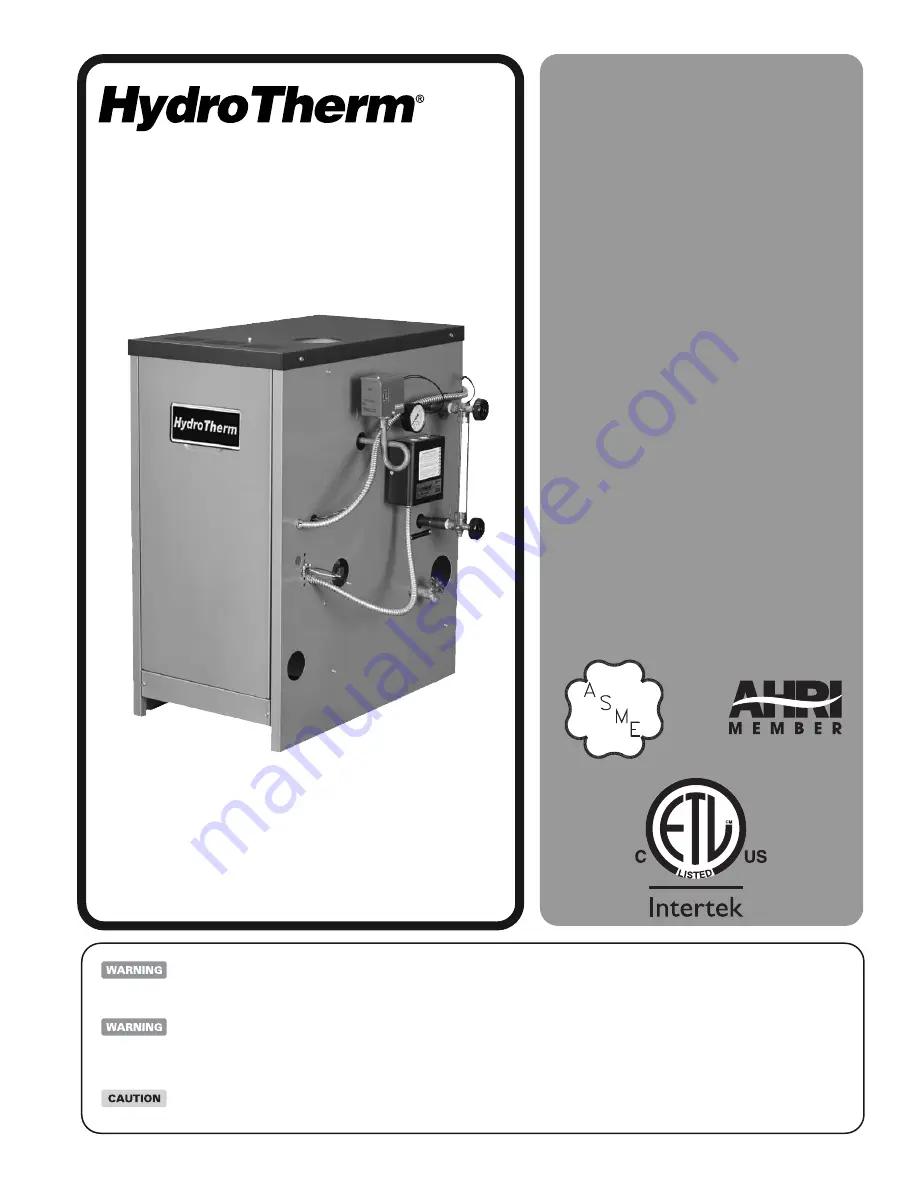
This manual is intended only for use by a qualified heating installer/technician. Read and follow this manual, all supplements and related
instructional information provided with the boiler. Install, start and service the boiler only in the sequence and methods given in these in-
structions. Failure to do so can result in severe personal injury, death or substantial property damage.
Do not use the boiler during construction.
Construction dust and particulate, particularly drywall dust, will cause contamination of
the burner, resulting in possible severe personal injury, death or substantial property damage. The boiler can only be operated with a dust-
free air supply. Follow the instruction manual procedures to duct air to the boiler air intake. If the boiler has been contaminated by operation with
contaminated air, follow the instruction manual guidelines to clean, repair or replace the boiler if necessary.
Affix these instructions near to the boiler/water heater. Instruct the building owner to retain the instructions for future use by a qualified
service technician, and to follow all guidelines in the User’s Information Manual.
VGX
Gas-Fired Residental
Boilers
Models 88-288 – Steam Only
Boiler Manual
Installation and
Operation Instructions
VGX2-213
22-VGX2