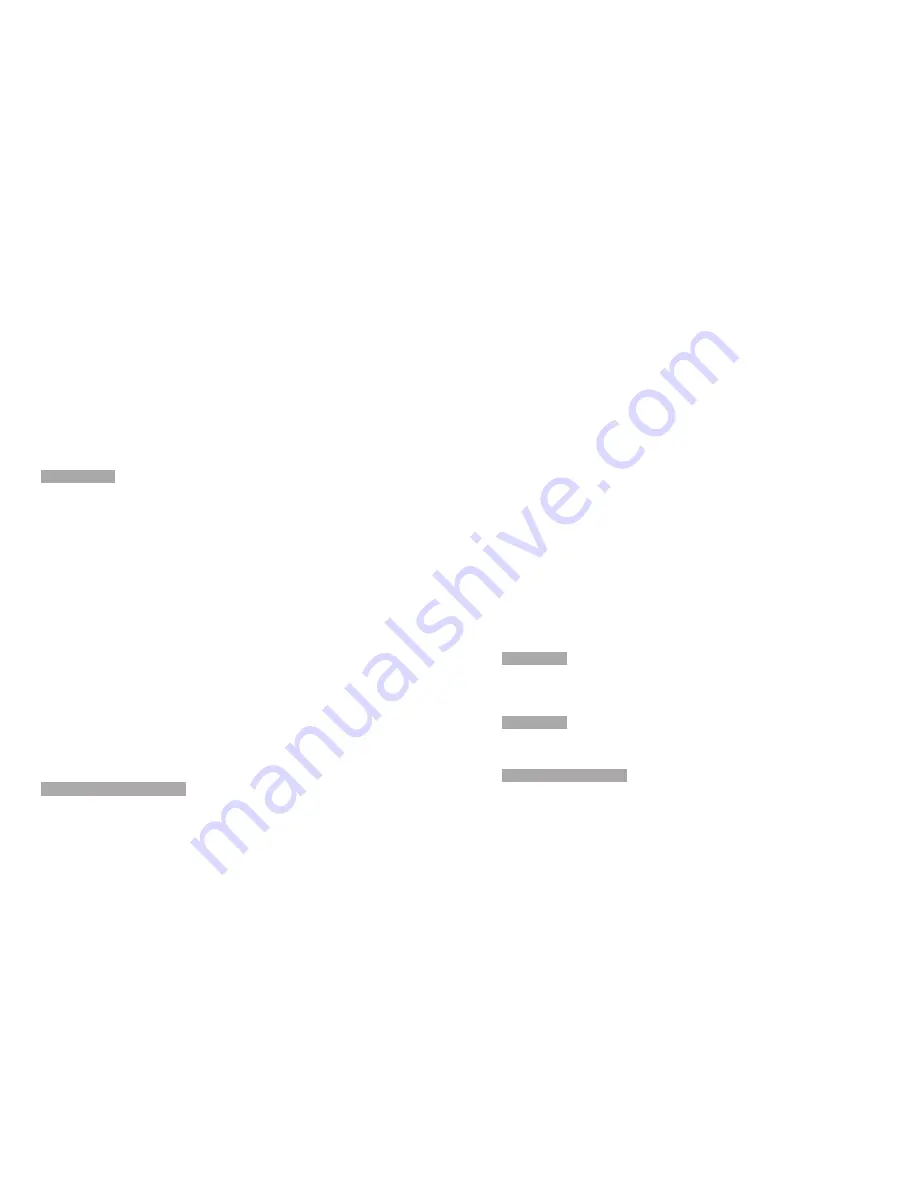
lubricant or sewing machine lubricant is acceptable for this purpose. Do not use
detergent oil.
2. Before connecting the hose for operation, apply 4 or 5 drops of #10 spindle oil at the
air inlet. Avoid the misuse of thicker oil which may lead to the reduced performance
or malfunction.
3. Oiling is necessary within 1 or 2 hours of continuous operation.
4. After operation, take off the air hose and pour 4 or 5 drops of #60 spindle oil into the
air inlet, then connect the hose again to run the tool for a few seconds, which can
prolong the tool life.
5. Clean air inlet filter cartridge on the air line weekly.
F.
Warnings
1. Never use the tool in potentially explosive atmospheres.
2. Keep your body in well balanced position and always wear gloves to reduce the risk
of crushing caused by torque between a reaction bar and work-piece.
3. Unexpected tool movement due to reaction forces or breakage of inserted tool or
reaction bar may cause injuries.
4. Prevent long hair or loose clothing from drawing in while operating the tool. You
may get the risk of being injured if the handkerchief, necktie etc. are not kept away
from the running tool.
5. The noise emission (sound pressure level) at the workplace may exceed the normal
standard ---usually 85dB(A). In this case, a quality ear protector should be used.
6. Unexpected direction of inserted tool movement could case a hazardous situation.
7. Slip / Trip / Fall is a major cause of serious injury or even death. Be aware of excess
hose left on your walking way or on the working surface and be aware of the
whipping air hose too.
8. Excessive high air pressure and too much free rotation may speed up the wear of the
tool and may cause dangerous situation.
9. Continuous operation and bad working condition will injure hands. Once hand
numbs or aches , operator shall stop the tool for a while for relaxing and re-start the
work after recovery. Operator shall immediately see a doctor if such a serious
symptom occurs.
10. Never change the inner construction and design, which may cause a danger in
operation.
G.
General Trouble Shooting
* Troubles:
-
Tool does not run at a normal speed or at a variable speed
-
The motor blocks
-
Automotive start when connected to compressed air
-
Torque reduces
-
Abnormal vibrating -Easy hot rising at the housing
* Causes:
-
Air supply is not enough (air pressure not in a required standard)
-
Speed controller/switch breaks down
-
Rotor blades break or wear out
-
Dust gets into the motor
-
Throttle lever or starting trigger malfunctions
-
Air leakage at the inlet or somewhere else
-
Bearing(s) damages
-
Correspondent O-ring(s) wears out or out of position
-
Lack of lubricating
* Troubles Shooting:
-
Check the air hose to see whether it is blocked or twisted for less air supply.
-
Check the air compressor to gain the correct air pressure required.
-
Replace rotor blades
-
Disassemble the tool and clean the inner structure under proper instructions
-
Check and fix the throttle lever or starting trigger for accurate operation
-
Check the air leakage and fix it under proper instruction
-
Replace new bearing(s)
-
Replace the damaged O-ring(s) or put it back in correct position
-
Oil / Lubricate the tool consistently until it gains the right speed and torque
* Note:
For any other special troubles which cannot be settled down by the operator, please
Contact the selling agent from whom you purchase the tool.
H.
Storage
Avoid to store the tool in a location subject to high humidity, which may result in rusty
mechanism inside the tool. Before storing, oil the tool at the air inlet with proper
spindle oil and run it for a few seconds.
I.
Disposal
When the tool is seriously damaged or out of life, leave it in a resource recycling can.
Never drop it into fire.
J.
Ordering Spare Parts
1. Contact the sale agent from whom you purchase the tool for spare parts ordering for
any necessary replacement for continuous use of tool and extending the tool life.
2. In ordering spare parts and components, give each spare part number and order
quantity.
Thank you.