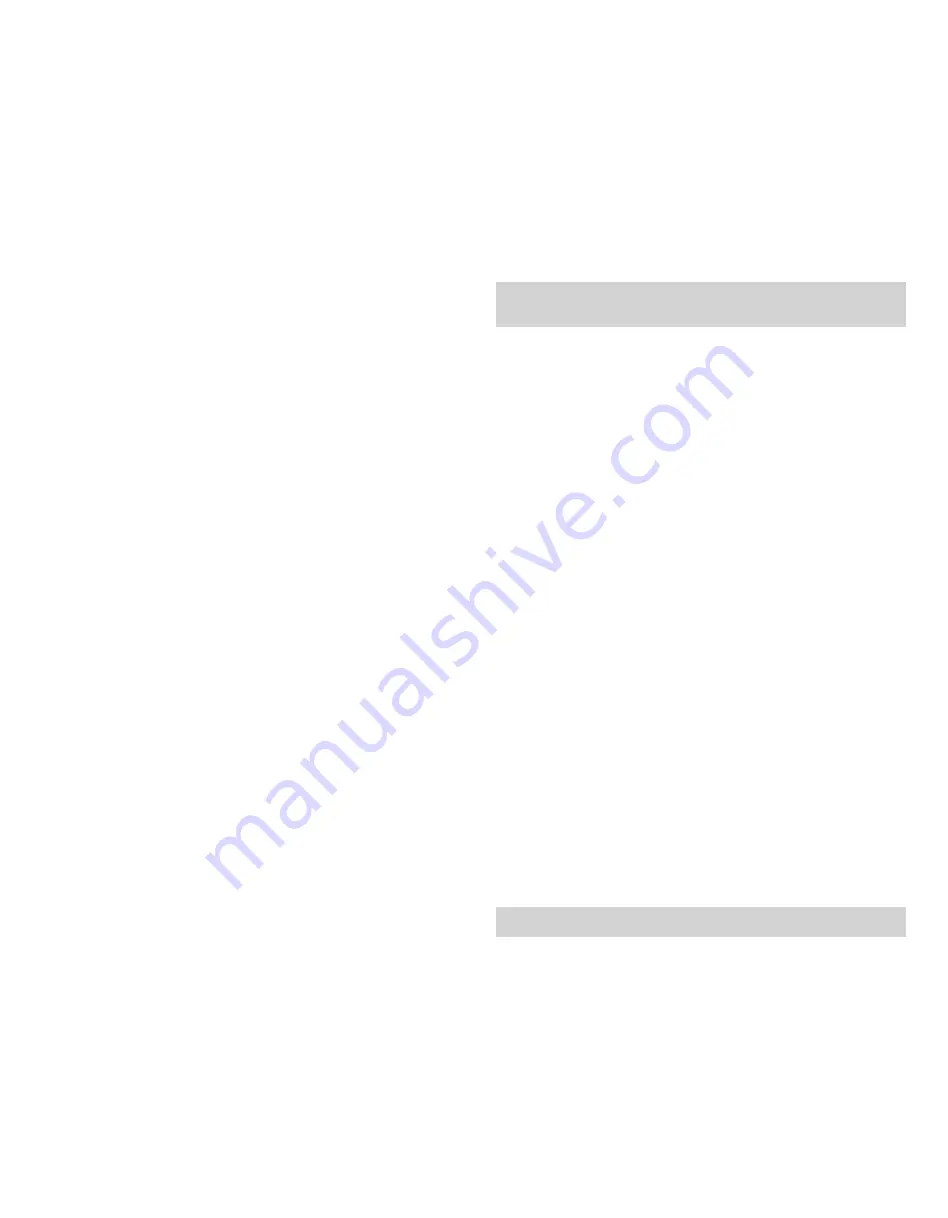
3
SAFETY INFORMATION
• Installation
GUARDS AND GUARDING
Interfacing of Equipment
. When two or more pieces of equipment
are interfaced, special attention shall be given to the interfaced area
to ensure the presence of adequate guarding and safety devices .
Guarding Exceptions
. Whenever conditions prevail that would
require guarding under these standards, but such guarding would
render the conveyor unusable, prominent warning means shall be
provided in the area or on the equipment in lieu of guarding .
Guarded by Location or Position
. Where necessary for the
protection of employees from hazards, all exposed moving
machinery parts that present a hazard to employees at their work
station shall be mechanically or electrically guarded, or guarded by
location or position .
•
Remoteness from frequent presence of public or employed
personnel shall constitute guarding by location .
•
When a conveyor passes over a walkway, roadway, or work
station, it is considered guarded solely by location or position
if all moving parts are at least 8 ft. (2.44 m) above the floor or
walking surface or are otherwise located so that the employee
cannot inadvertently come in contact with hazardous moving
parts .
•
Although overhead conveyors may be guarded by location,
spill guards, pan guards, or equivalent shall be provided if
the product may fall off the conveyor for any reason and if
personnel would be endangered .
HEADROOM
•
When conveyors are installed above exit passageways, aisles,
or corridors, there shall be provided a minimum clearance of
6 ft. 8 in. (2.032 m) measured vertically from the floor or or
walking surface to the lowest part of the conveyor or guards .
•
Where system function will be impaired by providing the
minimum clearance of 6 ft . 8 in . (2 .032 m) through an
emergency clearance, alternate passageways shall be
provided .
•
It is permissible to allow passage under conveyors with less
that 6 ft. 8 in. (2.032 m) clearance from the floor for other than
emergency exits if a suitable warning indicates low headroom .
• Operation
A) Only trained employees shall be permitted to operate conveyors .
Training shall include instruction in operation under normal
conditions and emergency situations .
B) Where employee safety is dependent upon stopping and/or
starting devices, they shall be kept free of obstructions to permit
ready access .
C) The area around loading and unloading points shall be kept clear
of obstructions which could endanger personnel .
D) No person shall ride the load-carrying element of a conveyor
under any circumstances unless that person is specifically
authorized by the owner or employer to do so . Under those
circumstances, such employee shall only ride a conveyor which
incorporates within its supporting structure platforms or control
stations specifically designed for carrying personnel. Under no
circumstances shall any person ride on any element of a vertical
conveyor .
E) Personnel working on or near a conveyor shall be instructed as
to the location and operation of pertinent stopping devices .
F) A conveyor shall be used to transport only material it is capable
of handling safely .
G) Under no circumstances shall the safety characteristics of the
conveyor be altered if such alterations would endanger personnel .
H) Routine inspections and preventive and corrective maintenance
programs shall be conducted to ensure that all safety features and
devices are retained and function properly .
I) Personnel should be alerted to the potential hazard of
entanglement in conveyors caused by items such as long hair, loose
clothing, and jewelry .
J) Conveyors shall not be maintained or serviced while in operation
unless proper maintenance or service requires the conveyor to be in
motion . In this case, personnel shall be made aware of the hazards
and how the task may be safely accomplished .
K) Owners of conveyor should ensure proper safety labels are
affixed to the conveyor warning of particular hazards involved in
operation of their conveyors .
• Maintenance
Refer to ANSI Z244 .1-1982, American National Standard for Personnel
Protection – Lockout/Tagout of Energy Sources – Minimum Safety
Requirements and OSHA Standard Number 29 CFR 1910 .147 “The
Control of Hazardous Energy (Lockout/Tagout) .”
•
All maintenance, including lubrication and adjustments, shall be
performed only by qualified and trained personnel.
•
It is important that a maintenance program be established
to ensure that all conveyor components are maintained in a
condition which does not constitute a hazard to personnel .
•
When a conveyor is stopped for maintenance purposes, starting
devices or powered accessories shall be locked or tagged out
in accordance with a formalized procedure designed to protect
all persons or groups involved with the conveyor against an
unexpected start .
•
Replace all safety devices and guards before starting
equipment for normal operation .
•
Whenever practical, DO NOT lubricate conveyors while they are
in motion . Only trained personnel who are aware of the hazard
of the conveyor in motion shall be allowed to lubricate .
Safety Guards
Maintain all guards and safety devices IN POSITION and IN SAFE
REPAIR .
Safety Labels
In an effort to reduce the possibility of injury to personnel working
around HYTROL conveying equipment, safety labels are placed at
various points on the equipment to alert them of potential hazards .
Please check equipment and note all safety labels . Make certain
your personnel are alerted to and obey these warnings . See Safety
Manual for examples of warning labels .
CAUTION!
Because of the many moving parts on the conveyor, all
personnel in the area of the conveyor need to be warned that the conveyor
is about to be started .
REMEMBER
Do not remove, reuse or modify material handling equipment
for any purpose other than it’s original intended use .