time, make sure to avoid mistakes and incorrect wiring by referring to the
procedure below. “PC” stated in this section means “PC software”.
Trouble Shooting
In the case an error is occurred, check the operation status on the LED display on the front panel [Refer to
Each Fieldbus Section], and also, check the status monitor by connecting a teaching tool such as PC software
for RC.
Either of the following alarms will be shown for Fieldbus. Please refer to the Instruction Manual of the controller
for other alarms to perform an appropriate treatment.
Code
Error Name
ID
(*1)
RES
(*2)
Cause / Treatment
0F2
Fieldbus
Module Error
05
×
Cause
: An error is detected on Fieldbus module
Treatment : Check on the parameter
0F3
Fieldbus Module
Not Detected
04
×
Cause
: Module cannot be detected
Treatment : Turn the power off and reboot. Please contact us
if the problem is not solved with this action.
(*1) ID
→
Simple alarm code
(*2) RES
→
Alarm reset available/unavailable
○
: Alarm reset available / ×: Alarm reset unavailable
Manual No.: ME0260-9A
CON
ERR
Status LED
Upstream Side
LK1 (link 1)LED
Downstream
Side
LK2 (link 2)LED
×
No. of Encoder Pulses
×
≤
2
31
* Refer to instruction manual of operation
for servo press type.
Top View of
Connector on
Controller side
L.ER
LINK
L.ER
LINK
Master Unit
Slave Devices
SCON CC-Link IE Type
Ethernet Straight Cable Category 5e or more
Double shielded cable braided with aluminum foil recommended
(Note) Terminal resistance is not required
There is no distinction
of IN/OUT on the
connector.
→
No →
→
No →
↓ Yes
No →
→
Check the emergency stop circuit.
→
No →
↓ Yes
↓ Yes
↓ Yes
→
Yes
Check of Packed Items
Are there all the delivered items?
Please contact the distributor.
Point Check Item
• Is frame ground (FG) connected?
• Has the noise countermeasure been taken?
Power Supply and Alarm Check
Connect a teaching tool such as PC, turn the mode changeover
switch to “MANU” side and turn the power on for each unit.
Select [Teaching Mode 1 Safety Speed Activated / PIO
Operation Invalid] in the teaching tool such as PC.
Check Item
Is the orange light [ALM] on
the LED status display off?
Connect the PC or teaching
pendant and check the
content of the alarm to have
the right treatment.
Safety Speed Setting
Set it in Parameter No. 35 if necessary. The safety speed is set to 100mm/s at the delivery.
Servo ON
Turn the servo on with the operation on the teaching
tool such as PC.
Check Item
Is the green light [SV] on
the LED status display on?
If an alarm is generated, connect
the PC or teaching pendant and
check the content of the alarm to
have the right treatment.
CAUTION
Please perform this process with the actuator away from the mechanical end or
interfering subjects as much as possible.
Put the actuator away if it interferes with surroundings. It may generate an alarm if the
actuator hit the mechanical end or interfering subjects when the servo is turned on.
The slider may get slightly dropped by self-weight if servo on and off is repeatedly
performed at the same position. Be careful not to pinch the hand or damage the work.
Safety Circuit Check
Does the emergency stop circuit (drive cutoff circuit) work properly and
turn the servo off?
Target Position Setting (This section is not necessary for □□ Direct Mode and MECHATROLINK-
III
.)
Set the target position in “Position” Box in each position table.
Perform a home-return operation first when Direct Teaching is to be performed. When moving the
actuator manually, set the Brake Release Switch to “BK RLS” side for the brake equipped type.
Put the switch back after the setting is complete.
CAUTION
To ensure safety, it is recommended that safety speed be enabled during initial movements.
If there is a vibration or abnormal
noise generated, check the actuator
if it is installed properly, the condition
for its use is below the rated
values, etc.
Test Run Adjustment
1) Check the operation with setting the safety speed invalid on the teaching tool such as PC software.
2)
Select “Monitor Mode 2 Safety Speed Invalid / PIO Available to Boot” in MANU
Operation Mode and remove the PC or teaching pendant from the controller.
3) Set the Mode Changeover Switch to “AUTO” side.
4) Conduct the Fieldbus setting on the host side.
Check Item
Turn on the power to the host side. Is the LED display on the front panel as shown below for each
Fieldbus?
CC-Link : STATUS 1 is off and STATUS 0 is turned on in green
DeviceNet and CompoNet : Both MS and NS are turned on in green
PROFIBUS, MECHATROLINK
I
and
II
: Both STATUS1 and STATUS0 are turned on in green.
Either of MECHATROLINK
III
- LK1 or LK2 is turned on in green
Now it is ready for operation. Proceed to the system operation adjustment.
↓ Yes
No
Installation and Wiring
Install and wire the actuator and the controller following the
instructions described in the Instruction Manual and this guide.
Initial Operation Check
Connect our controller to the actuator.
Connect a teaching tool such as PC, set the operation mode setting switch to “MANU” side and turn the power on.
Confirm the operation by performing a home-return operation and jog operation in full stroke range on the teaching tool.
↓
CAUTION
Be careful not to pinch the hand or damage the mechanical hand by the slider dropped with the
self-weight when turning the brake release switch to “BK RLS” side if it is mounted vertically.
↓ Yes
→ • Check the station number setting.
• Check the terminal resistor.
• Check the baud rate setting.
No