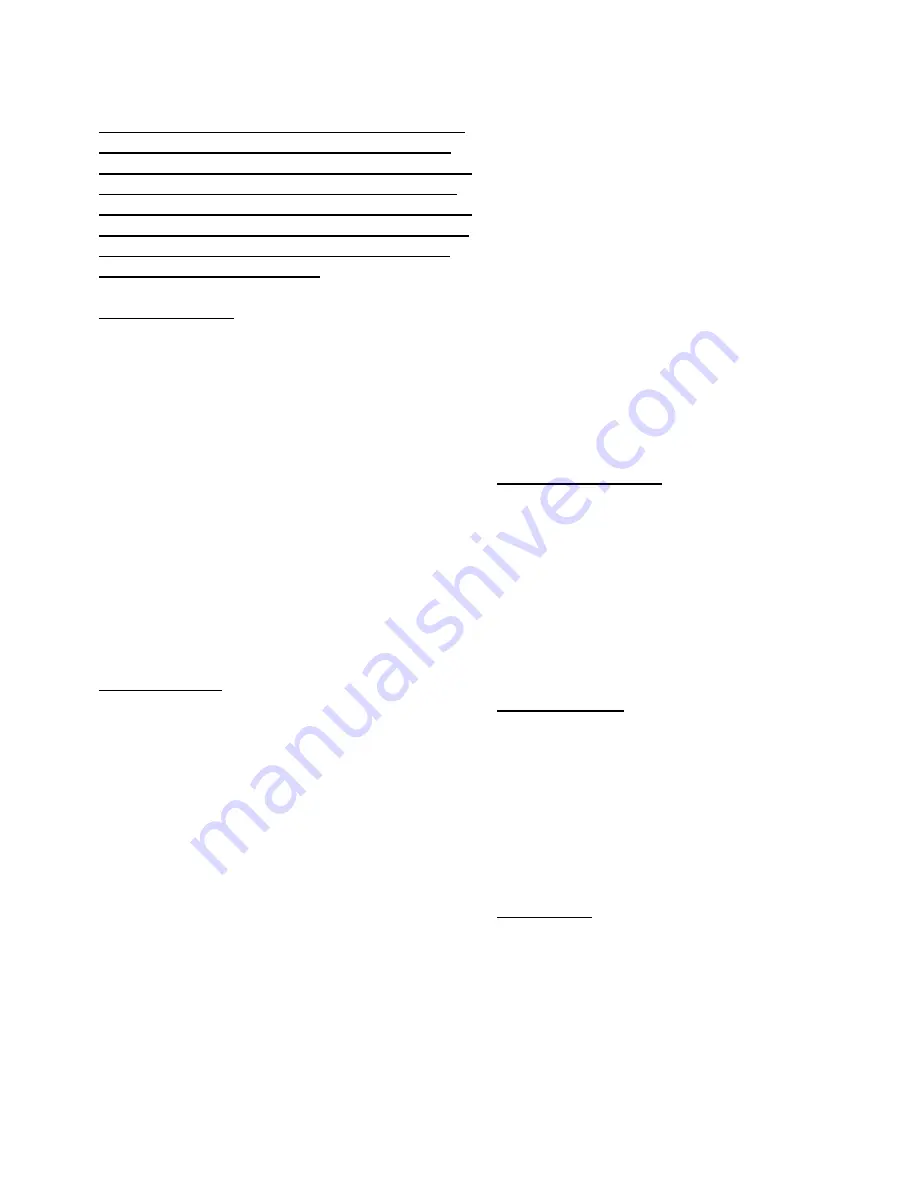
Page 8
Because of the CFC atmospheric considerations
being taken today, we ask that leak testing be
done with refrigerant 22 mixed with nitrogen. If
the condensing unit nameplate designates a re-
frigerant other than R-22, remove all R-22 from
the immediate area to avoid confusion after leak
testing and evacuating the unit. Recharge the
unit with proper refrigerant.
LEAK TESTING –
The test gas cylinder must be equipped
with a pressure gauge and regulator so that sys-
tem test pressures do not exceed maximum allow-
able limits. Do not ever use anything other than a
R-22/Nitrogen mixture for leak testing.
Attach a refrigerant test gas cylinder to
your service manifold and connect the manifold
to the charging port on the liquid line valve.
Charge an R-22/Nitrogen mixture into the sys-
tem, raising the pressure to the unit’s nameplate
for the low side and high side pressures. Using an
electronic detector, carefully check the entire sys-
tem for leaks. Take special care to inspect all
brazed and flare connections.
EVACUATION –
After the system is proven leak tight, thor-
oughly evacuated the system according to the fol-
lowing procedure:
1. Discharge the refrigerant-nitrogen mixture,
allowing it to blow from the system as rapidly
as possible, into an empty cylinder. Be sure
that all service valves and solenoid valves are
open to allow all of the mixture to be dis-
charged.
2. Connect a deep-drain vacuum pump to
both the high and low side of the sys-
tem. Pull a vacuum on the system to at
least 1500 microns.
3. Break the vacuum by adding refriger-
ant into the system until the pressure is
above 0 PSIG. Always charge the re-
frigerant line into the system through a
new drier in the charging manifold line.
A 16 cubic inch drier is sufficient for
this purpose.
4. Repeat steps 2 and 3 two more times,
the third time evacuating the system to
500 microns.
OPERATING DATA –
The following is typical data for
USL models based on lab tests, and may
vary under field operating conditions.
Ambient Temperature
75ºF
Head
Pressure
225
psi
Suction
Pressure
3-5
psi
Discharge
Air
-25ºF
Return
Air
-10ºF
COMPRESSOR –
The compressor is mounted on
springs and banded for shipping purposes
and this band needs to be cut upon installa-
tion. DO NOT LOOSEN THE COM-
PRESSOR MOUNTING BOLTS AS
THESE ARE FACTORY PRE-SET FOR
PROPER RIDING ON THE SPRINGS.
RECEIVER –
The receiver should not be confused
for a filter-drier or muffler. The receiver is
Summary of Contents for USL-2
Page 15: ......