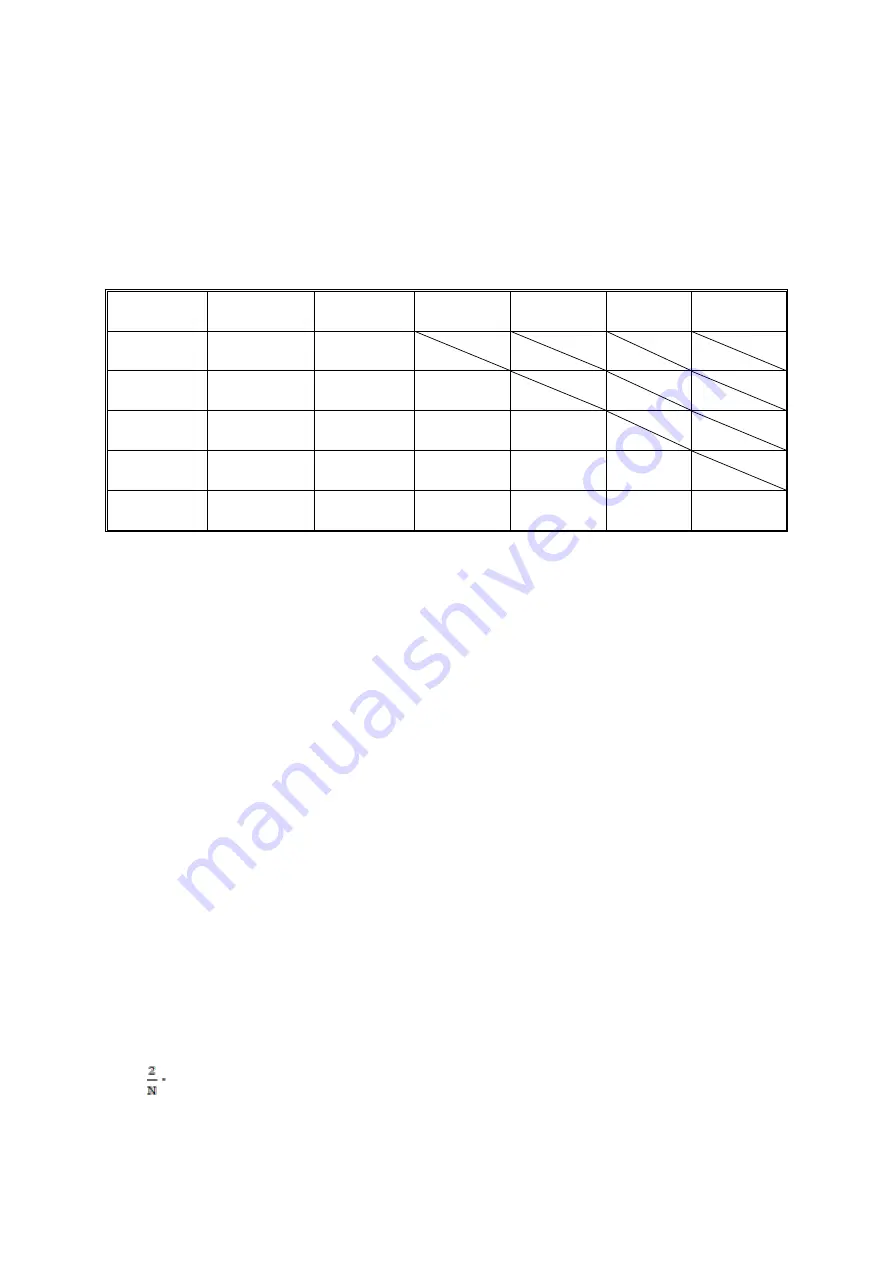
20
(
3
)
Start the machine
7.5
For multi-arc and multi-wire welding machine
Multi-arc welding system should set the current position to avoid the magnetic interruption for each arc, which mean
control the different arc wave shape. the set value as 0°
、
90°
、
180°
、
270°
、
0°
、
90°……which indicate the current wave shape
position, each arc position set separately:
The first arc
Second arc
Third arc
Fourth arc
Fifth arc
Sixth arc
Tandem
0°
90°
Triple arc
0°
90°
180°
Four arc
0°
90°
180°
270°
Five arc
0°
90°
180°
270°
0°
Six arc
0°
90°
180°
270°
0°
90°
No more than 6 arc, adopt the above table to set the arc position, if more than 6 arc, then repeat the setting as 90° to
reduce the interruption.
The procedure for multi-arc welding:
(
1
)
Power off, refer to 6.3 connect the machine
(
2
)
Power on the machine, set the l function of the power source, select the function and set parameter on the panel,
choose the power source characteristics, select AC, DCEP, DCEN. Choose the AC frequency, all power source set the remote
control, wave balance 50
%
and DC deposition 50
%
, finally set the welding current, welding voltage, wire feed speed, wire dia.
And characteristic at the remote control terminal.
(
3
)
Start the machine
7.6
For parallel application
This machine AC rated output is 1200A/44V
(
40
℃,
100
%
duty cycle
)
, if need higher current
,
then can parallel N sets
(
2≤N≤32
)
power source to get N times 1200A
;
DC rated output is 900A/44V
(
40
℃,
100
%
duty cycle
)
, if need higher current
,
then can parallel N sets power source to get N times 900A.
The remote control plug pin 11 and pin 12 output current feedback signal voltage will be change from 1000A/4V to
1000A/
4V.
The procedure for power source parallel: