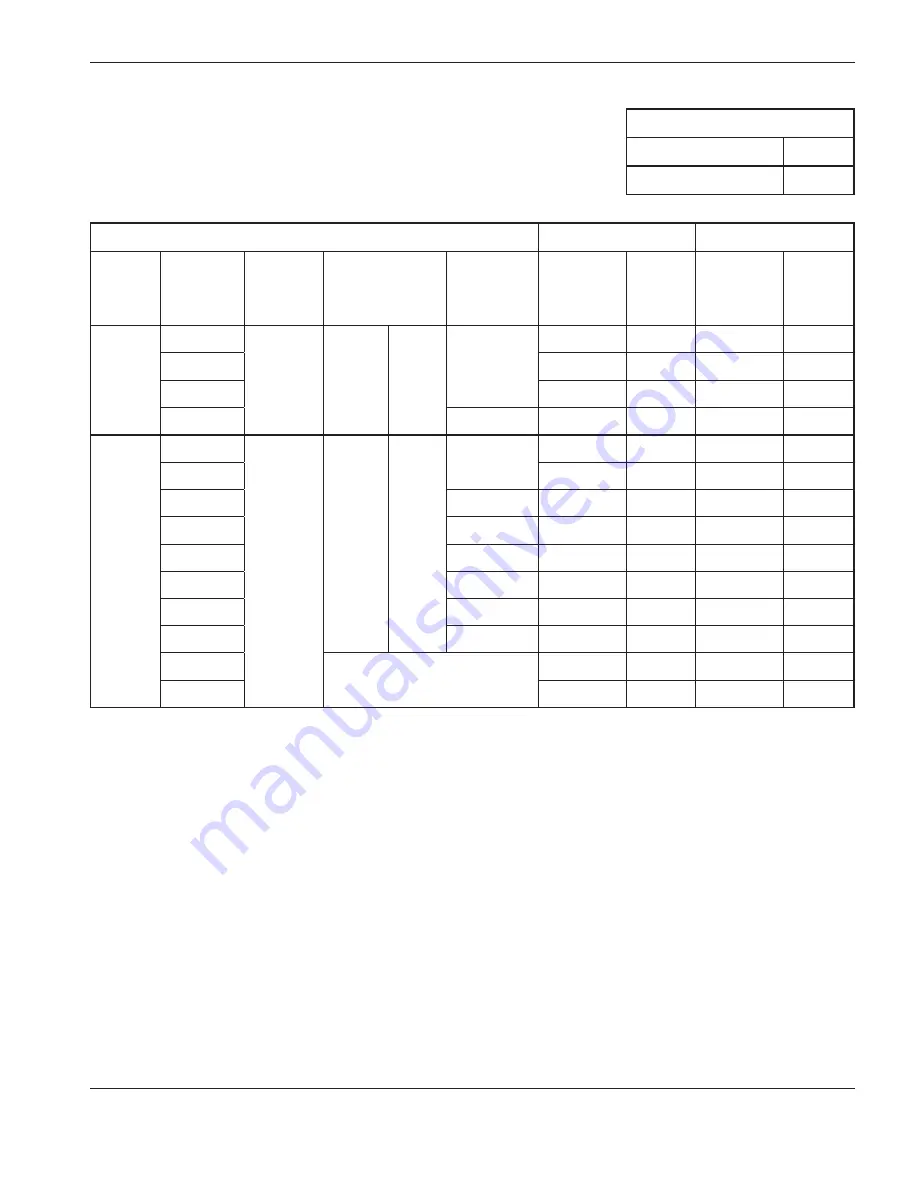
torch setup
powermax
45
Operator Manual
3-11
T45m shielded consumables
Air flowrate (
lpm
)
Stainless steel
Hot
151
Metric
Cold
165.2
Recommended
Maximum
Arc
current
(amps)
Material
thickness
(mm)
Torch-
to-work
distance
(mm)
Initial pierce
height
Pierce time
delay
(sec)
Cut Speed
(mm/min)
Voltage
(V)
Cut Speed
(mm/min)
Voltage
(V)
30
0.5
1.5
3.8 mm
250%
0.0
9150
119
10160*
123
0.8
8650
117
10160*
121
0.9
8100
115
10160*
119
1.5
0.2
3750
113
4700
118
45
0.9
1.5
3.8 mm
250%
0.0
7600
112
10160*
109
1.5
8100
112
10160*
125
1.9
0.1
7100
118
9144
115
2.7
0.3
4050
118
5080
116
3.4
0.4
3050
121
3810
118
4.8
0.5
1780
122
2159
118
6.4
0.6
1100
124
1397
120
9.5
0.8
760
126
813
121
12.7
Edge start recommended
350
132
457
128
19.1
175
136
229
131
*Maximum cut speed is limited by the test able’s maximum speed (10160 mm/min).
Summary of Contents for POWERMAX 45
Page 1: ...45 Plasma arc cutting system Operator Manual 805780 Revision 2 ...
Page 6: ......
Page 10: ...Table of Contents iv powermax45 Operator Manual ...
Page 30: ...Power supply setup 2 8 powermax45 Operator Manual ...
Page 74: ...operation 4 16 powermax45 Operator Manual ...
Page 84: ...Maintenance and Repair 5 10 powermax45 Operator Manual ...