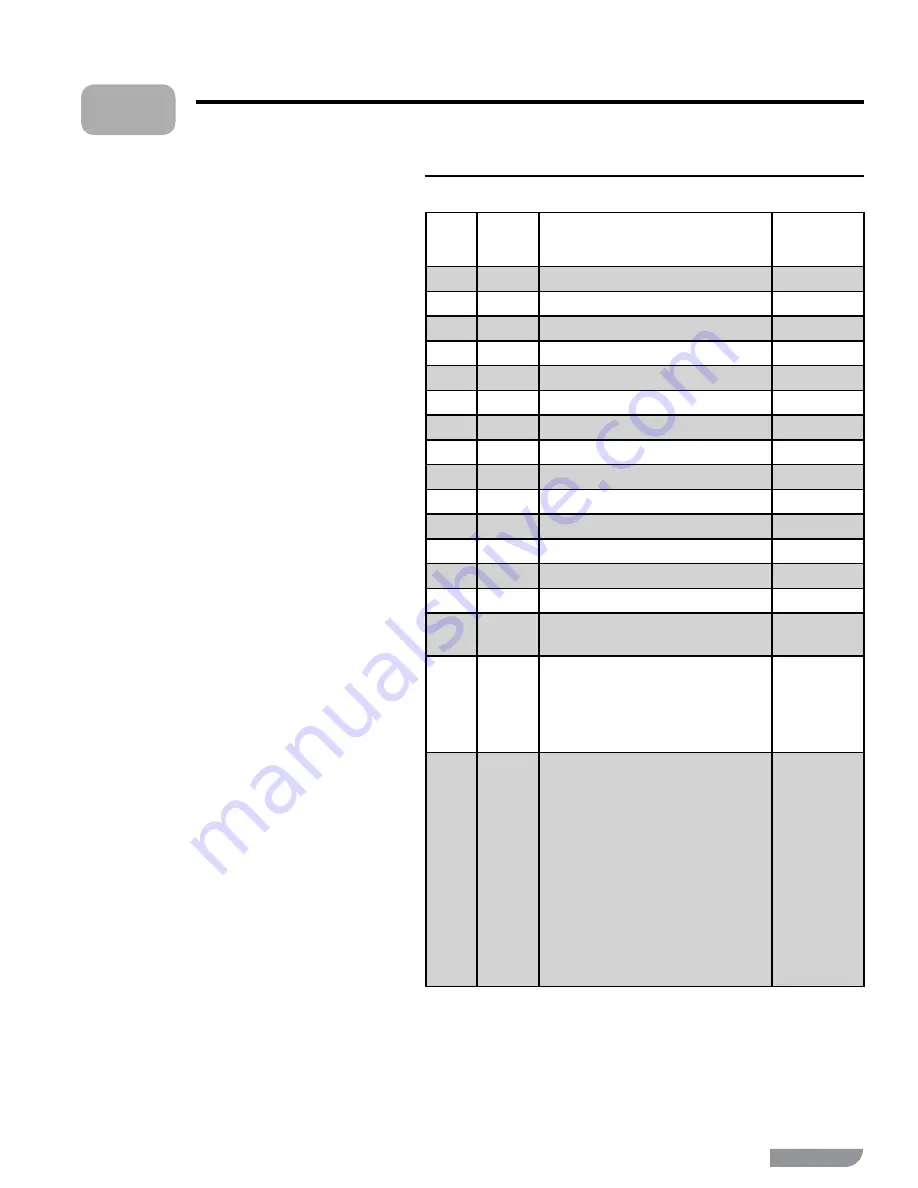
15
P/N 42-9452 8/08 Copyright Hydrotherm
KN USER’S CONTROL MANUAL
Method 2: HeatNet modulation – BMS control
(cont.)
2
Table 5
Modbus input (read-only) registers
Address
Data
Type
Description Valid
Values/
Range
30001
Unsigned Boilers Running
0 – 16
30002
Unsigned Modulation (% BTU Load)
0 – 100
30003
Signed
Header / System Temperature
32 – 250 °F
30004
Signed
Supply Temperature
32 – 250 °F
30005
Signed
Return Temperature
32 – 250 °F
30006
Signed
Outside Air Temperature
-40 – 250 °F
30007
Signed
Spare Input 1
-32768 to 32767
30008
Signed
Spare Input 2
-32768 to 32767
30009
Unsigned Clock – Month
0 – 11
30010
Unsigned Clock – Day
1 – 31
30011
Unsigned Clock – Year
0 – 99
30012
Unsigned Clock – Hours
0 – 23
30013
Unsigned Clock – Minutes
0 – 59
30014
Unsigned Clock – Seconds
0 – 59
30015
Unsigned Clock – Day of Week
1 – Monday 7 –
Sunday
30016 –
30047
Unsigned Boilers 1 – 16 status fl ag (32-bit) registers. The
upper 16-bits of each 32-bit register is stored at
odd numbered addresses 30016 –30046. The
lower 16-bits of each 32-bit register is stored at
even numbered addresses 30017 – 30047.
See the Boiler
Status Flags
Table Below
30048 –
30079
Unsigned Boilers 1 – 16 runtime (32-bit) registers. The
upper 16-bits of each 32-bit register is stored at
odd numbered addresses 30048 – 30078. The
lower 16-bits of each 32-bit register is stored at
even numbered addresses 30049 – 30079.
When the upper and lower registers are combined
they form a 32-bit unsigned integer that is the
number of seconds that the boiler has been
running. For instance: (((Register 29) * 65536)
+ Register 30) = Boiler 1 runtime in seconds.
Boiler 1 is the master boiler. Boilers 2 – 16 are
member boilers.
0 – 4294967295
seconds
BACnet or LonWorks protocols
Install the correct bridge to adapt to building management
systems using BACnet or LonWorks protocols.
Th e bridge translates the BACnet or LonWorks input to
the Modbus protocol for compatibility with the HeatNet
controls.
Wiring and set-up
Wire and set up the master boiler and member boilers exactly
as for HeatNet modulation — local control applications.
See page 6 through page 13.
ALL control parameters must be set up just as for the local
control method.
Th
e ONLY diff erence in setup is the termination DIP switch
sett ings. Use the sett ings for Modbus communications given
in Table 1, page 11.
Connect communications cables (RJ45 or shield-wire
cables) between the control communications boards as for
the local control method.
Verify network operation BEFORE connecting the building
management system.
Connect the BMS cable
DO NOT connect the building management system cable
until the boiler network has been proven to operate inde-
pendently. Th
e system is designed to revert to local control
by the master boiler should communications with the
building management system be lost.
Turn off power to the master boiler.
See Figure 10, page 13. Connect an RJ45 cable to the BMS
input port, item 6. Or use shielded wire cable, connected to
terminal block, item 3.
Verify BMS/HeatNet operation
Turn on power to the master boiler.
Allow the master boiler to initialize.
Verify operation with the building management system.
1.
2.
1.
2.
3.
4.
5.
1.
2.
3.
1.
2.
3.