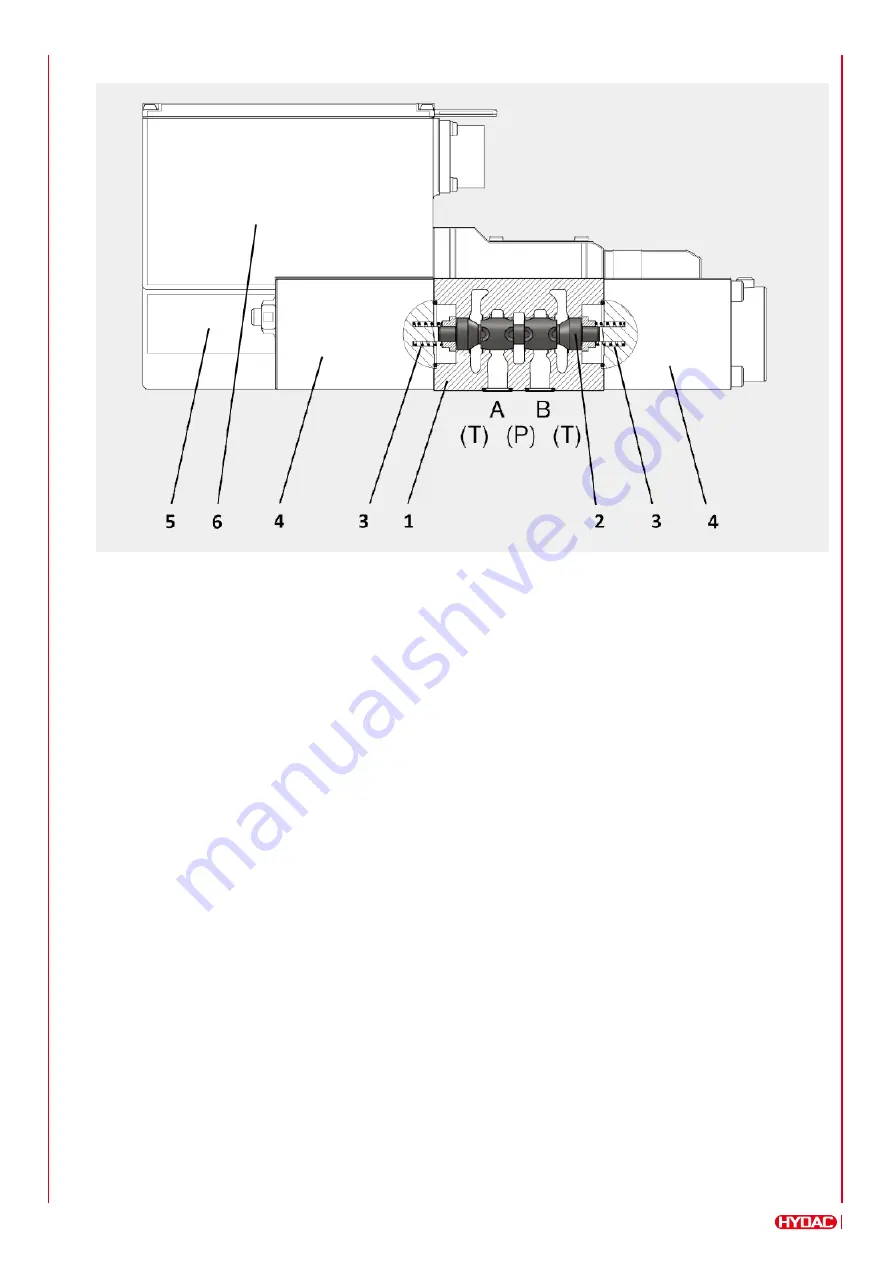
5
1.5 DESCRIPTION OF FUNCTION
The solenoid-operated proportional directional spool valves of type C4WERE 6 are used to control a flow
precisely and dynamically.
The valve comprises a valve housing (1) with corresponding valve piston (2). It has two return springs (3)
and is fitted with two powerful regulating solenoids (4), a positional transducer (5) and on-board electronics
(6).
The on-board electronics convert an analogue nominal value signal into a proportional piston displacement
in relation to the return spring. This causes the nominal flow directions between the respective connections
to be released or closed. The force needed to perform the displacement is generated by the solenoid. The
positional transducer constantly records the current position and the on-board electronics compare the actual
position with the target position and set the pilot flow to the level required to correct any difference. This
makes it possible to have a steadily increasing flow even if the pressure difference across the valve is
increasing.
If the valve is de-energised, the return springs return the valve piston to a safe position (fail-safe function as
an option).
1.6
FIELDS OF APPLICATION
The valve is used in the following applications, for example:
•
Injection moulding machines
•
Grinding machines
•
Blow moulding technology
•
Honing machines
•
Steelworks
•
Wood processing
•
Machine tools
If you plan on using the valve for other fields of application, please consult with our technical department
before initial start-up.
E
N
5.
9
07.
6.
B
A
.
0/
10.
20