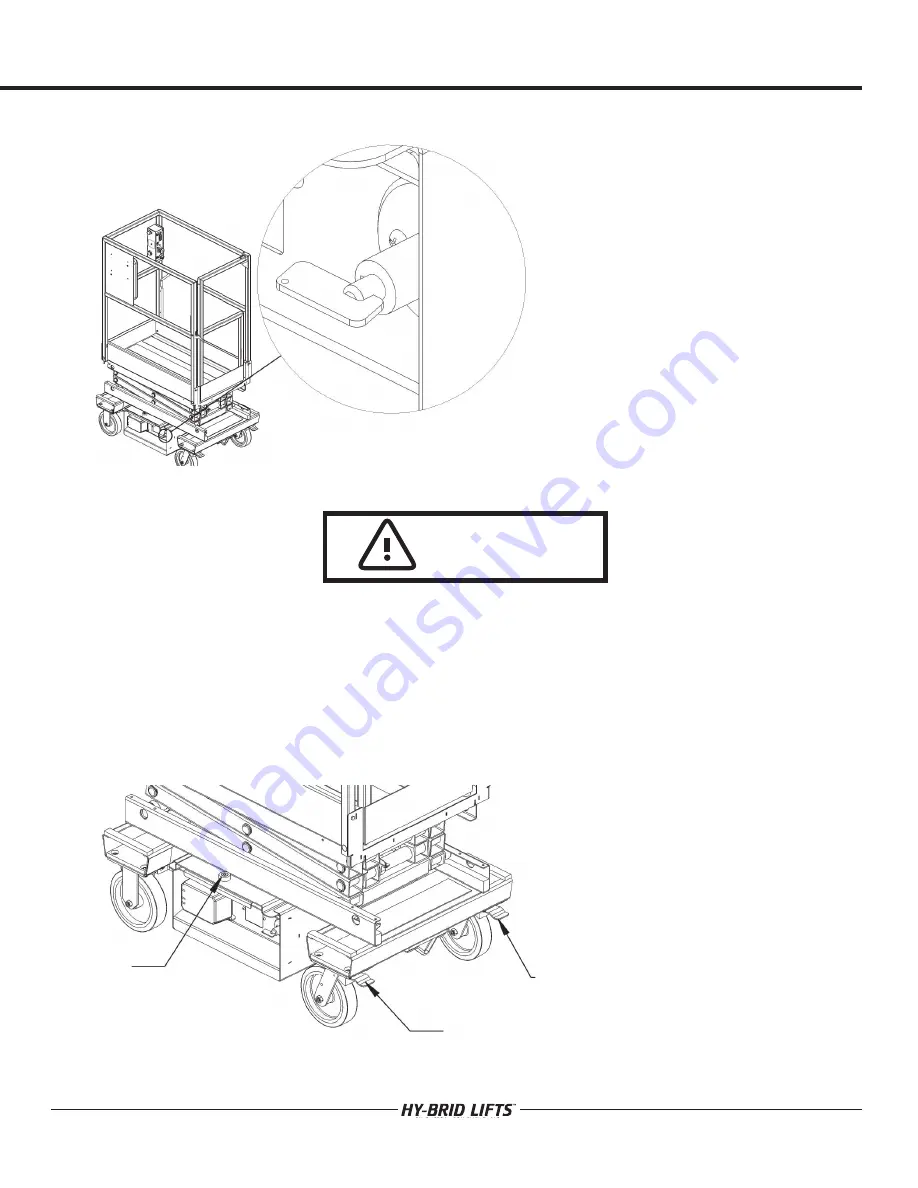
Operation & Safety Manual
HB-P4.5 / HB-P5.0
SUPO 647
REV D
18
5.3 | Startup/Shut Down
Check that the work area is safe.
It is not recommended to maneuver
the unit on a slope greater than 5°.
Check that master power switch is in
“ON” position.
Ensure that the key in the lower con-
trol panel is in the “ON” position for
the chassis or platform control.
Machine must be on a hard, level,
surface before operation. Check that
bubble level is centered.
Engage the manual brakes on the
rear casters before elevating the plat-
form.
DANGER
THE OPERATOR MUST BE AWARE OF THE ENVIRONMENT. DO NOT RAISE THE PLATFORM IF
THE MACHINE IS NOT ON A FIRM, LEVEL SURFACE.
Enter the work platform in the stowed position using the constant three point contact method.
Follow all general rules and precautions stated in this manual.
When finished with the machine, place the platform in the stowed position.
Carefully exit the platform using the constant three point contact method.
NEVER JUMP OFF PLATFORM.
Park the machine on a level surface.
Remove key from lower control pan-
el to prevent unauthorized use.
Figure 9: Master Power Switch
Figure 10: Rear Brakes and Bubble Level
SECTION 5 | OPERATION