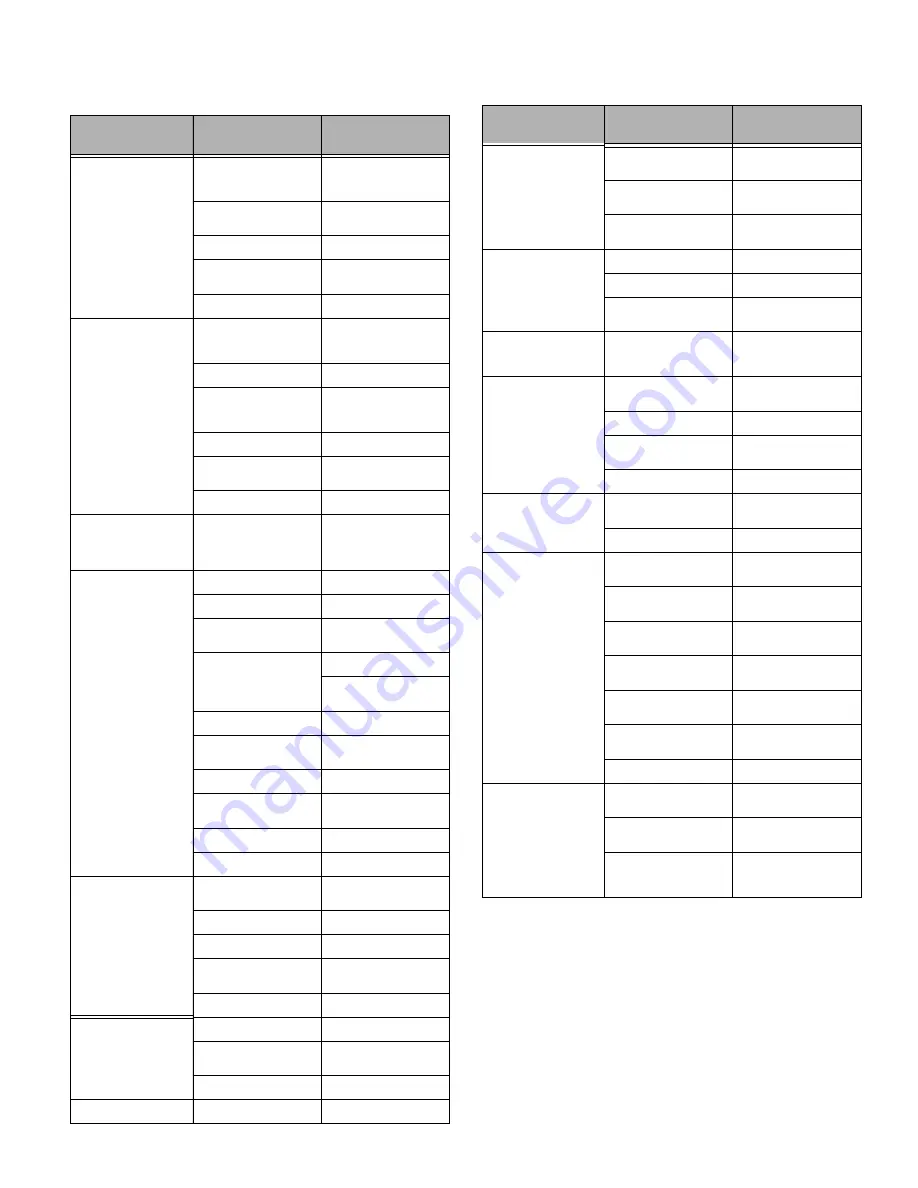
115164
9-1
REV D
TROUBLESHOOTING
SYMPTOMS
PROBABLE CAUSES
SUGGESTED
REMEDIES
Starting motor does not
crank
Steering control levers not
in park brake position or
switch not adjusted
Place steering control
levers in park brake posi-
tion or re-adjust switch
Deck clutch switch
engaged
Disengage clutch switch
Weak or dead battery
Recharge or replace
Electrical connections are
corroded or loose
Check the electrical con-
nections
For additional causes
See engine manual
The engine will not start,
starts hard or fails to
keep running
No fuel or line plugged
Fill tank or replace line
(See Fuel System section
for more details)
Fuel valve is turned off
Open the fuel valve
There is incorrect fuel in
the fuel system
Drain the tank and replace
the fuel with the proper
type
There is dirt in the fuel filter
Replace the fuel filter
Dirt, water or stale fuel in
the fuel system
Contact your dealer
Numerous
See engine manual
Engine:
Runs with continuous
misfiring or engine runs
unevenly or erratically
Numerous
See engine manual
Loss of power or system
will not operate in either
direction
Restrictions in air cleaner
Service air cleaner
Hydraulic line blockage
See your dealer
Internal interference or
leakage in wheel motor
See your dealer
Insufficient hydraulic oil
supply
Check level in reservoir
Have dealer check hydrau-
lic pump
Poor compression
See your dealer
Steering linkage needs
adjustment
Adjust linkage
Tow valve open
Close tow valve
The traction drive belt is
worn, loose or broken
Install a new traction drive
belt
Air in system
Check filter and fittings
For additional causes
See engine manual
Liquid cooled or Diesel
engines overheating:
Temperature light glows
Frequent refilling of radia-
tor required
Coolant appears rusty
Audible alarm
Leaks in system
Replace/tighten hoses and
connections
Coolant level low
Add coolant
Radiator screen clogged
Clean screen
Thermostat stickling or
inoperative
See engine manual
Heat light malfunction
Contact your dealer
Low engine oil pressure
Low oil level
Add oil
Oil diluted or too light
Change oil and check for
source of contamination
Failed oil pump
Contact your dealer
High oil consumption
Numerous
Contact your dealer
Mower jerky when start-
ing or operates in one
direction only
Steering control linkage
needs adjustment
Adjust linkage
Pump or wheel motors
faulty
Contact your dealer
Tow valves not closed
completely
Close tow valves
Hydraulic system oper-
ates hot (oil in reservoir
smells rancid)
Low hydraulic oil level
Fill reservoir
Hydraulic pump faulty
Contact your dealer
Hydraulic oil heat
exchanger clogged
Clean oil heat exchanger
core
Mower creeps when
steering control levers are
in neutral
Steering linkage needs
adjustment
Adjust linkage
Mower circles or veers in
one direction
Steering linkage needs
adjustment
Adjust linkage
Wheel motors faulty
Contact your dealer
Tires improperly inflated
Adjust air pressure to 8 - 12
psi (55 - 83 KPa)
Hydraulic pump faulty
Contact your dealer
Mower creeps when park-
ing brake engaged
Steering linkage out of
adjustment
Adjust steering linkage
Brakes need adjustment
Adjust parking brakes
There is abnormal vibra-
tion
The engine mounting bolts
are loose
Tighten the engine mount-
ing bolts
The engine pulley, idler pul-
ley or blade pulley is loose
Tighten the appropriate
pulley
The engine pulley is dam-
aged
Contact your dealer
The cutting blade(s) is/are
bent or unbalanced
Install new cutting blade(s)
A blade mounting bolt is
loose
Tighten the blade mount-
ing bolt
Spindle bearing is worn or
loose
Replace or tighten spindle
bearing
A blade spindle is bent
Contact your dealer
Blades do not rotate
The deck drive belt is worn,
loose or broken
Install a new deck drive
belt
The deck drive belt is off
the pulley
Install the deck drive belt
and check for a reason
Electric clutch is not
engaging
Check and/or replace 10
amp fuse.
Contact your dealer
SYMPTOMS
PROBABLE CAUSES
SUGGESTED
REMEDIES
Summary of Contents for Super Z Diesel
Page 1: ...115164 REV D Hustler Z Diesel General Service Manual 200 South Ridge Road Hesston Kansas 67062...
Page 6: ...REV D 1 2 115164...
Page 12: ...REV D 3 2 115164...
Page 34: ...REV D 5 8 115164 Figure 5 12 Figure 5 13 Figure 5 14 Figure 5 15...
Page 36: ...REV D 5 10 115164...
Page 52: ...REV D 6 16 115164...
Page 58: ...REV D 7 6 115164...