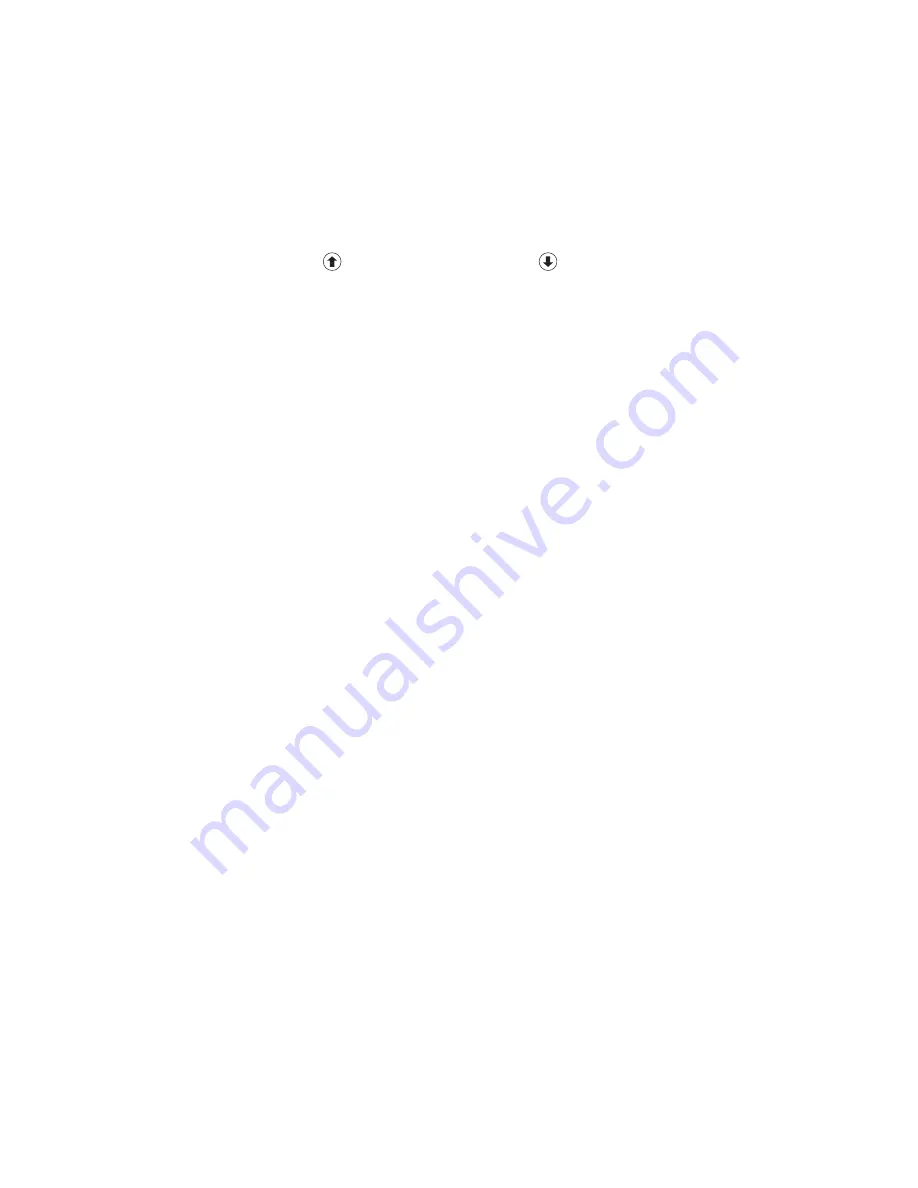
15
VIII. TROUBLESHOOTING
A.
FACTORY DEFAULT
– If there is an electronics problem that cannot be solved by any of the below
efforts, then you might consider performing a factory default. However, when this is done all calibration
data is lost and must be reset. Therefore it is best to try other steps fi rst because you will have to go
through both the Advance Calibration Mode and the Confi guration Mode to enter all control and calibration
settings. The factory default can eliminate glitches that may arise in the software by erasing all settings
and entering the factory default settings. In order to perform a factory default follow these steps:
1. Turn off the power to the HC-220.
2. Hold both the “up arrow”
key and the “down arrow”
key on the front panel.
3. While holding both keys, turn on the power to the HC-220.
NOTE: After reapplying the factory defaults you will have to re-calibrate the controller’s input and
output signals.
B.
POSSIBLE PROBLEMS
and Recommended Steps to take:
1.
Insuffi cient or Excessive Chemical Feed in Proportional/Flow Pacing Control.
a.
Adjust Dosage Level
– See Section V.1b. Increase dosage for more chemical feed and decrease
dosage for less.
b.
Check Items 1a. – 1d. above
– If actual chemical feed remains low, then check the suggestions in
item 1a. through 1d. above.
2.
Failure to reach set point in Residual/ORP or Compound Loop Control.
a.
Lag Times
– The lag times set in section III.2.m or III.3.a through III.3.c may be too long for the
system.
b.
Integral
– The integral value set in section III.2.l may be too low. If it is too low then the HC-220
will not react quickly enough to reach set point.
c.
Dead Band
– The dead band set in section III.2.k may be too large. The valve will consider set
point met if Residual/Other remains within this amount of set point.
3.
Repeated Overshooting of Set Point in Residual/Other or Compound Loop Control.
a.
Lag Times
– The lag times set in section III.2.m or III.3.a through III.3.c may be too short for the
system.
b.
Integral
– The integral value set in section III.2.l may be too high. If it is too high then the HC-220
will react too quickly and it will repeatedly drive the Residual/Other reading below and above set
point.
c.
Dead Band
– The dead band set in section III.2.k may be too small. The valve will only consider
set point met if Residual/Other remains within this amount of set point. If it is set to zero the
HC-220 will almost never be satisfi ed and will continue to adjust the valve position.
iv. Thread the Valve Stem hand tight onto the Intermediate Valve Stem.