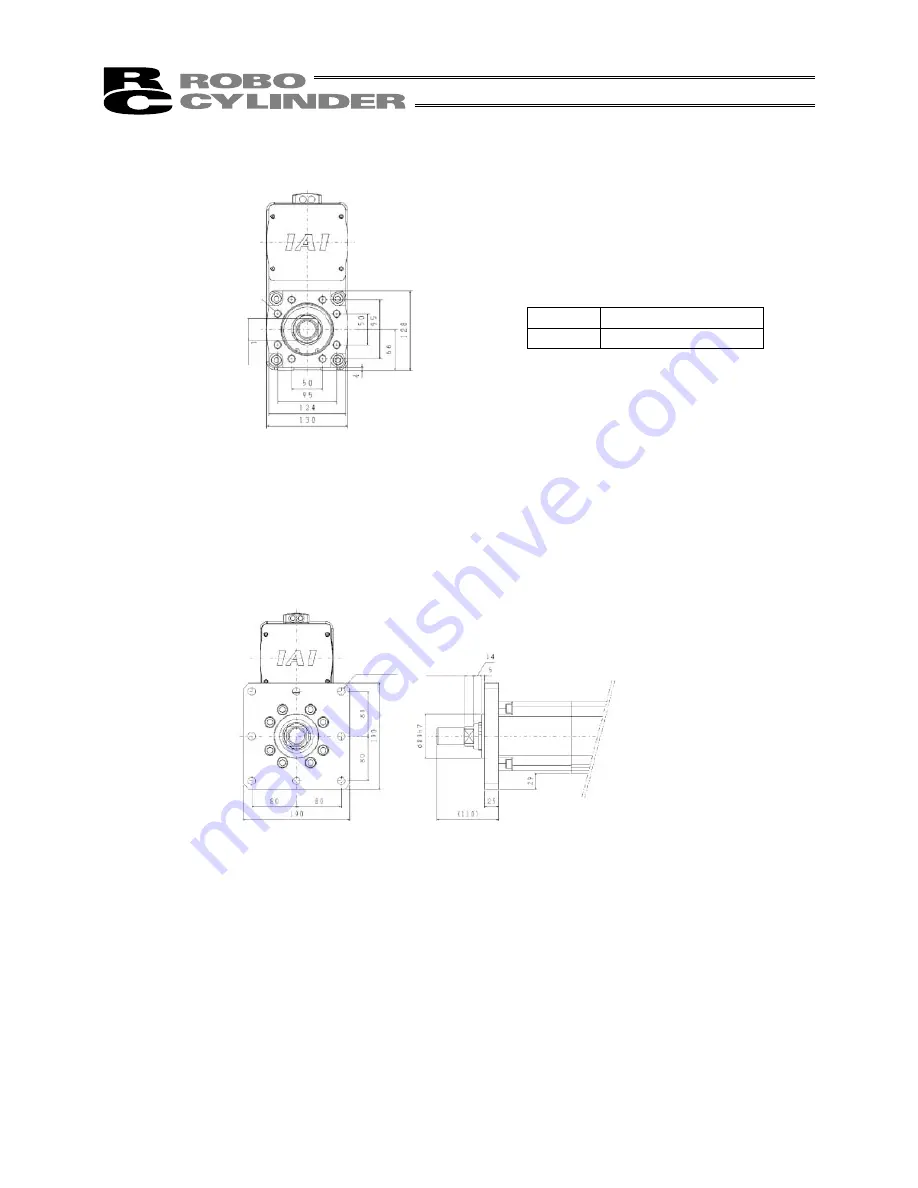
9
(2) Using the tapped holes on the rod side
Tap size
Maximum thread length
M12 24
mm
Tapped holes are provided on the rod side for mounting. You can use these tapped holes to install the
actuator. The maximum thread length of rod mounting screws is specified above. Make sure the bolt ends
do not project through the holes.
(3) Using a flange (optional) with screws
An optional flange is available. You can use this flange to install the actuator.
8-M12, depth 24
36 ac
ro
s
s
fla
ts
(w
id
th
a
c
ro
ss
fl
a
ts)
8-13, 5 drilled
16 (width across flats)