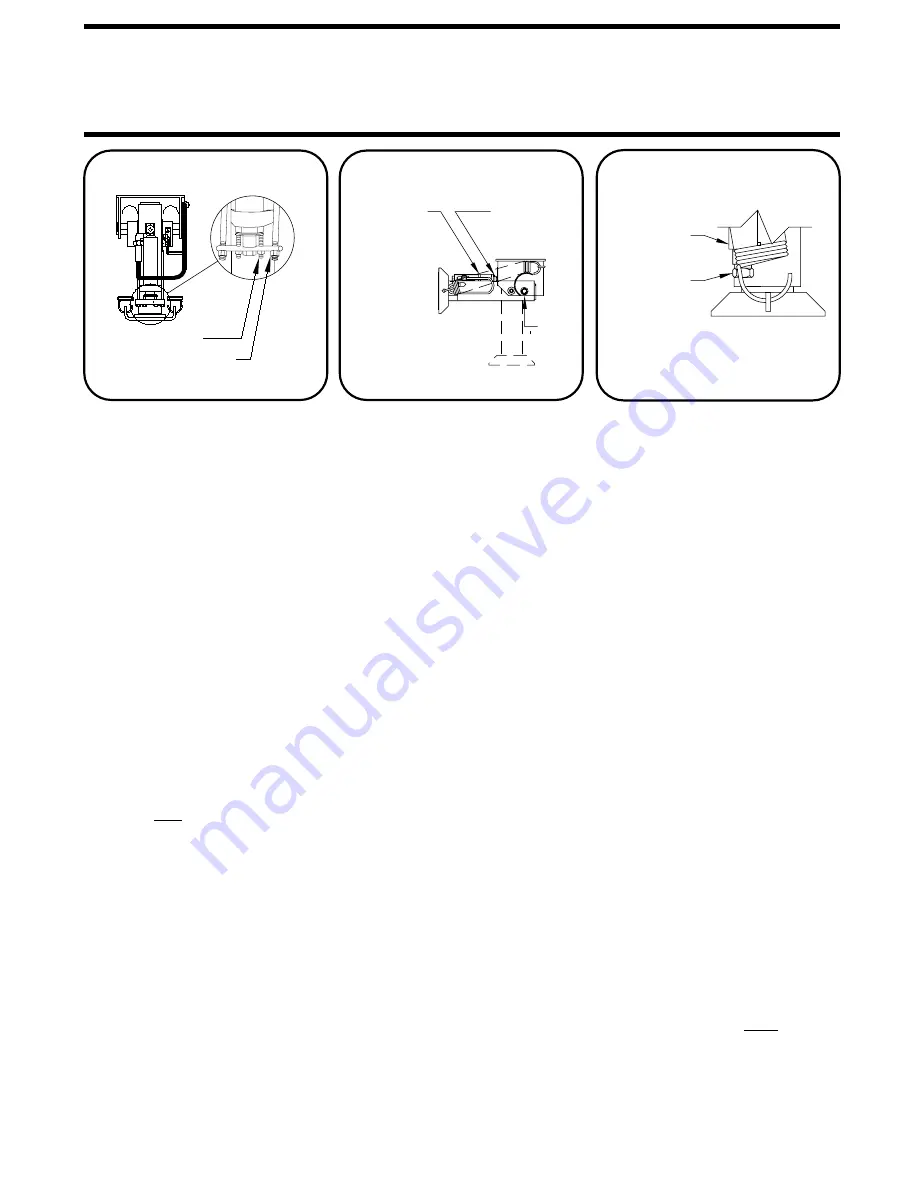
START-UP & ADJUSTMENTS
MI35.2505
02JAN96
Do NOT operate system without having the ground
FIGURE 10
16000# JACK
FIGURE 11
SET SCREW
ADJUSTING
HEAVY DUTY
LEVELING
CAP
UNITS
ADJUSTING NUTS
SET SCREWS
FIGURE 9
9000# JACK
LOWER
ADJUSTING
LOW PROFILE
STANDARD &
UNITS
NUT
UPPER
ADJUSTING
NUT
STOP
A. HYDRAULIC START-UP
1. PRIMING PUMP
4-LEVER:
turn the master switch on. Move any lever on the manual
system to the EXTEND postion. The lever must be moved
to the fullest extent of its travel. This should be done in 3-
second intervals until the pump is primed. This can be de-
termined by a lower pitch sound from the pump. Extend the
two front jacks until they bump the ground, then RETRACT and
Check the system for hydraulic leaks.
Check that the correct jacks are operating as each lever is
operated.
Refill hydraulic tank to within 1" of the top after all jacks have
have been operated.
B. JACK ADJUSTMENTS
Horizontal stop is adjusted by turning the set screws located
just inside the cable locknuts. The jack can be adjusted down
to provide clearance for objects which may interfere with the
operation of the jacks. The horizontal stop must be adjusted to
provide clearance in case the jack extends in the horizontal posi-
tion. The jack must be able to fully extend in the horizontal posi-
tion without interfering with suspension components, tanks,
etc.
Each jack should be checked to be sure that it is vertical when
it swings down. To do this retract all jacks, then extend each
jack until it is close to but not touching the ground. Each jack
it can be adjusted by loosening the lower actuator nut and
tightening the upper actuator nut. (FIGURE 10) If the jack
provide clearance for objects which may interfere with the
operation of the jack (FIGURE 10). The stop must be adjusted
so that the jack can be fully extended in the horizontal pos-
ition without interfering with suspension components or tanks,
etc.
If the jack stopped short of being vertical,
the jack went beyond vertical, loosen the set screw and turn
the adjusting cap counterclockwise. After each counterclock-
wise adjustment, the weight of the coach must be applied to
the jack to make the adjustment effective. Do NOT adjust cap
more than one turn without cycling the jack (FIGURE 11). The
horizontal stop on the heavy-duty jack is adjusted by adding
washers under the urethane stop.
The horizontal stop can be adjusted up or down in the slot to
loosen the set screw and turn the adjusting cap clockwise. If
wire grounded properly to the chassis.
Consult the respective operator’s manuals for specific operat-
ing instruction for the system being installed.
6000# JACK
PART IV
To prime the pump turn the ignition key on, then
NOTE:
1. 6000# JACKS:
2. 9000# JACKS:
3. 16000# JACKS:
- KICK DOWN JACKS ONLY
If the jack stopped short of being vertical
must be adjusted so it can extend in the horizontal position
without interfering with any suspension components, tanks,
etc.
goes past vertical reverse the process.
refill the tank. Care should be taken not to run the pump
out of fluid as it may damage the pump.
Always make the vertical adjustment first.
If the vertical adjustment is changed at any time, be sure
to check the horizontal adjustment. Vertical adjustment is
changed by adjusting the locknuts on the actuator cable.
(FIGURE 9) If the jack stopped short of vertical, tighten the
locknuts off. If the jack goes past vertical, back the lock-
nuts off. Be sure to adjust each nut the same number of
turns.