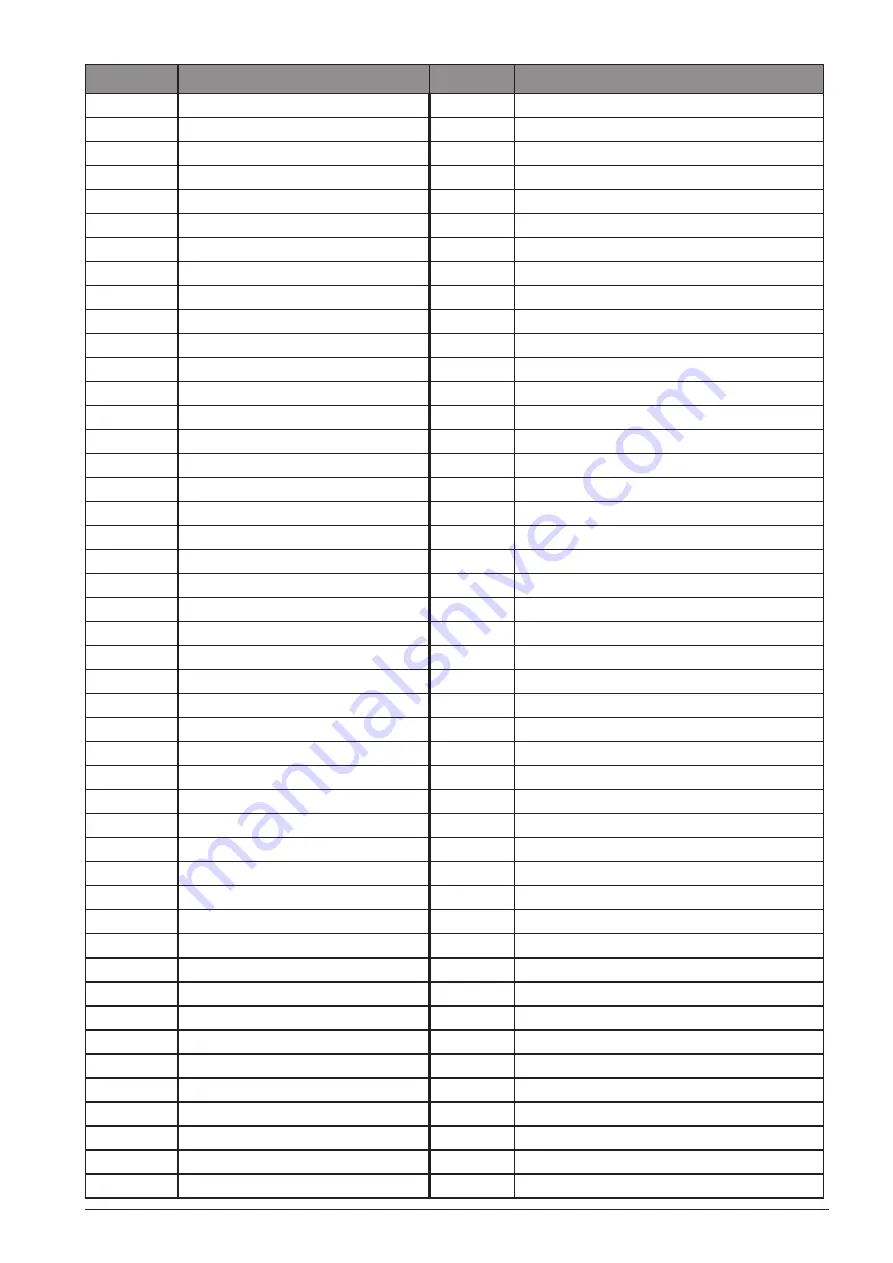
20
CHANGES AND T YPING ERRORS RESERVED
CHANGES AND T YPING ERRORS RESERVED
Number
Description
Number
Description
1
CAP Screw
40
Fixed Block
2
Washer
41
Set Screw
3
Shaft
42
Switch
4
Anchor Blok
43
Handel
5
C-Ring
44
Handel Pipe
5*1
CAP Screw
45
Screw
5*2
CAP Screw
47
Screw
6
Bearing
48
Blade Adjust Stick
7
Left Body Frame
50
Screw
7-1
PIPE connect
52
Blade Cover (Front)
7-2
PIPE connect Body Frame
53
Blade Adjust (Front)
7-3
Right Body Frame
54
Guide
10
Knob
55
Guide Holder
11
Blade Tension Handle
55-1
Guide
12
Big Waswher
56
Screw
13
Lead Screw
60
Eccentric Guide
13-1
Tention gauge
61
Bearing
13-2
Washer
62
Screw
14
Hex, Socket Head Screw
63
CAPScrew
15
Fixed Block
64
Spring Washer
16
CAPSrew
65
Blade Adjustable (Rear)
17
Bushing
65-1
Valve
18
Reducer Block
66
CAPScrew
19
Washer
67
Chip Plate
20
Screw
68
Screw
20*1
Nut
69
Spring Washer
21
Reducer
70
Screw
22
Motor
71
Drive Wheel
25
CAP Screw
72
Washer
27
Key
73
Screw
28
Output shaft
74
CAPScrew
29
Key
74-1
Washer
30
Bearing
74-2
Nut
31
Spring Support
74-3
Cover Switch
31*1
spring holder screw
75
Blade Black Cover
32
Screw
75-1
Blade Left Cover
33
Steel Brush
75-2
Blade Up Cover
33*1
Blade Cover
75-3
Blade Down Cover
33*2
Brush holder
76
Wire Fixed Board
34
Screw
76-1
CAPScrew
34*1
Bearing Cover
78
Saw Blade
35
Spring Washer
79
Idler Wheel
36
Frame Pivot Shaft
80
C-ring
38
Screw
81
Screw
39
Screw
82
Washer
39-1
Copper
83
Wheel
11. e
xPloded
draWInG
and
ParTs
lIsT
Summary of Contents for HU 285 AC-4 TOPLINE
Page 1: ...HU 285 AC 4 TOPLINE BANDSAW MACHINE ...
Page 15: ...15 CHANGES AND TYPING ERRORS RESERVED 9 Electrical diagrams YCM 300 YCM 300 Fig 17 ...
Page 16: ...16 CHANGES AND TYPING ERRORS RESERVED 10 Parts diagram Fig 18 ...
Page 17: ...17 CHANGES AND TYPING ERRORS RESERVED Fig 19 ...
Page 18: ...18 CHANGES AND TYPING ERRORS RESERVED Fig 20 ...
Page 19: ...19 CHANGES AND TYPING ERRORS RESERVED Fig 21 ...
Page 24: ...24 CHANGES AND TYPING ERRORS RESERVED 2017 V1 ...