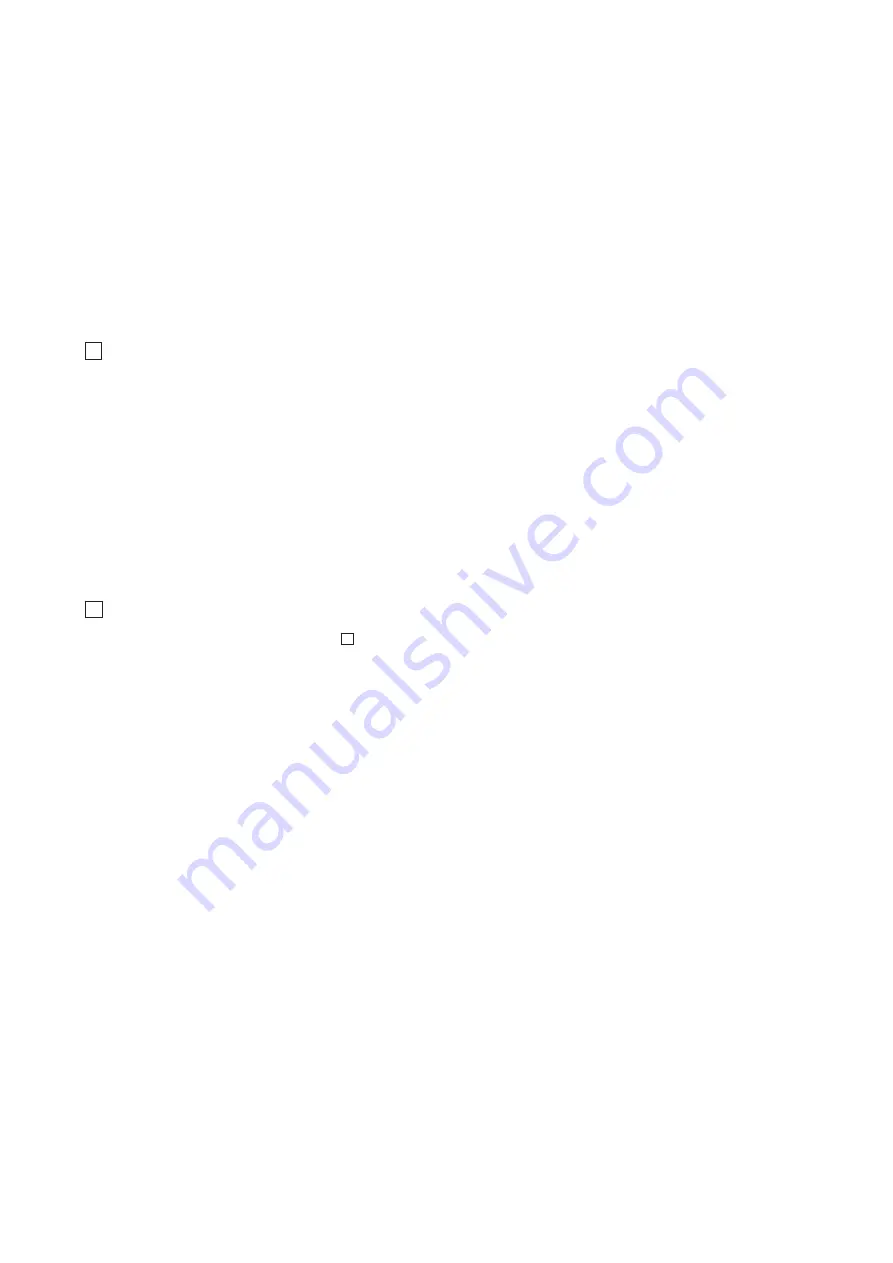
12
PROGRAMMING DEVICES
The functional parameters of digital controllers, like internal reference generation or controller dynamics, can be easily set and optimized with the Atos
Z-SW programming software, available in three different versions according to the driver’s communication interface: Z-SW-PS (Serial), Z-SW-BC
(CANopen) and Z-SW-BP (PROFIBUS DP).
A proper connection is required between the PC and the electronic controller communication port: for a more detailed description of software interface,
PC requirements, adapters, cables and terminators, please refer to technical table
G500
.
Digital controllers with fieldbus communication interface (-BC and -BP) can be managed in real-time by the machine control unit; it is required to imple-
ment in the machine control the standard communication as described in the user manuals supplied with the relevant programming software; please con-
tact Atos technical office for assistance.
Programming software, must be ordered separately:
Z-SW-*
(mandatory - first supply) = Dvd including Z-SW-* software installer and operator manuals; it allows the registration to Atos digital service
Z-SW-*-N
(optional - next supplies) = as above but not including the registration form for Atos digitals service
On first supply of the Z-SW-* software, it is required to apply for the registration in the Atos download area: www.download.atos.com .
Once the registration is completed, the password will be sent by email.
The software remains active for 10 days from the installation date and then it stops until the user inputs his password.
With the password it is also possible to download the latest releases of the Atos software, manuals, drivers and configuration files.
USB Adapters, Cables and Terminators, can be ordered separately (see tab. G500)
13
MAIN SOFTWARE PARAMETER SETTINGS
11.14 Digital input signals (DI1 - DI8)
The 8 digital inputs can be used to trigger a command or to read a system state. For each input by the Z-SW software, it is possible to set the polarity and
to match a proper condition within the following:
- start/stop/switch-over command in case of internal reference generation (see 3.2)
- specific operative command for hydraulic axis mode (referencing mode, jog mode, automatic mode)
- jog command
- disable pressure / force alternated control
11.15 Digital output signals (DO1 - DO7)
The 7 digital outputs can be used to generate digital signals useful to the system synchronization and for monitoring purpose. The digital outputs can be
configured in polarity and all the channels can be independently programmed by the Z-SW software.
Typically the digital outputs are used to:
- set alarm condition related with the hydraulic axis working phase
- identify a particular working condition to synchronize other machine functionalities
- signal target position reached
- signal pressure / force control active
- signal tracking error
11.16 CANopen communication signals (only for /BC option)
For controllers with CANopen communication interface (only for /BC option), the connections are located on the rear connector: pin f28 (CAN_GND), pin
f30 (CAN_L) and pin f32 (CAN_H).
G340
For a detailed descriptions of the available settings, wirings and installation procedures, please refer to the programming manual Z-MAN-ME-KZ included
in the Z-SW-* Dvd programming software (see section
).
13.1 External reference and transducer parameters
Allow to configure the controller reference and transducer inputs, analog or digital, to match the specific application requirements:
-
Scaling parameters
define the correspondence of these signals with the specific actuator stroke or force to be controlled
-
Limit parameters
define maximum/minimum stroke and force to detect possible alarm conditions
-
Homing parameters
define the startup procedure to initialize incremental transducer (e.g. encoder)
13.2 Position PID control dynamics parameters
Allow to optimize and adapt the position controller closed loop to the wide range of hydraulic system characteristics:
-
PID (position)
each part of the position controller closed loop algorithm (proportional, fine positioning advanced integral, derivative, feed
forward, etc.) can be modified in order to match the application requirements.
13.3 Multiple pressure/force PID control dynamics parameters
Allow to optimize and adapt the pressure/force controller closed loop to the wide range of hydraulic system characteristics:
-
PID (pressure/force)
each part of the pressure/force controller closed loop algorithm (proportional, integral, derivative, feed forward, etc) can be
modified in order to match the application requirements. Through Atos software or using dedicated digital inputs it is possible
to select up to four different pressure/force PID parameters setting, stored into the controller. Switching the active setting of
pressure/force PID during the machine cycle allows to optimize the system dynamic response in different hydraulic working
conditions (volume, flow, etc.).
13.4 Control output signal parameters
Allow to configure the controller command for the proportional valve which regulates the hydraulic flow to the actuator:
-
Scaling parameters
define the correspondence of the command signal to the specific valve reference signal range
-
Limit parameters
define maximum/minimum range to detect possible alarm conditions
13.5 Monitoring parameters
Allow to configure the controller monitoring function of the positioning error (difference between actual reference and feedback) and detects anomalous
conditions:
-
Monitoring parameters
maximum allowed errors can be set for both static and dynamic positioning phases, and dedicated waiting times can be set to
delay the activation of the alarm condition and relevant reaction (see 13.6)
13.6 Fault parameters
Allow to configure how the controller detect and react to alarm conditions:
-
Diagnostics parameters
define different conditions, threshold and delay time to detect alarm conditions
-
Reaction parameters
define different actions to be performed in case of alarm presence (stop at actual or preprogrammed position, emergency
forward/backward, controller disabling, etc.)
13.7 Digital IO configuration
Allow to configure the controller’s digital inputs/outputs to trigger/generate signals from /for the external machine central unit:
- Polarity
define the signal active state
- Trigger condition
define the input state to run a predefined internal command (see 11.14)
- Output state
define the digital output based on the internal controller state (see 11.15)
13.8 Motion phases parameters
When the internal reference generation is active a pre-programmed cycle can be generated; start/stop/switch-over commands and reference generation
types parameters can be set to design a customized sequence of motion phases adapted to the specific application requirements (see 3.2).
12