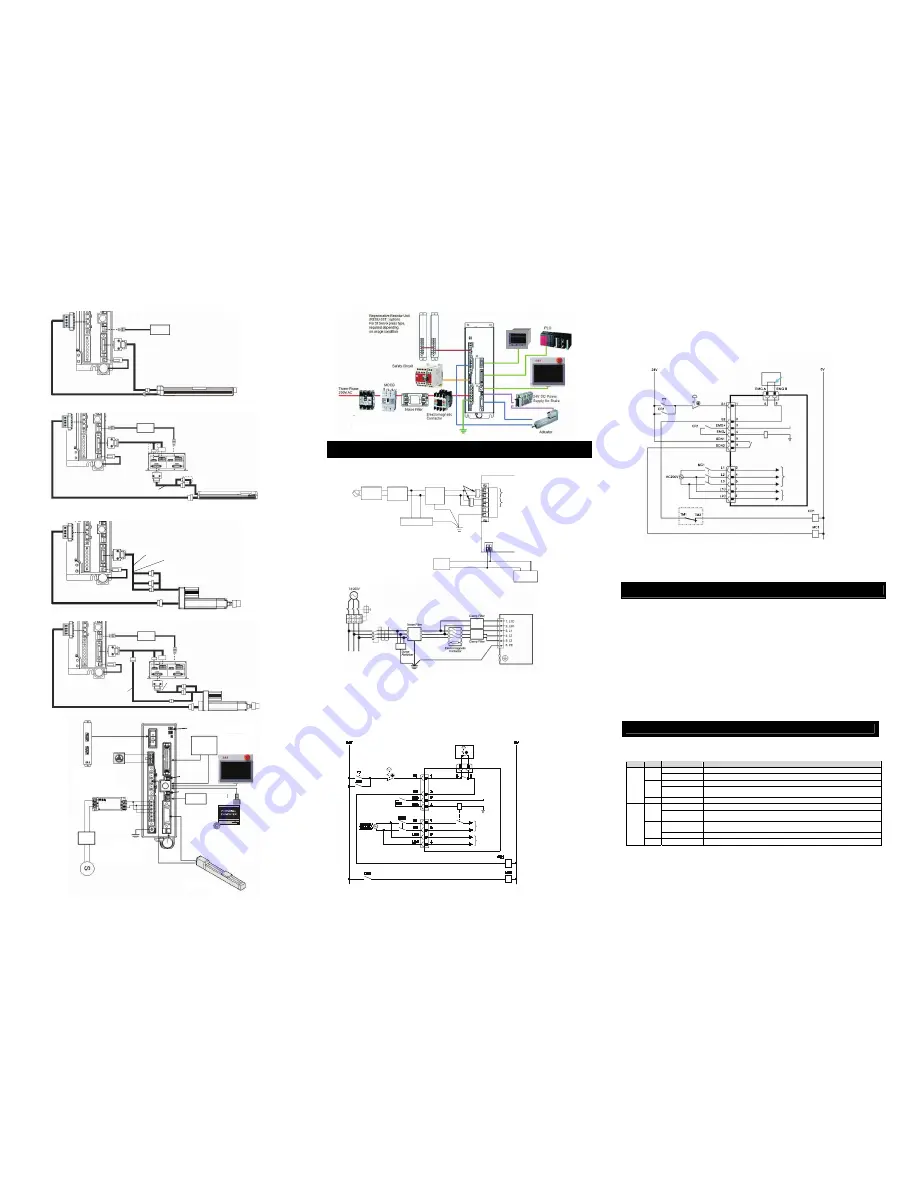
NF
*3
SK
*2
+24V
0V
L1
L2
L1C
L2C
NC
PE
BK
+
PWR
-
100V AC
or
200V AC
(Refer to Controller
Power Voltage Specifications)
Circuit
Breaker
Ground Fault
Circuit
Interrupter
CLF
*1
Class D grounding
(Formerly Class-
Ⅲ
grounding)
24V DC
Power
Supply
SCON
AC Power Supply
Input Connector
B. Motor Power Supply
A. Control Power Supply
Brake Power Supply
Input Connector
Brake
Release Box
Emergency
stop reset
switch
Emergency
stop switch
Cable for PC software
or dummy plug
Short-circuit in the
cable for PC software
System I/O connector
SIO connector
(Note 1)
(Note 1)
(Note 2)
(Note 3)
(Note 4)
Motor power
supply
Control power
supply
Temperature sensor contact
of external regenerative resistor
AC power supply
input connector
Emergency
stop circuit
exclusive use
24V
Stop Circuit
Contact output for the
external drive cutoff
SCON-CGB
Circuit Breaker
Leakage Breaker
EMG Switch
Regenerative
Resistor Unit
Required depending
on usage condition
Noise Filter
Necessary to
noise prevention
Host
Controller
System
Circuit Breaker
Select and connect a circuit
breaker that can apply to
the capacity of controller
Actuator
PC Software
<RCM-101-USB>
Optional
PC
24V DC
NFB
Absolute
Battery
Brake for
Power Supply
Teaching Pendant
LED Display
Mode
Changeover
Switch
Brake Release Switch
Communication
Cable
Teaching Tool
Power Cutoff Breaker
As SCON-CGB for 3000 to 3300W does not have
the drive cutoff circuit, make sure to establish
cutoff externally.
Load Display
Device etc.
Communication
Cable
●
For Models Equipped with brake Except for RCS2-RA13R and NS Actuators
●
RSC2-RA13R Equipped with Brake, with no Loadcell, or NS Actuators with Brake
●
For RCS2-RA13R equipped with no brake and with loadcell for SCON-CA/CB/CGB or for when connecting
the servo press actuator to CB/CGB Servo Press Type
●
RCS2-RA13R Equipped with Brake and Loadcell in SCON-CA/CB/CGB
SCON-CAL/CGAL
SCON-CGB (For 3000 to 3300W Motor)
Power Supply and Emergency Stop Circuit
●
Wiring for Power Supply (to be prepared by customer)
SCON-C/CA/CAL/CGAL/CB/CGB (For ~750W Motor)
SCON-CGB (For 3000 to 3300W Motor)
Power consumption varies depending on the connected actuator, etc. Select the circuit breaker that suits to the specification.
[Refer to Basic Specifications]
A ground fault circuit interrupter needs to be selected carefully considering the purposes of prevention of fire and protection of
human. Use the “harmonic type” for the ground fault circuit interrupter. Also, check the leak current at the set points.
Refer to the instruction manual for the recommended models for the noise filter, clump filter and surge absorber.
●
Wiring for Emergency Stop Input
The following diagram shows an example of how the emergency stop switch for the teaching pendant may
be included in the emergency stop circuit you may construct.
SCON-C/CA/CAL/CGAL/CB/CGB (For ~750W Motor)
Note 1 The power rating of the motor power-off relay turning ON/OFF with contact CR1 is 24V DC and 10mA or less.
Note 2 Connect such as a connector to L1/L2 terminals when cutting off the motor power source externally.
Note 3 CGAL/CGB Types are not equipped with a relay to enable to automatically identify a teaching tool was inserted and
switch the wiring layout. (The system I/O connector does not get short-circuited between S1 and S2 terminals even if
a teaching tool is removed. Connect the enclosed dummy plug DP-5 to the SIO connector when it is necessary to
have short-circuit.) The controller on except for CGAL/CGB Types automatically identifies that a teaching tool was
inserted. (Short-circuit is made between S1 and S2 terminals inside the controller once connection is detected.)
Note 4 Since there is no motor power cutoff relay in CGAL/CGB Types, make sure to establish a cutoff relay externally.
SCON-CGB (For 3000 to 3300W Motor)
Note 1 The power rating of the motor power-off relay turning ON/OFF with contact CR1 is 24V DC and 10mA or less.
Note 2 Connect such as a connector to L1/L2/L3 terminals when cutting off the motor power source externally.
(This controler not equipped with the drive cutoff relay mounted inside the controller.)
Note 3 It is the contact output to control the drive source breaker connected externally. The rating is 30V DC and 20mA or less.
Note 4 Connect a temperature sensor when an external regenerative resistor unit is connected.
Operation Modes and Functions (other than MECHATROLINK-
Ⅲ
)
(Note) Refer to the Section for MECHATROLINK-
Ⅲ
for the operation modes and features of MECHATROLINK-
Ⅲ
.
SCON-C Type is available for the operation of Remote I/O Mode.
SCON-CA/CB/CGB Type is available for all the operation modes in the next table.
SCON-CAL/CGAL Type is available for the operations in the modes except for those in the shaded area in the next table.
The following operation modes are available to select for the operation.
(1) Remote I/O Mode
: This is the mode to perform operation by PIO (24V I/O) with Fieldbus.
(2) Position /
: This is the mode to perform operation by indicating the target position by inputting the value directly.
Simple Direct Mode The values of the position data already registered for the speed, acceleration/deceleration and
positioning band are to be used in this mode.
(3) Semi-Direct Mode
: This is the operation mode to indicate the speed, acceleration/deceleration and pressing
current, as well as the target position, by inputting the values directly.
(4) Full-Direct Mode
: This is the operation mode to indicate all related to the position control by inputting the values directly.
(5) Remote I/O Mode 2 : This is the mode that the function to read the current position and the current speed is added to Remote I/O.
(6) Position /
: This is the mode corresponding to the force control function instead of the teaching and zone
Simple Direct Mode 2 functions in (2).
(7) Semi-Direct Mode 2 : This is the mode that enables to read the loadcell data instead of reading the command current value in (3).
(8) Remote I/O Mode 3 : This is the mode that the function to read the current position and loadcell data is added to (1) functions.
(9) Semi-Direct Mode 3 : This is the mode that equips the vibration control function instead of the jog function in (3).
(10) Full Functional Mode
: It is a mode dedicated for the servo press type.
DeviceNet
●
Specification
Refer to the DeviceNet Instruction Manual [ME0256 : CA/CB Type, ME0124 : C Type]
●
LED Indicators for Monitoring
LED
Color Illumination Status
Explanation
Steady Light
In normal operation
GN
Blinking
A hardware error occurred. Condition sometimes recovers after the power reboot.
Steady Light
A hardware error occurred. Board must be replaced.
OR
Blinking
An error occurred in the user settings. It is just a simple error such like configuration
error. It can be recovered with a rebuild of the settings.
MS
−
Off
Power is not supplied during DeviceNet initializing.
Steady Light
Connection is established and the communication under normal condition
GN
Blinking
Online but network connection is not yet established. Communication is stopped.
(Network is in normal condition)
Steady Light
Node address duplication or bus-off state was detected. Communication is not
possible.
OR
Blinking
Communication error (Communication time-out is detected.)
NS
−
Off
Not online. DeviceNet Power is not supplied.
24V DC
Power Supply for Brake
Absolute Battery
(for Absolute Type)
Actuator
The following models are excluded:
•
RCS2-RA13R with brake or loadcell equipped
•
NS Actuators with brake equipped
24V DC
Power Supply for Brake
For LS (option)
Brake Box
CB-RCS2-PLA010
(enclosed to Brake Box)
For LS (option)
•
NS Actuators (with Brake
㧕
•
RCS2-RA13R (with Brake
㧕
Connect to back side
Absolute Battery
(for Absolute Type)
CB-LDC-LTL
CB-RCS2-PLLA
RCS2-RA13R
(with Loadcell and Brake)
CB-RCS2-PLA (enclosed to Brake Box)
24V DC
Brake Box
RCB-110-RA13-0
Connect to back side
Absolute Battery
(for Absolute Type)
Power Supply for Brake
Motor Power
Cutoff Relay
Motor power
supply
Control power
supply
(Note 3)
(Note 1)
(Note 1)
(Note 2)
(Note 4)
System I/O connector
SIO connector
EMG A
EMG B
Emergency
stop reset
switch
Emergency
stop switch
Emergency stop switch
for the teaching pendant
Emergency
stop circuit
exclusive use
24V
AC power supply
input connector
CB-RCS2-PLLA
RCS2-RA13R
(with Loadcel)
Absolute Battery
(for Absolute Type)
* For RCS3 servo press actuator:
It should be CB-RCS2-PLDA, and
cable should be 3 branched → 2 branched.