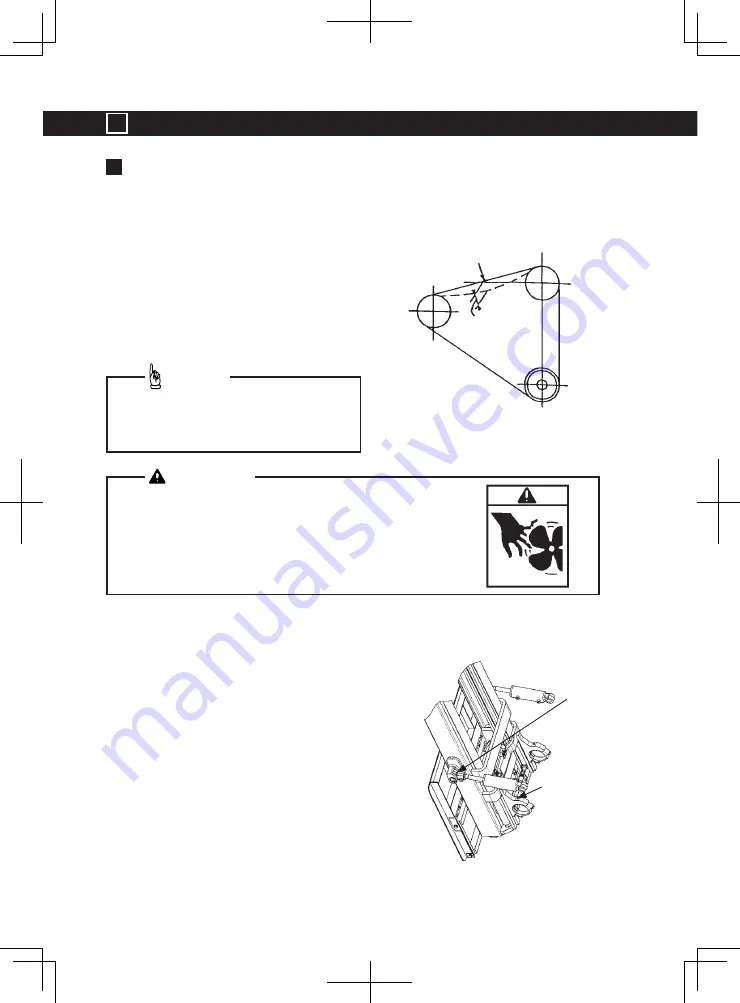
Inspection
6
─
90
─
Weekly Inspection (Every 50 Hours)
Besides the daily inspection, carry out the following inspections once a week (every
50 hours).
1. Inspection of fan belt
1. Press down on the fan belt between
the alternator and fan pulley with a
force of 98 N (10kgf).
a. Is the belt tension adequate? 11 to
13mm (when pressed with 98 N)
b. Is there any damage?
2. Lubrication and greasing of lift truck parts
1. Clean the grease nipples with a clean cloth and apply grease to the following
points with a grease gun.
Grease Used: Albania EP2
Mast trunnion and Tilt rod end
(At one location each on right and left)
Inspecting the fan belt tension while the engine is
running is dangerous. Always stop the engine before
inspecting the rotating sections and peripheral areas.
WARNING
The belt can be adjusted by moving
the installation position of the
alternator.
ADVICE
98 N
(10kgf)
Alternator
Fan
11 to 13mm
Crankshaft
Lubricate
Lubricate