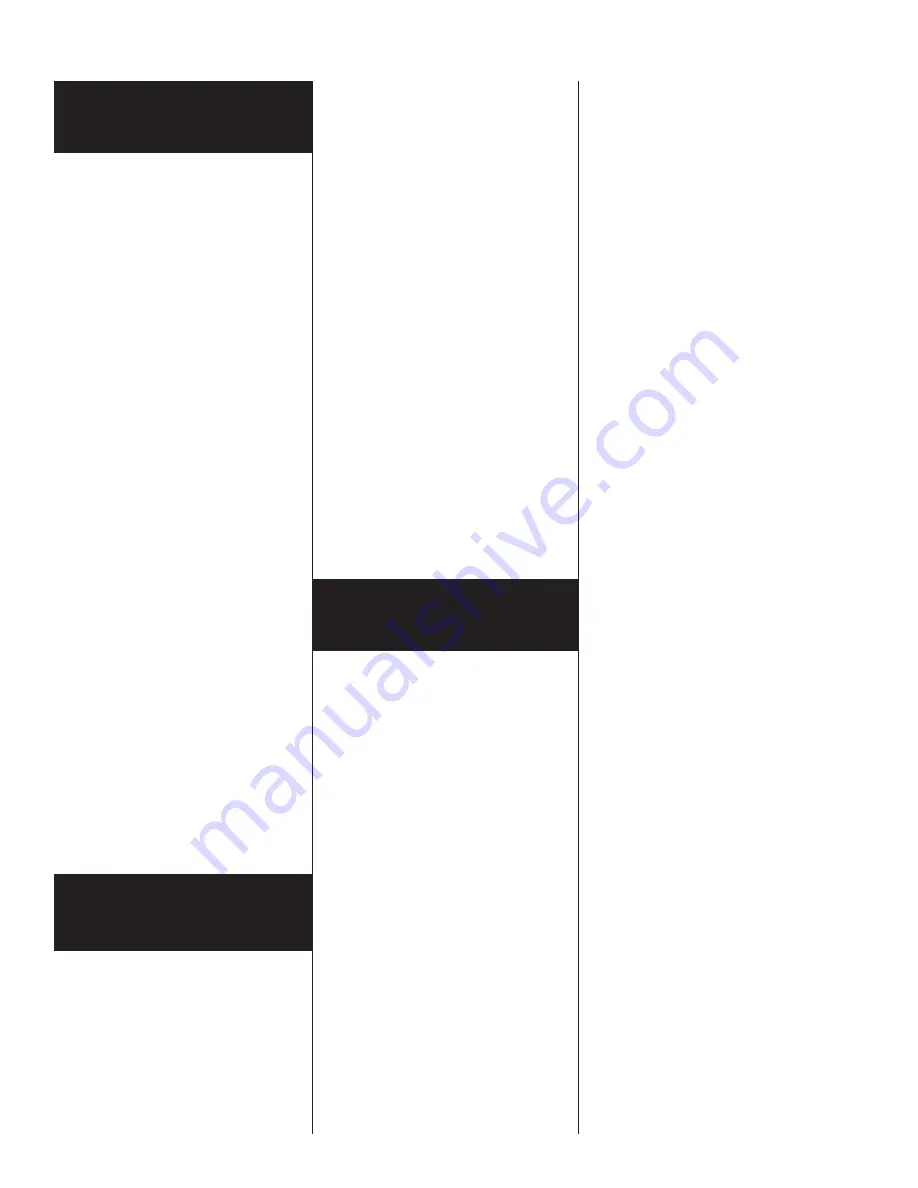
2
Thank you for purchasing your
Hydromatic
®
pump. To help
ensure years of trouble-free
operation, please read the
following manual carefully.
Before Operation:
Read the following instructions
carefully. Reasonable care and
safe methods should be practiced.
Check local codes and
requirements before installation.
Attention:
This manual contains important
information for the safe use of
this product. Read this manual
completely before using this
product and refer to it often for
continued safe product use.
DO NOT THROW AWAY OR
LOSE THIS MANUAL. Keep it
in a safe place so that you may
refer to it often.
WARNING: Before handling
these pumps and controls,
always disconnect the power
first. Do not smoke or use
sparkable electrical devices or
flames in a septic (gaseous) or
possible septic sump.
To reduce risk of electrical shock:
1.
Risk of Electrical Shock:
This pump has not been
investigated for use in
swimming pool areas.
2.
Risk of Electrical Shock:
Connect only to a properly
grounded receptacle.
Septic tank to be vented
in accordance with local
plumbing codes.
Do not smoke or use sparkable
electrical devices or flame in a
septic (gaseous) or possible
septic sump.
If a septic sump condition may
exist and if entry into sump is
necessary, then (1) provide
proper safety precautions per
OSHA requirements and (2)
do not enter sump until
these precautions are strictly
adhered to.
Do not install pump in location
classified as hazardous per
N.E.C., ANSI/NFPA 70 - 1999.
Failure to heed above cautions
could result in injury or death.
General
Information
Pump
Warning
not solid. Raise the pump by
placing bricks or concrete
blocks underneath it.
5. Use steel or plastic pipe for all
connecting lines between
pump and sewer outlet.
Note: Some city regulations
do not allow installing a
pump with plastic pipe. Check
local regulations.
6. In applications where the
pump may sit idle for months
at a time, it is recommended
that the pump(s) be cycled
every month to ensure the
pumping system is working
properly when needed.
7. Hydromatic check valve
should be installed in discharge
pipe. Install check valve with
arrow on valve body pointing
in the direction of the flow.
8. A shutoff valve should also
be used.
9. An audible alarm system, such
as the Q Alert, for high water
conditions should be installed
in every pump pit for greater
protection.
Note: The Q Alert is for
indoor use only. For outdoor
applications contact your
Hydromatic distributor.
10.Connect to power source
using 3-prong grounded AC
receptacle. Do not remove
ground pin from electrical
plug. Do not use an extension
cord or adaptor plug.
11. For proper automatic operation,
make sure the pump power
cord is plugged into the back
of the piggyback receptacle on
the wide angle float switch.
These important instructions must
be followed for satisfactory
performance of your pump. Before
installation, check your local
electrical and plumbing codes.
1. Provide proper sump.
Recommended minimum
sump diameter is 18".
2. Make sure the wide-angle
float switch (excluding those
automatic models equipped
with a diaphragm pressure
switch) hangs freely. The float
should not come in contact
with the side or bottom of the
sump pit.
3. Make sure sump is free of
string, cloth, nails, gravel, etc.
before installing pump.
4. Do not set pump directly on
the bottom of sump pit if it is
Pump
Installation