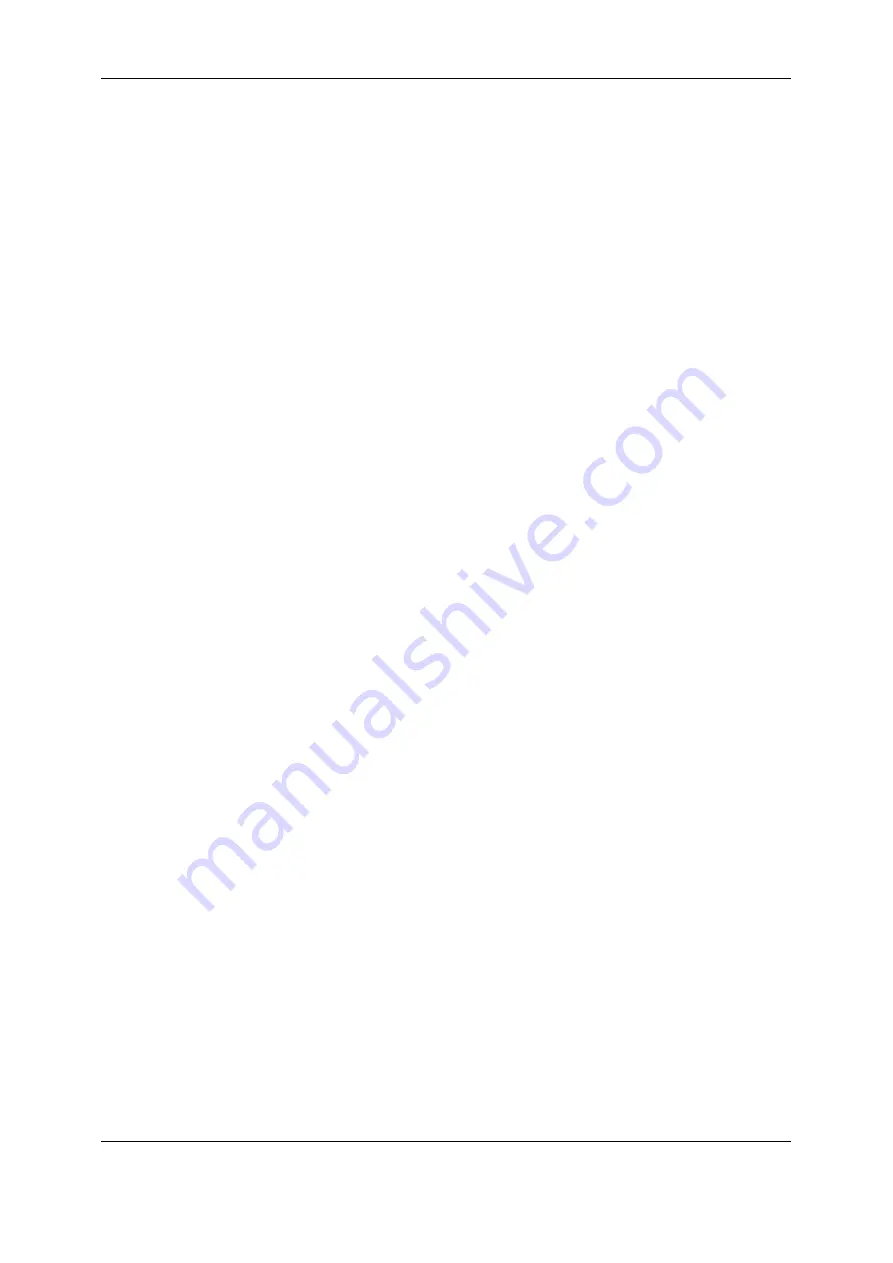
MRF 2 NU MultiRheo Filter
5
Maintenance and Servicing
5.1 General
Below follows a description of the maintenance and servicing to be performed at regular
intervals. The filter’s serviceability, operational reliability and service life substantially depend
on performing maintenance and servicing work regularly and carefully.
5.2 Maintenance
Measures
•
The replacement parts have to satisfy the manufacturer’s technical specifications. This is
ensured when HYDAC original parts are used.
•
Tools, working area and equipment are to be kept clean.
•
After taking the filter apart, clean all components, checking them for damage or wear. If
necessary, replace them.
•
When replacing a filter element, extreme care is to be taken that no dirt or other foreign
matter is introduced.
5.3
Frequency of Changing the Filter Elements
The filter is equipped with a clogging indicator for monitoring the filter elements.
When the clogging indicator is triggered this shows that the filter element has to be replaced
immediately.
When no clogging indicator has been fitted, we recommend that elements be changed in
specific intervals, however at least once a year. (The frequency of changing the filter
elements depends on the filter design and the conditions under which the filter is operated.)
When filter elements are subjected to high dynamic loading it may prove necessary to
change them more frequently. The same applies to commissioning, repair work or hydraulic
fluid oil changes.
Standard clogging indicators are not triggered unless there is a flow through the filter. As to
electrical clogging indicators, the output signal can also be processed and indicated on the
control panel continuously until acknowledging the fault by eliminating it (i.e. changing the
filter element(s) and cold-starting the system).
If the clogging indicator is only triggered upon cold-starting, this may indicate that the filter
element(s) may not yet require changing.
HYDAC Filtertechnik GmbH
en
Page 14
BeWa MRF2NU 3341025 en.doc
2007-09-24