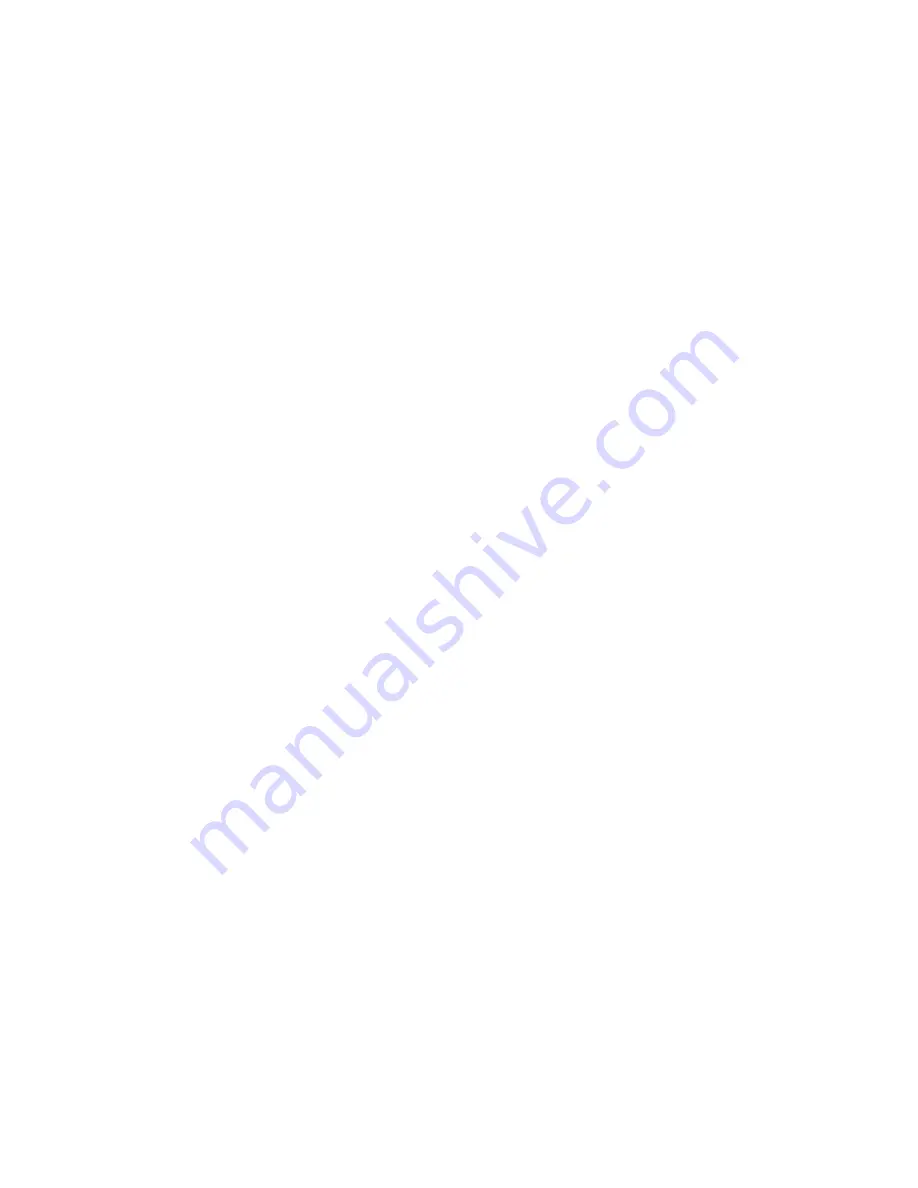
Password Setups
340
Integral Gain
Integral Gain improves the positioning accuracy of the control loop. Integral Gain can be used to
compensate for static friction or gravity. Excessive Integral Gain can result in system instability.
For most shape cutting machines, this parameter should be set to zero (0).
Derivative Gain
Derivative Gain helps to dampen out sudden changes in velocity. The higher the Derivative Gain, the
slower the response time to the control loop.
For most velocity loop drives, this parameter will be set to zero (0).
Feedforward Gain
Feedforward Gain can be used to drive the following error to zero during machine motion. In all
digital control loops there is a finite amount of error that is introduced by the velocity command.
Increasing Feedforward Gain can reduce this introduced error.
Velocity Gain
When using a current loop amplifier, the internal velocity loop in the control can be used to provide
dampening without an external tachometer.
Using the internal velocity loop with a current loop amplifier can result in higher static stiffness,
smoother machine motion, and less overshoot.
Servo Error Tolerance
Allows the user to program the amount of servo loop Following Error to be allowed prior to display an
error message. The parameter is limited to a maximum value of 90 degrees.
Encoder Counts per rev
Enter a value that is the number of encoder edges per revolution of the Contour Bevel Head axis. It
is possible to enter fractional encoder units and the control will keep track of these fractions
automatically. Encoder Counts per rev are equal to the resolution of the encoder multiplied by the
encoder revolutions per rev.
For example: The Resolution of a 4X
– 1000 line encoder counts both edges (lines) of channel A and
channel B to equal 4 counts per line time multiplied by the 1000 lines per revolution would equal 4000
counts per revolution.
Encoder Counts/Rev = 4 Counts/Line x 1000 Lines/Rev = 4000
Drive Type
This parameter is used to tell the control what type of control loop to run. If you are running an
external velocity loop drive (indicated by having an integrated tachometer in the motor), select
Velocity. If you are running in torque mode (no tachometer), select Current.
Summary of Contents for Edge TI
Page 24: ...Table of Contents XXII...
Page 41: ...Overview 17 Alpha Numeric Keypad Numeric Keypad...
Page 54: ...Overview 30...
Page 83: ...Setups 59 Water Jet Press the Timing Diagram soft key to view the timing diagram from setups...
Page 88: ...Setups 64...
Page 116: ...Shape Manager 92...
Page 128: ...Files 104...
Page 280: ...Part Options 256...
Page 317: ...Diagnostics 293 DriveTop from Indramat...
Page 402: ...Phoenix Link 378...
Page 420: ...Sensor THC 396...
Page 428: ...Command THC 404...
Page 436: ...Motion Overview 412 Motion Tuning Watch Windows Position and Following Error may be displayed...
Page 470: ...Program Codes 446...
Page 478: ...Automated Plasma Interface 454 Inputs...
Page 479: ...Automated Plasma Interface 455 Inputs...
Page 480: ...Automated Plasma Interface 456 Outputs...
Page 496: ...Automated Plasma Interface 472...
Page 520: ...MicroEdge 496...
Page 532: ...Edge Ti 508 Optional Motor Information...
Page 540: ...Edge Ti 516...
Page 546: ...Voyager III 522 Examples of possible circuits Output Input 24 VDC Com...
Page 557: ...Networking 533 7 Double Click on the network interface connected to your LAN...
Page 558: ...Networking 534...
Page 561: ...Networking 537...
Page 562: ...Networking 538 13 Double click on the System 14 Select the Computer Name tab...
Page 572: ...Networking 548...
Page 573: ......