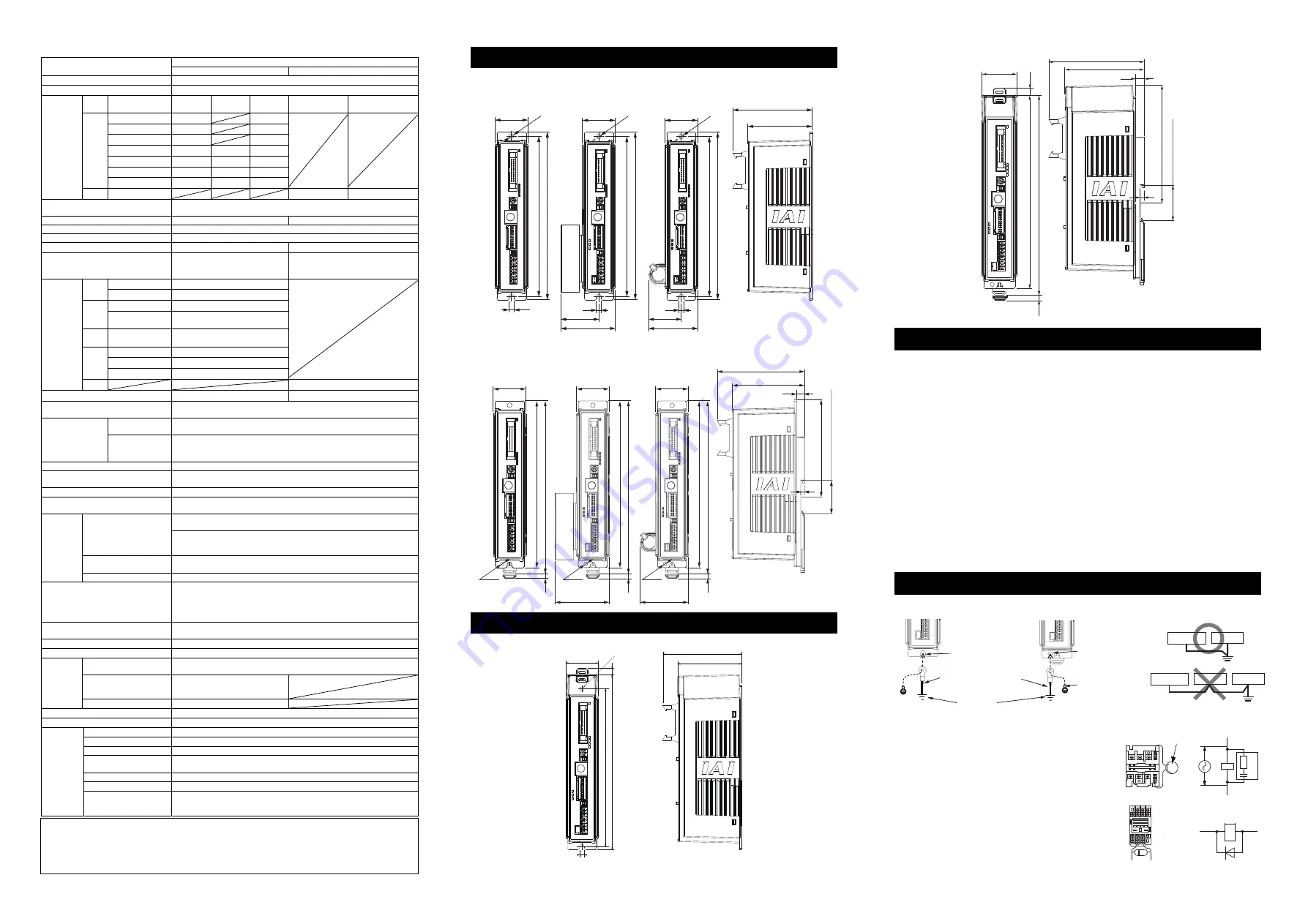
ACON, DCON List of Specifications
Item
Description
ACON-CA/CB/CGB DCON-CA/CB/CGB
Number of controlled axes
1-axis
Power-supply Voltage
24V DC
10%
Load
Capacity
(It does not
including
control side
current
consumption)
(Note1)
Series Motor
Type
Rated
Max. Power
Consumption MAX.
(Note5)
Rated
MAX.
RCA,
RCA2,
RCL
2W 0.8A
4.6A
5W 1.0A
6.4A
10W (RCL) 1.3A
6.4A
10W (RCA/ RCA2) 1.3A
2.5A
4.4A
20W 1.3A
2.5A
4.4A
20W (Model: 20S) 1.7A
3.4A
5.1A
30W 1.3A
2.2A
4.0A
RCD 3W
0.7A
1.5A
Power Supply for Electromagnetic Brake
(for actuator equipped with brake)
24V DC
10% 0.15A (MAX.)
Heat Generation
8.4W
4W
Rush Current
(Note2)
10A
Transient Power Cutoff Durability
MAX. 500
s
Motor Control System Sinusoidal
Waveform
(AC) Drive
Rectangular Waveform (DC) Drive
Corresponding Encoder
Incremental Encoder
Serial Absolute Encoder
Battery-less Aboslute Encoder
Incremental Encoder
Corresponding
Encoder
Resolution
RCA Incremental
Type 800pulse/rev
Serial Absolute Type 16384pulse/rev
RCA2 RCA2_***
N
1048pulse/rev
Other than
RCA2_*** N
800pulse/rev
RCA
/RCA2
Battery-less
Absolute Type
16384pulse/rev
RCL
RA1, RA4, SA1, SA4 715pulse/rev
RA2, RA5, SA2, SA5 855pulse/rev
RA3, RA6, SA3, SA6 1145pulse/rev
RCD
400pulse/rev
Actuator Cable Length
MAX. 20m
MAX. 10m
Serial Communication Interface
(SIO Port)
RS485 : 1 CH (based on Modbus Protocol RTU/ASCII) Speed : 9.6 to 230.4Kbps
Control available with serial communication in the modes other than the pulse train
External Interface
PIO Type
Signal I/O dedicated for 24V DC (selected from NPN/PNP) … Input 16 points max.,
output 16 points max. Cable length MAX. 10m
Fieldbus Type
DeviceNet, CC-Link, PROFIBUS-DP, CompoNet, MECHATROLINK-
Ⅰ
/
Ⅱ
,
EtherCAT, EtherNet/IP, PROFINET-IO, MECHATROLINK-
Ⅲ
(Except for ACON-CA
and DCON-CA)
Data Setting and Input
PC Software, Touch Panel Teaching, Teaching Pendant, Data Setter
Data Retention Memory
Saves position data and parameters to non-volatile memory
(There is no limitation to the number of times data may be written.)
Operation Mode
Positioner Mode/Pulse Train Control Mode (selected by parameter setting)
Number of Positions in Positioner Mode
Standard 64 points, MAX. 512 points (PIO Type)
(Note) Number of positions differs depending on the selection in PIO pattern.
Pulse Train
Interface
(Note4)
Input Pulse Frequency
Differential System (Line Driver System) : MAX. 200kpps
Cable length MAX. 10m
Open Collector System : Not applicable.
* If the host applies the open collector output, prepare AK-04 (option) separately to
convert to the differential type.
Command Pulse Multiplying
Factor (Electrical Gear : A/B)
1/50
A/B
50/1
Setting Range of A and B (set to parameter) : 1 to 4096
Feedback Pulse Output
None
LED Display
(mounted on Front Panel)
SV (GN)/ALM (RD) : Servo ON/Alarm generated
STS0 to 3
: Status display
RDY (GN)/ALM (RD) : Absolute function in normal / absolute function error (for the simple
absolute type)
1, 0 (GN) (RD)
: Absolute function status display (for the simple absolute type)
Electromagnetic Brake Compulsory
Release Switch (mounted on Front Panel)
Switching NOM (standard)/BK RLS (compulsory release)
Insulation Resistance
500V DC 10M
or more
Protection Function against Electric Shock Class I basic insulation
Weight
(Note3)
(Other than
Field
Network
Type)
Incremental Type
Screw fixed type : 230g or less
DIN rail fixed type : 265g or less
Simple Absolute Type
Battery (AB-7) : 190g or less
Absolute Battery Case (SEP-ABU):
140g or less
Serial Absolute Type Battery (AB-5) : 20g
Cooling Method
Natural air-cooling
External dimensions
Screw fixed type : 35W×178.5H×69.6D DIN rail fixed type : 35W×185H×78.1D
Environment Surrounding Air Temperature 0 to 40
C
Surrounding Humidity
5%RH to 85%RH or less (There should be no condensation or freeze)
Surrounding Environment
[Refer to Installation Environment]
Surrounding Storage
Temperature
-20 to 70
C (Excluding battery)
Usage Altitude
1000m or less
Protection Class
IP20
Vibration Durability
Frequency 10 to 57Hz / Swing width : 0.075mm
Frequency 57 to 150Hz / Acceleration 9.8m/s
2
XYZ directions Sweep time : 10 minutes Number of sweep : 10 times
Note1 Control power capacity is 0.3A.
Note2 In-rush current will flow for approximately 5ms after the power is turned on (at 40
C).
Note that the value of in-rush current differs depending on the impedance of the power supply line.
Note3 Add the weight of the battery (case) for “Simple Absolute Type” and “Serial Absolute Type”.
Note4 Serial absolute type is not applicable for the pulse train control mode.
Note5 The current reaches the maximum at the excitation phase detection of the motor conducted when the servo is turned on
for the first time after the power is supplied. (TYP 1 to 2 second, MAX. 10 second)
External Dimensions (ACON, DCON and PCON-CA/CB/CGB/CBP/CGBP)
●
Screw
fixed
type
Battery-less Absolute/
Simplified Absolute Type
Serial Absolute Type
Side View
Incremental Type
(Option)
(Option)
84.8
69.6
35
φ
5
170.5
178.5
5
35
φ
5
5
(40.5)
(58)
170.5
178.5
35
φ
5
5
(34.5)
(52)
170.5
178.5
●
DIN rail fixed type
Battery-less Absolute/
Simplified Absolute Type
Serial Absolute Type
Side View
Incremental Type
(Option)
(Option)
35
178.5
185
(5)
M3
(for FG cable
attachment)
93.6
78.1
8.5
4
104 from DIN rail center
35.4 (Width of 35mm DIN rail)
M3
35
178.5
185
(5)
(52)
(for FG cable
attachment)
M3
35
178.5
185
(5)
(58)
(for FG cable
attachment)
External Dimensions (PCON-CFA/CFB/CGFB)
●
Screw
fixed
type
35
φ
5
5
84.8
69.6
190
170.5
(7)
(Note) When using the
attachment hole
on the top of the
controller, detach
the fan unit
temporarily.
●
DIN rail fixed type
(7)
35
93.3
78.1
8.5
4
115 from DIN rail center
35.4 (Width of 35mm DIN rail)
190
(5)
196.5
Installation Environment
This product is capable for use in the environment of pollution degree 2
*1
or equivalent.
*1 Pollution Degree 2: Environment that may cause non-conductive pollution or transient conductive
pollution by frost (IEC60664-1)
1. Installation Environment
Do not use this product in the following environment
Location where the surrounding air temperature exceeds the range of 0 to 40
C
Location where condensation occurs due to abrupt temperature changes
Location where relative humidity exceeds 5%RH to 85%RH
Location exposed to corrosive gases or combustible gases
Location exposed to significant amount of dust, salt or iron powder
Location subject to direct vibration or impact
Location exposed to direct sunlight
Location where the product may come in contact with water, oil or chemical droplets
Environment that blocks the air vent [Refer to Installation and Noise Elimination]
A place with its altitude more than 1000m
When using the product in any of the locations specified below, provide a sufficient shield.
Location subject to electrostatic noise
Location where high electrical or magnetic field is present
Location with the mains or power lines passing nearby
2. Storage and Preservation Environment
Storage and preservation environment follows the installation environment. Especially in a long-term storage, consider
to avoid condensation of surrounding air.
Unless specially specified, moisture absorbency protection is not included in the package when the machine is
delivered. In the case that the machine is to be preserved in an environment where dew condensation is anticipated,
take the condensation preventive measures from outside of the entire package, or directly after opening the package.
Installation and Noise Elimination
1. Noise Elimination Grounding (Frame Ground)
2. Precautions regarding wiring method
1) Wire is to be twisted for the 24V DC power supply.
2) Separate the signal and encoder lines from the power
supply and power lines.
3. Noise Sources and Elimination
Carry out noise elimination measures for power devices on
the same power path and in the same equipment.
The following are examples of measures to eliminate noise
sources.
1) AC solenoid valves, magnet switches and relays
[Measure] Install a Surge absorber parallel with the coil.
2) DC solenoid valves, magnet switches and relays
[Measure] Install a diode parallel with the coil. Use a DC
relay with a built-in diode.
Surge absorber
Relay
coil
Relay coil
R
C
+24V
0V
+24V
0V
+
-
Do not share the ground wire with or connect
to other equipment. Ground each controller.
Controller
Other
equipment
Controller
Other
equipment
Other
equipment
Connect the ground cable
using the tapped hole for
FG connection on the main unit.
M3 × 5 nickeled pan head
machine screw
(enclosure dedicated for
DIN rail fixed type)
Screw fixed type
DIN rail fixed type
Connect the ground line
together to the main unit
using the fixing screw.
Copper wire:
Connect a ground wire with a
diameter of 1.6mm (2mm
2
) or larger.
Earth Terminal
Grounding resistance 100Ω or less
(Class D grounding)