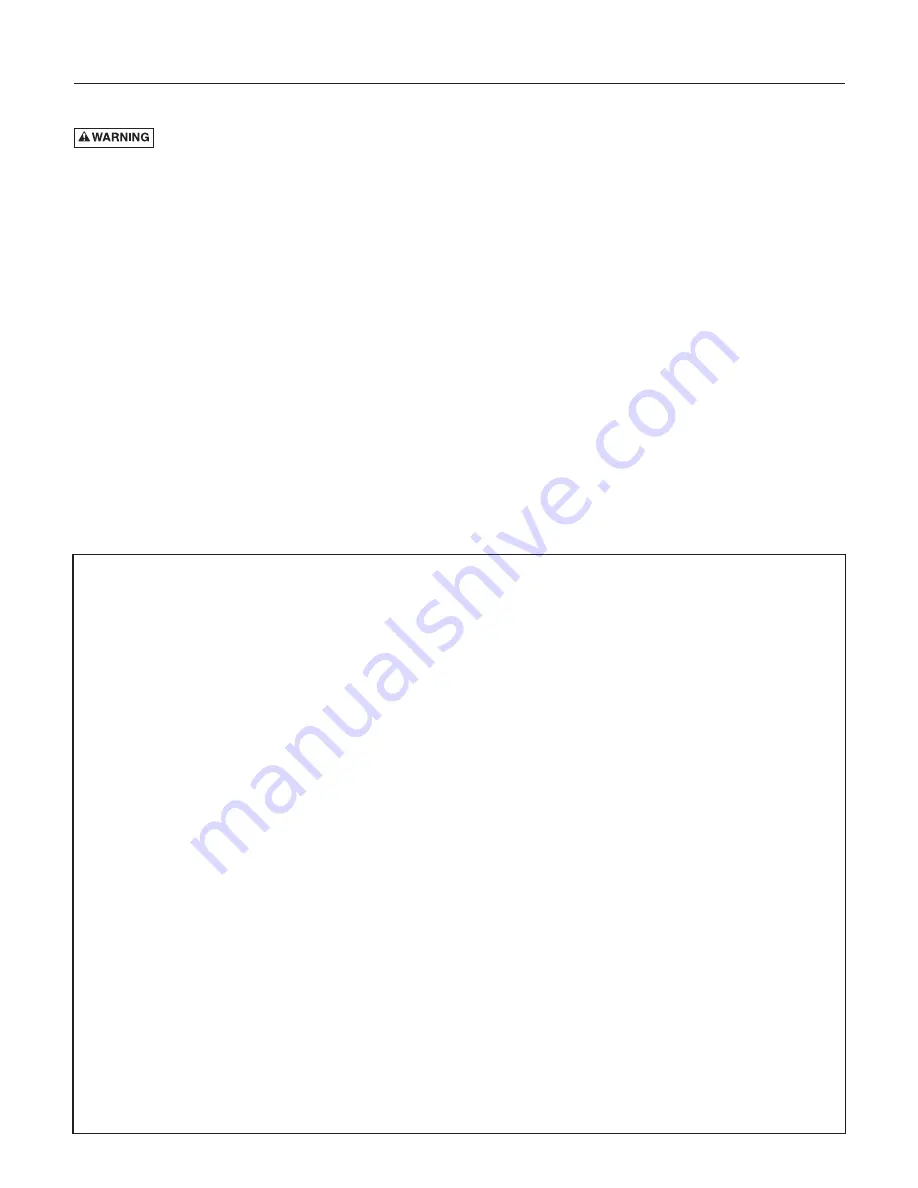
LIMITED WARRANTY
HYDROMATIC warrants to the original consumer purchaser (“Purchaser” or “You”) of HYDROMATIC products
that they will be free from defects in material and workmanship for the Warranty Period of (whichever occurs
first): 12 months from date of original installation, or 36 months from date of manufacture.
Our warranty will not apply to any product that, in our sole judgement, has been subject to negligence, misap-
plication, improper installation, or improper maintenance. Without limiting the foregoing, operating a three
phase motor with single phase power through a phase converter will void the warranty. Note also that
three phase motors must be protected by three-leg, ambient compensated, extra-quick trip overload relays of
the recommended size or the warranty is void.
Your only remedy, and HYDROMATIC’s only duty, is that HYDROMATIC repair or replace defective products
(at HYDROMATIC’s choice). You must pay all labor and shipping charges associated with this warranty and
must request warranty service through the installing dealer as soon as a problem is discovered. No request
for service will be accepted if received after the Warranty Period has expired. This warranty is not transferable.
HYDROMATIC SHALL NOT BE LIABLE FOR ANY CONSEQUENTIAL, INCIDENTAL, OR CONTINGENT
DAMAGES WHATSOEVER.
THE FOREGOING WARRANTIES ARE EXCLUSIVE AND IN LIEU OF ALL OTHER EXPRESS AND
IMPLIED WARRANTIES, INCLUDING BUT NOT LIMITED TO THE IMPLIED WARRANTIES OF
MERCHANTABILITY AND FITNESS FOR A PARTICULAR PURPOSE. THE FOREGOING WARRANTIES
SHALL NOT EXTEND BEYOND THE DURATION EXPRESSLY PROVIDED HEREIN.
Some states do not allow the exclusion or limitation of incidental or consequential damages or limitations on
the duration of an implied warranty, so the above limitations or exclusions may not apply to You. This warranty
gives You specific legal rights and You may also have other rights which vary from state to state.
This warranty supersedes and replaces all previous warranty publications.
HYDROMATIC
740 East 9th Street, Ashland, OH 44805
Phone: 888-957-8677 • Fax: 888-840-7867 • Web Site: http://www.hydromatic.com
Risk of asphyxiation or poisoning. Never
enter pump chamber after sewage or effluent has been
in basin.
Sewage water can give off methane, hydrogen
sulfide, and other gases which are highly poisonous. For
this reason, we recommend installing effluent pumps
with a quick removal system. The quick removal system
may be a union or Cam-lok® coupling if the pipe or
discharge hose is within reach from the surface, or a rail
system type quick disconnect on deeper installations.
See installation drawings for suggested installation.
The dosing tank or pumping chamber must be
constructed of corrosion resistant materials and must be
capable of withstanding all anticipated internal and
external loads. It also must not allow infiltration or exfil-
tration. The tank must have provisions for anti-buoy-
ancy. Access holes or covers must be adequate size and
be accessible from the surface to allow for installation
and maintenance of the system. Access covers must be
lockable or heavy enough to prevent easy access by
unauthorized personnel. The pumping chamber holding
capacity should be selected to allow for emergency
conditions.
The discharge pipe must be the same size as the pump
discharge, 2" or larger. In order to insure sufficient fluid
velocity to prevent any residual solids from collecting in
the discharge pipe, it is recommended that a minimum
flow of 2' per second be maintained. (21 GPM through
2" pipe and 46 GPM through 3" pipe). It is recom-
mended that PVC or equal pipe is used for corrosion
resistance. A full flow (ball or gate) shut-off valve must
be installed to prevent back flow of effluent if the pump
must be removed for service. A check valve must be
installed on pressure sewer systems and on other
systems (where conditions allow) to prevent back flow
and to reduce wear on the pump system.
A high water alarm must be installed on a separate
circuit from the pump circuit. The alarm should have
the ability to be tested for proper operation.
Installation
4