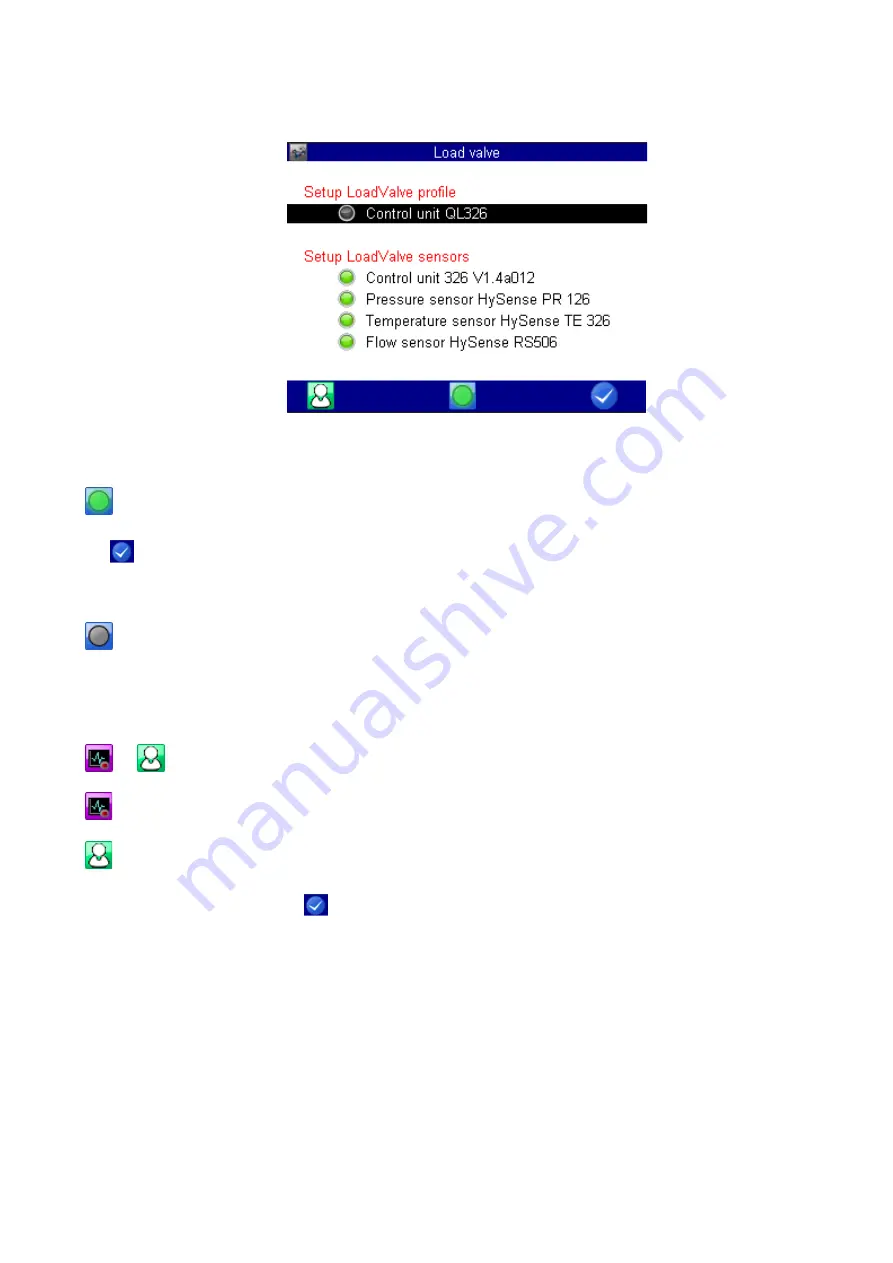
Activation QL326
When all relevant traffic lights of the sensor system are "GREEN", the load distance can be activated.
ONLINE / OFFLINE - Mode
Switches the load valve to the ONLINE mode. The button colour of the control unit changes to
green
. A
correction of the parameters is no longer possible.
F5 takes you directly to the menu of the measured value display. All active sensors are added to the dis-
play indication. A manual correction is possible later. In the measured value display, you have an additional soft-
key bar for sequence control of the load valve.
Switches the load valve to the OFFLINE mode. The button colour of the control unit changes to
GREY
. The
correction of parameters is possible again.
Storing measured values
or
The function key F1 switches between both states.
When starting a test cycle, the storage is automatically activated.
When starting a test cycle, the storage is not automatically activated. You must set up a storage yourself.
When leaving this menu with F5 , the required storage time is calculated from the current parameter settings
and all active sensors of the load valve are added to the display.
The display can be adjusted manually via the channel settings.