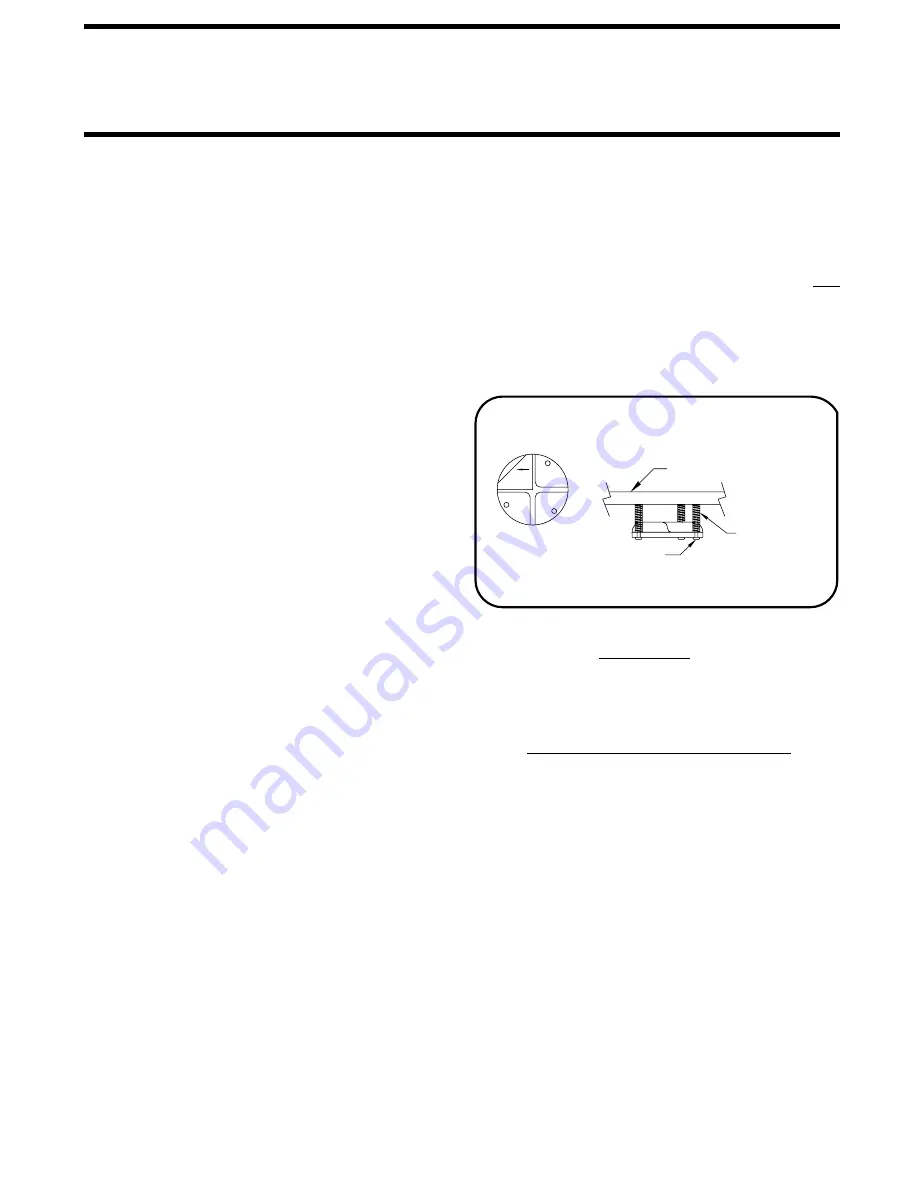
PART III
MI35.2015
25AUG95
5. WIRING: Refer to the appropriate electrical diagram for
wiring. Any wire or cable in the interior of the coach is to be
protected by fusing. All wire insulation should be rated 125
deg. Celsius (257 deg. F). Check applicable RVIA or other
code for detailed fusing and wiring information. Protecting
all wires and cables by fusing is desirable.
A #2 battery cable is supplied with most systems to connect
the pump to the battery or a battery junction post. If a different
cable is used it must be able to carry 200 amperes. If fusing
is required, use a 200 ampere fuse. The fuse should be placed
near the power source. Never connect a fuse directly to the
battery or place it in the battery box where an electrical spark
can cause the battery to explode. If power is taken directly
from the battery, the fuse should be at least 18" from the bat-
tery. A fuse kit is available from HWH Corporation.
Wiring harnesses supplied are usually adequate for most
installations. Harnesses are loomed at the factory. All con-
nections are plug in type except for pump relay which has
ring terminal connections and the power supply for the panel.
That is a field connection made by the installers.
If lengthening or shortening the harness is necessary it is
suggested that all connections be soldered and protected
with shrink tube. If other connection devices are used they
must be sealed to prevent deteriation of the connection.
Grease-filled weather resistant crimp on butt connectors are
available .
Packard Connectors are marked with A & B for wire
connections. This cannot be mixed up. Maintain correct wire
size and color when altering harnesses.
Master Warning Light/Buzzer connections are done by the
installer. Route all wiring away from all heat sources and pro-
tect against sharp edges. Check that jacks can pivot properly
without cutting or stretching wire harnesses or connections.
All grounding connections are supplied by HWH Corporation
and all grounding should be done at the supplied ground stud.
(Refer to PUMP RELAY AND PANEL CONNECTION DIAGRAM).
Coat all exposed electrical connections (battery cable ends,
pump solenoid terminals, grounds, etc.) with a protective
sealant such as Kraylon 1307.
6. THE MASTER WARNING LIGHT/BUZZER:
Warning Light should be used with all systems. A buzzer must
be used with systems using straight acting jacks.The Master
Warning Light should be mounted in the dash in a location
highly visible to the driver. This light will warn the driver if
any of the jacks are down when the ignition is turned to "ON".
Drill a 1/2" hole at the desired location. Be sure to check for
wires or other devices behind the surface before drilling. When
installing the light itself, make sure the ignition is in the "OFF"
position. With the ignition on +12 can be present at the warn-
ing light.
When using a buzzer, the +12 power should come from the
"ON" side of the ignition switch. The power for the panel should
come from the "ACC" side of the ignition switch. (Refer to the
MASTER LIGHT/BUZZER CONNECTION DIAGRAM).
With all wiring complete, the light plate (100 Series System),
or cover plate (110 Series) may now be mounted.
7. MOUNTING THE SENSING UNIT:
can be mounted above or below the surface as long as the
"This Side Up" sticker (FIGURE 8) is facing up and the "Rear"
arrow is pointing to the rear of the coach. The sensing unit
must be mounted to a solid surface that will not flex. Do NOT
mount the sensing unit near any heat-emitting items. Outside
of the frame rails is preferred. The sensing unit must be at
least 12" away from exhaust pipes or other high temperature
components, and must not be in line of sight from these high
temperature components.
A Master
8. FLUIDS: Use Mercon, Multipurpose or Dextron automatic
transmission fluid. DO NOT USE brake fluid or hydraulic
jack fluid. Use of these fluids can damage seals. The hydraulic
tank should be filled to within 1" from the top.
Air Dump - Optional
The air dump feature is used only on coaches with full air bag
suspension, not on coaches with spring suspensions and air
booster bags.
Most coaches have three height control valves; one for the
right rear air bag, one for the left rear air bag, and one for
the front two air bags, OR one for the two rear bags, one for
left front air bag, and one for the right front air bag.
An air dump solenoid valve must be teed into the air line be-
tween each height control valve and the air bag it controls.
(See the Air Line Connection Diagram).
On the 100 and the 110 Series, the air dump signal is on the
yellow wires coming from the control panel. There is one
connection at the front of the vehicle and one at the rear. A
Tee adaptor is supplied with the control system. This will con-
nect two dump valves to one harness connection at the front
or rear of the vehicle. (Refer to Electrical Connection Diagram
With Suspension Air Dump.)
COMPONENT INSTALLATION
NOTE:
The Level Sensing Unit
SURFACE
MOUNTING
BELOW THE SURFACE MOUNTING
SCREWS (3)
REAR
THIS
SIDE
STICKERS
ON TOP
UP
FIGURE 8
LEVEL SENSING UNIT
SPRINGS (3)