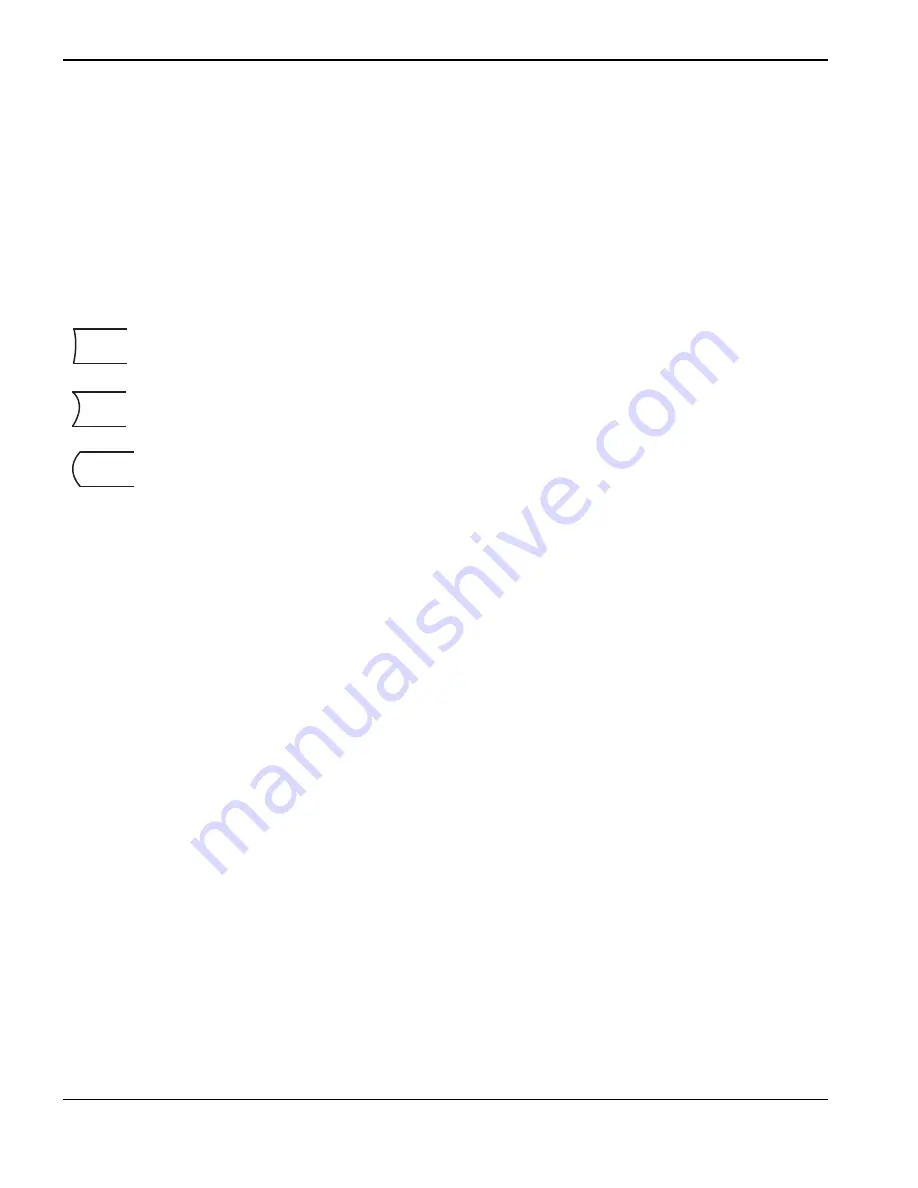
50
Duramax/Duramax Hyamp Robotic Torches
Service Manual 807460
3 – Operation
Low-speed dross forms when the torch’s cutting speed is too slow and the arc angles ahead. It forms as a heavy, bubbly
deposit at the bottom of the cut and can be removed easily. Increase the speed to reduce this type of dross.
High-speed dross forms when the cutting speed is too fast and the arc angles behind. It forms as a thin, linear bead of
solid metal attached very close to the cut. It is more firmly attached to the bottom of the cut than at low speed and is
difficult to remove. To reduce high-speed dross:
Decrease the cutting speed.
Decrease the torch-to-work distance.
Straightness of the cut surface
Piercing a workpiece using the robotic torch
As with the hand torch and machine torch, you can start a cut with the robotic torch at the edge of the workpiece or by
piercing the workpiece. Piercing may result in a shorter consumable life than with edge starts.
The cut charts, provided in the system’s Operator Manual, include a column for the recommended torch height when
starting a pierce. For the Powermax65, Powermax85, and Powermax105, the pierce height is generally 2.5 times the
cutting height. For the Powermax125, the pierce height is generally between 1.5 and 4 times the cut height. Refer to the
cut charts for specific values.
The pierce delay must be long enough that the arc can pierce the material before the torch moves, but not so long that
the arc “wanders” while trying to find the edge of a large hole. As consumables wear, this delay time may need to be
increased. Pierce delay times given in the cut charts are based on average delay times throughout the life of the
consumables.
When piercing materials close to the maximum thickness for a specific process, consider the following important factors:
Allow a lead-in distance approximately equal to the thickness of the material being pierced. For example, 20 mm
(0.75 inch) material requires a 20 mm lead-in.
To avoid damage to the shield from the buildup of molten material created by the pierce, do not allow the torch to
descend to cut height until it has cleared the puddle of molten material.
Different material chemistries can have an adverse effect on the pierce capability of the system. In particular,
high-strength steel with a high manganese or silicon content can reduce the maximum pierce capability. Hypertherm
calculates mild steel parameters with certified A-36 plate.
Using a “flying pierce” (that is, starting torch motion immediately after transfer and during the pierce process) can
extend the piercing capability of the system in some cases. Because this can be a complex process that can damage
the torch or other components, a stationary or edge start is recommended.
A typical plasma cut surface is slightly concave.
The cut surface may become more concave, or convex. Correct torch height is required to keep the cut
surface acceptably close to straight. Worn consumables also affect the straightness of the cut.
A strongly concave cut surface occurs when the torch-to-work distance is too low. Increase the
torch-to-work distance to straighten the cut surface.
A convex cut surface occurs when the torch-to-work distance is too great or the cutting current is too
high. First, try lowering the torch, then reduce the cutting current.
Summary of Contents for Duramax
Page 1: ...Duramax and Duramax Hyamp Robotic Torches 45 90 180 Service Manual 807460 Revision 2 English ...
Page 6: ......
Page 10: ...10 Duramax Duramax Hyamp Robotic Torches Service Manual 807460 Contents ...
Page 20: ...20 Duramax Duramax Hyamp Robotic Torches Service Manual 807460 1 Specifications ...
Page 46: ...46 Duramax Duramax Hyamp Robotic Torches Service Manual 807460 2 Torch Setup ...