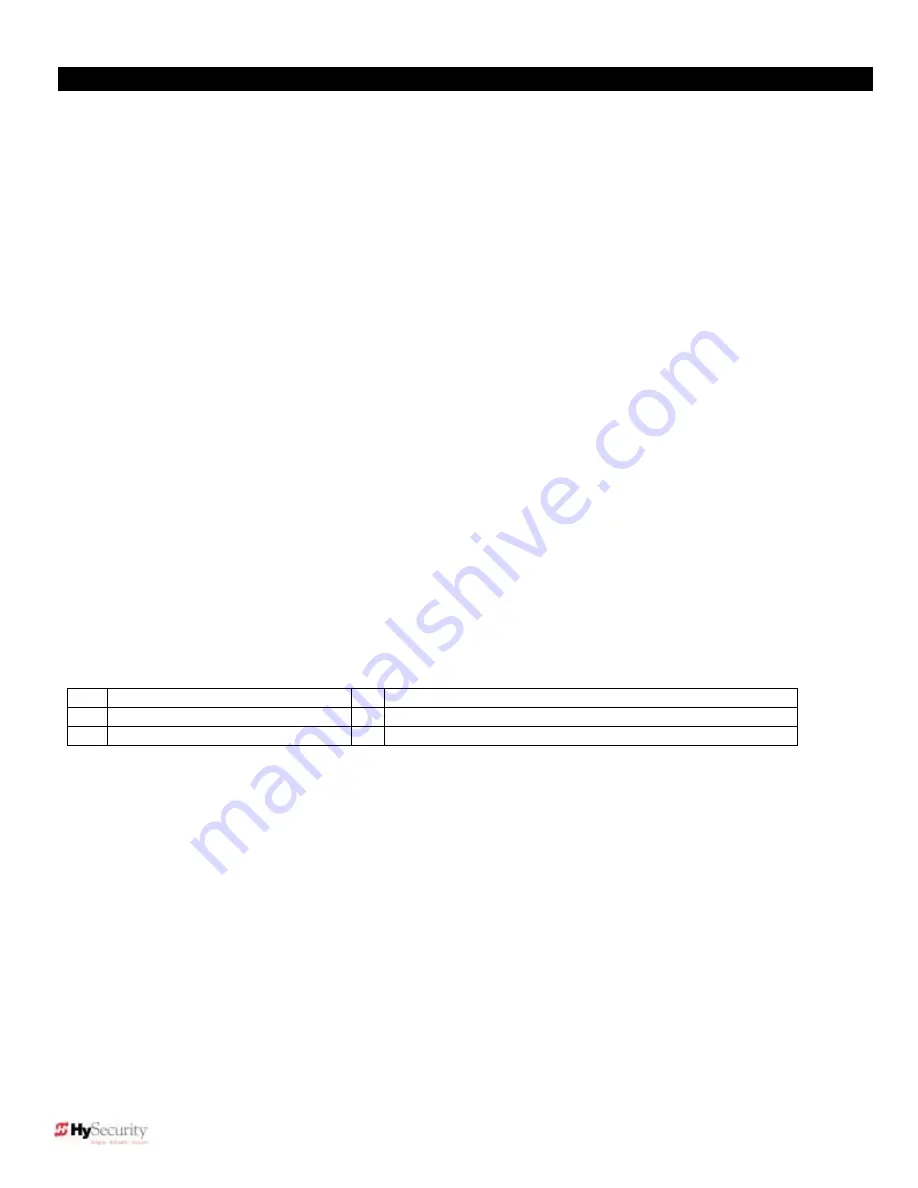
42
© 2012 Installation and Reference Manual D0125 Rev. H
Section 5
—HySecurity HY-5A Vehicle Detector Installation
1. Insert the locking end of each of two white plastic standoffs into the mounting holes on the detector.
2. Plug the detector into the appropriate socket along the right edge of the Smart Touch Controller board for the
detector function that is desired. Be careful to align the six detector pins into the socket correctly, and then snap
the standoffs into the holes on the right side of our control enclosure.
3. Route the loop wires through the wire guide provided and connect the loop leads to the two terminals directly on
the detector. Tighten the terminal screws securely.
4. When the power is turned on, the detectors will immediately tune themselves.
5. Once enabled, if the detector module is unplugged, a communications alert [AL10] will be triggered, then if the
fault continues, [ERR3] “detector failed” is displayed. The operator will also run as if the detector is triggered.
The [ERR3] can only be cleared by pressing the Reset button, which electronically uninstalls the detector. See
Detector & Loop Fault Diagnostics on page 44.
6. The Smart Touch Controller automatically governs frequency selection of all HY-5A detector modules. This
simplifies installation and guarantees that there is no cross talk between multiple loops. The frequency can also
be manually selected if needed, see the installer menu options.
7. Sensitivity is the only adjustment on the detector itself. Generally, sensitivity does not need to be increased unless
the loop is large loop or there are multiple loops connected to one detector. Do not exceed more than 200 sq/ft of
loop area to one detector.
The rotary switch for sensitivity has eight settings, which are as follows:
0 = Low, 1 = Normal, 2 = Medium, 3 = High (0 - 3 add the boost feature*)
4 = Low, 5 = Normal, 6 = Medium, 7 = High
*Boost increases the sensitivity during a call and is useful for maintaining continuous detection when the signal
may become weak, such as semi-trucks.
8. Vehicle detector functions are configurable in the Installer Menu as shown below.
I21
[or 1] OOLD detector function
1
0 = pause only, 1 = enable reversing to open
I22
[ir 1] IOLD detector function
1
0 = pause only, 1 = enable reversing to open
I23
[dL 1] Vehicle detector logic
1
1 – 4, 1 = std, 2&3 = quick close, 4 = full anti-tailgate*
The outside and inside Obstruction Loop Detectors “OOLD” or “IOLD” are factory configured to fully re-open the gate as a
default setting. In the Installer menu, each detector can individually be set so that when the gate is closing there is only a
pause if triggered. To change the IOLD setting, go to the menu item [ir__] and set to 0. For the OOLD, go to the menu
item [or__] and set to 0.
* See page 45 for optional Vehicle Detector logic modes and anti-tailgate option.
Summary of Contents for SlideDriver 50VF2
Page 2: ......
Page 28: ...14 2012 Installation and Reference Manual D0125 Rev H Section 2 Technical Drawings...
Page 29: ...15 2012 Installation and Reference Manual D0125 Rev H Section 2 Technical Drawings...
Page 36: ...22 2012 Installation and Reference Manual D0125 Rev H Section 3 Wiring Control Inputs...
Page 63: ...49 2012 Installation and Reference Manual D0125 Rev H Section 6 Internal Solenoid Lock Drawing...
Page 64: ...50 2012 Installation and Reference Manual D0125 Rev H Section 6 Internal Solenoid Lock Drawing...
Page 81: ...68 2012 Installation and Reference Manual D0125 Rev H...