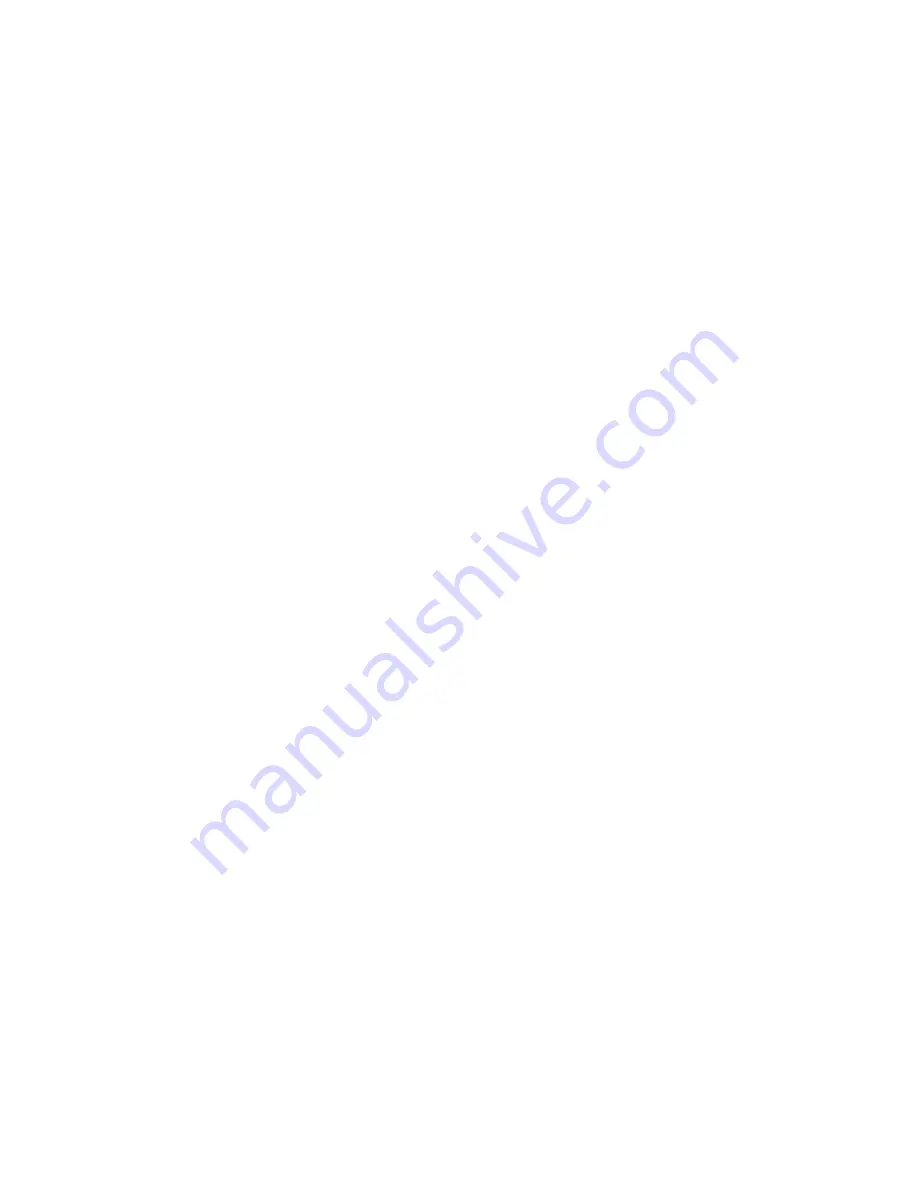
•
The operational check will also direct the tech-
nician to the proper cause in the procedure,
based on truck/system configuration, other
symptoms, and advise the user if any special
conditions are required (i.e. Operate the truck
until it has reached normal temperature, re-
charge the battery before proceeding etc.).
•
The operational check is also performed to ver-
ify that the problem has been corrected and
that the components and devices have been
restored to an operating condition.
The next item that appears in the procedure is the
CAUSE A
. This introduces the troubleshooter to the
first sequence of tests or measurements to follow.
Continuing through the procedure in the step-by-step
directions will lead the user to:
•
Additional possible causes
•
Replacement/repair instructions
•
Correction of the fault
•
Operational check of the repaired/replaced de-
vice
It must be noted that Service Manual factory direc-
tions discourage probing of the connectors using any
type of wire or pin and that resistance or continuity
measurements of these connections should only be
done with the appropriate service tool and breakout
connectors.
Following through the procedure, the next items are
the
DIAGRAMS
that support the troubleshooting and
provide relevant data for wiring, connectors, power,
signal and other reference data. These will enable the
troubleshooter to measure, verify, and make critical
decisions leading to the root cause. The diagrams
may include:
•
A mini-schematic of the suspect circuit
•
Wire identification and circuit function
•
Connector pin-out locators
•
Special reference data for device or compo-
nent
Troubleshooting Procedures, Performance
It is important to remember the basics of troubleshoot-
ing when checking the electronically reported faults.
Prior to starting any of the listed procedures, it is rec-
ommended that the items listed below be reviewed.
These may help to isolate the problem, eliminate
some steps or enforce the procedure that has been
identified. These items are:
•
LOOK
— Are there any observable symptoms,
visual evidence or obvious conditions that
could result in, or contribute to, the reported
fault.
Are the displayed Icons due to Interlocks? See
User Interface Supervisor
2200SRM1335 or
User Interface Service Technician
2200SRM1336 .
•
LISTEN
— If the lift truck can be operated with
the reported problem, are there any unusual
noises or vibrations that could result in, or con-
tribute to, the reported fault.
•
TOUCH OR SMELL
— High operating temper-
atures and excessive wear can sometimes pro-
duce an odor or visual evidence that can be
linked to other faults or conditions.
•
In general, let your senses and your experi-
ence assist you in resolving the problem in the
most efficient manner. Ask yourself:
•
What is required for this device or oper-
ation to function correctly?
•
Where are the devices/parts located?
•
Has this problem been reported before?
If so, how frequently? Use the fault his-
tory logs to help identify repeated prob-
lems. This can be very helpful in analyz-
ing faults of an intermittent nature which
may be difficult to duplicate.
•
Has repair work, disassembly or other
maintenance work been performed on
suspect device or system recently?
•
Once these questions have been considered,
proceed with the DTC resolution as per the
procedure, using any additional information to
assist in resolving the discrepancy.
Troubleshooting Procedures, Final
DTCs are stored in the FAULT CODE LOGS, where a
history of repeat failures is maintained, until cleared
by an authorized service technician. All DTCs are to
be cleared prior to operating the lift truck. Fault code
logs should only be cleared once the data is recorded
by a authorized service technician. See Display Menu
Flowchart.
Electrical System
General Maintenance and Diagnostic Data
Check the Service Manual section in Hypass Online for possible updates and check pertinent Grams
Confidential/Proprietary - Do Not Copy or Duplicate
9030-03-5
Summary of Contents for A099
Page 1: ...Hyster A276 J45XN J50XN J60XN J70XN Forklift...
Page 14: ...9010 2...
Page 28: ...NOTES 9010 05 14...
Page 30: ...9025 2...