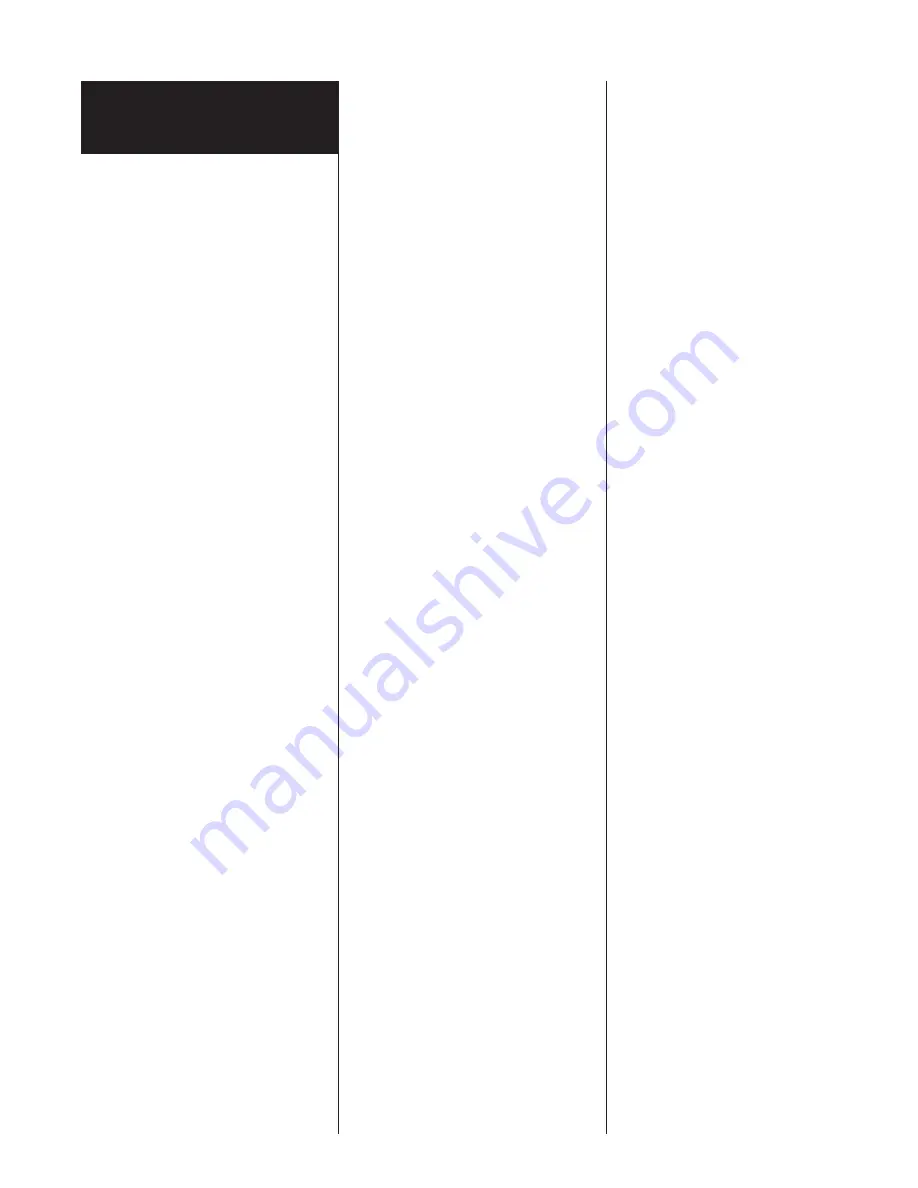
3
Pump
Servicing
power cord from terminals in
control panels (manual pump
models) and power
source
(automatic models) and remove
pump from sump.
1. Clean any dirt or trash from
the outside of the pump before
dismantling.
If the unit is being operated by
float or diaphragm switch,
unplug the pump from the
piggyback receptacle and plug
the pump directly into the
power source. If the pump
starts each time it is plugged
directly into the receptacle and
does not start each time when
plugged into the piggyback
switch with the float raised or
the diaphragm switch pressed
into the start position, replace
the complete piggyback switch
assembly and retest with
new assembly.
2. If motor does not run when
tested as described above, the
capacitor and/or stator must
be checked.
Disconnect from power supply.
Remove plug (#6) from top of
housing and pour oil into
container, preferably clear, so
that oil can be observed.
3. If oil is clear, it will indicate
motor is not burned and there
has been no water leak into the
motor. If oil is cloudy, it will
indicate water in motor, or, if
oil is black, it will indicate a
burned stator.
4. After draining oil, carefully
loosen the power cord
assembly (#22) from the motor
housing (#2). With power cord
loose, remove the four wire
nuts and screws (#4) and
carefully lift off the motor
housing (#2) exposing the
capacitor (#28) (1ø only) and
the motor assembly.
b. pump motor or bearings
may be defective
c. start capacitor in motor may
have failed
d. pump may be miswired to
terminal block
e. head is lower than rating,
pumping too much liquid
6. Air locked pump. Disconnect
piping at union and run until
all air bubbles are expelled.
7. Wrong impeller rotation.
Rotation should be
counterclockwise when looking
at the impeller. Correct improper
rotation on three phase pumps
by reversing any two line
leads. No rotation check is
necessary on single phase pumps.
8. Closed discharge gate valve.
9. Plugged impeller or pipeline.
10.Discharge head may be too
high. Check elevation against
design point of pump.
11. Floats not hanging free in
the sump.
12.Malfunctioning floats.
Disconnect power supply.
Checking Power Cord
To be sure wires are not burned
off or broken in cord, use ohmmeter
for check. Set ohmmeter scale
pointer to R x 1 scale and attach
one meter lead to white cord wire
and one meter lead to black cord
wire, then place a screwdriver
blade across terminals of plug. If
cord is OK, meter needle will go
to zero and stay there. If meter
needle does not move, this will
indicate an open wire and cord
must be replaced.
Motor
Warning: Be certain power to
pump is off! Disconnect pump
Read the following instructions
carefully before replacing any
parts. Reasonable care and safe
methods should be practiced.
Check local codes and
requirements before installation.
Only a competent electrician
should make the installations.
Tools Required
General shop tools include socket
wrenches and a bearing puller.
An ohmmeter is required
to thoroughly check motor
and wiring.
For proper automatic operation,
make sure the pump power
cord is plugged into the
piggyback receptacle on the float
switch cord.
Before removing the pump from
its installation for repairs, check
first to see if the trouble is
caused by:
1. Miswiring of the pump into
the terminal block.
2. Miswiring of the float level
controls into the panel.
3. Miswiring inside the control
panel.
4. Trip circuit breaker. If the
breaker is manually reset and
then trips off again, the
problem could be:
a. short circuit in motor or
control panel
b. water in the motor housing
c. insufficient amp capacity of
wiring or breakers
d. improper panel wiring
5. Tripped overload. If overload
is manually reset and then
trips off again, the problem
could be:
a. pump or piping is clogged
Summary of Contents for SPD100H
Page 4: ...4 SPD100H SPD50H ...