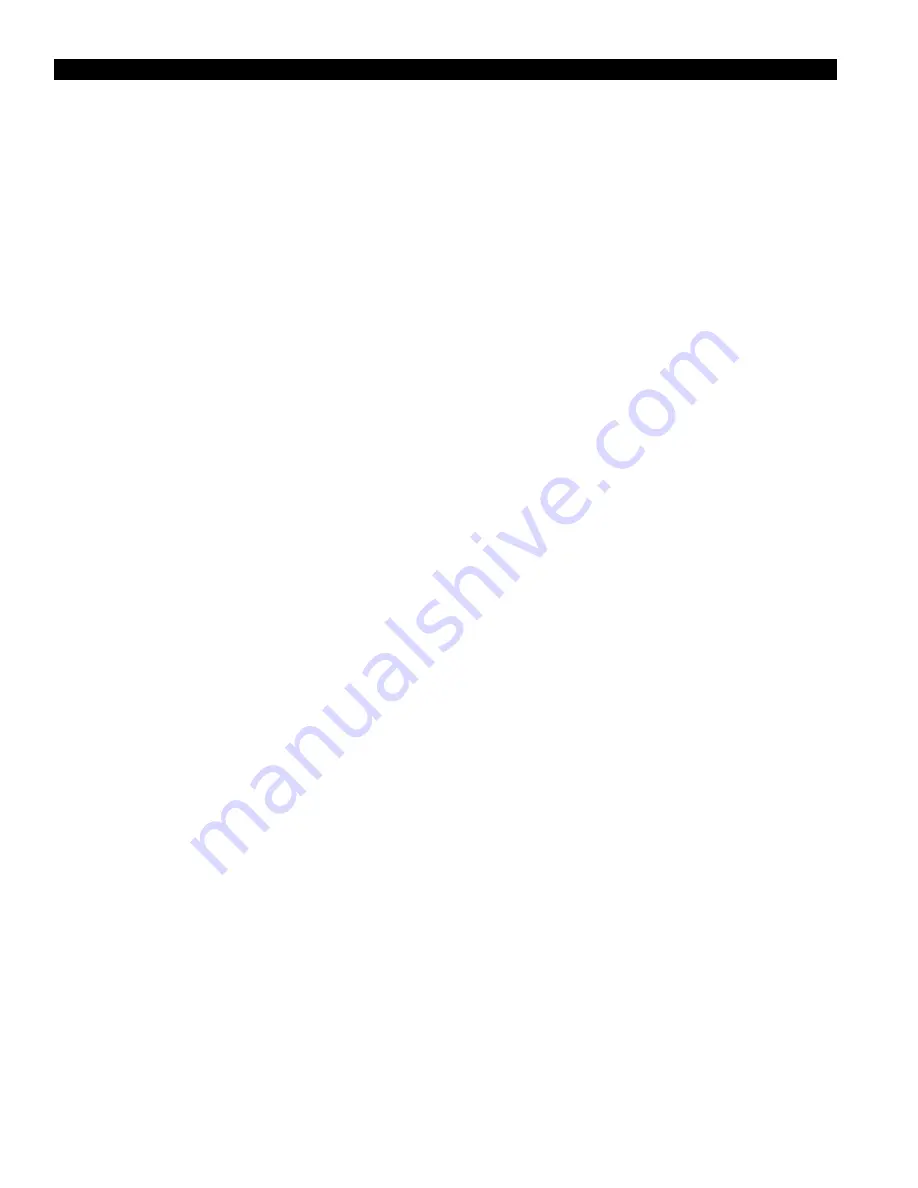
IGHT-ESH/ESHS-0010
44
APPENDIX A. – Temperature Guidelines
1.0 Hot cases are tested to maintain all hot food at 140
°
- 150
°
.
These cases are not designed to heat up or cook food. It is the
user’s responsibility to stock the hot food cases immediately after
the cooking of the food with a pulp temperature of at least 150
°
to 160
°
.
APPENDIX B.– Application Recommendations
1.0 The installer should perform a complete start-up evaluation prior to the
loading of food into the hot food case, which includes such items as:
a) Initial temperature performance, Griddles and Hot Wells.
b) Observation of outside influences such as drafts, radiant heating
from the ceiling and from lamps. Such influence should be
properly corrected or compensated for.
c) Complete start-up procedures should include :
1. Heat / display lamps are lighting
2. Indicator lamps on control panel(s) are working
3. Auto-fill is functioning properly (Service cases)
4. Hot Griddles are functioning.
APPENDIX C. – Field Recommendations
1.0 The most consistent indicator of display hot case performance is
temperature of the product itself.
NOTE
: Public Health will use the temperature of the product in
determining if the hot case will be allowed to display potentially
hazardous food. For the purpose of this evaluation, product
temperature above the FDA Food Code 1995 temperature for
potentially hazardous food will be the first indication that an evaluation
should be performed. It is expected that all hot cases will keep food
at the FDA Food Code 1995 temperature to prevent the sale of
potentially hazardous food.
1.1 The following recommendations are made for the purpose of
arriving at easily taken and understood data which, coupled with
other observations, may be used to determined whether a display
fixture is working as intended:
a) INSTRUMENT – A stainless steel stem-type thermometer is
recommended and it should have a dial a minimum of 1 inch
internal diameter. A test thermometer scaled only in Celsius or
dually scaled in Celsius and Fahrenheit shall be accurate to 1
°
C
(1.8
°
F). Temperature measuring devices that are scaled only in
Fahrenheit shall be accurate to 2
°
F. The thermometer should
be checked for proper calibration. (It should read 32
°
F when
the stem is immersed in an ice water bath).
b) LOCATION – The thermometer must be inserted into the food
itself to acquire proper food pulp temperature.
c) READING – The thermometer reading should be made only
after it has been allowed to stabilize, i.e., maintain a constant
reading.
Loading Product: Cases should be allowed to heat up for one
hour before product is loaded.
Temperature adjustments: Allow 1 hour after adjustment has
been made before testing pulp temperature of product.
d) OTHER OBSERVATIONS – Other observations should be made
which may indicate operating problems, such as unsatisfactory
product, feel/appearance.
APPENDIX D. – Recommendations to user
1.0 Hussmann has instructions and recommendations for proper periodic
cleaning. The user will be responsible for such cleaning, including the
cleaning of equipment within the compartment and the hot area(s).
Cleaning practices, particularly with respect to proper fixture
unloading and warm-up, must be in accordance with applicable
recommendations.
1. Allow the case to preheat for one hour prior to loading.
2. Hot foods should enter the case directly after cooking or no
lower than 150
°
- 160
°
F. The Hot Cases are not designed to
heat up or cook food.
3. Self Service - be sure to display product in single layer in
direct contact with heating surface and/or wire rack.
4.
All griddle type units are designed to maintain temperatures above
the FDA guideline of 140
°
F. This is product temperature, not air or
griddle temperature. Due to the open design of these units, they
must be loaded with product for proper operation. When units are
empty, they experience rapid rise of heated air from air outside the
case. This action gives empty units a false, lower than desired,
temperature reading. Loading the case traps the air at the griddle,
raising temperatures to the 165
°
F to 185
°
F range, keeping product
well above the FDA guidelines. Remember, these units must be
loaded with product to maintain safe product temperature.
5. Check the food pulp temperature frequently with a thermom-
eter to make sure it is at the proper holding temperature. Hot
foods should be at 140
°
. The thermometer must be inserted
into the food itself for the proper temperature.
6. Do not display more food than will be sold within a 4 hour
period.
7. When restocking, bring older food to the front.
8. Clean spills as soon as they happen.
9. Fingerprints and food splatter will drastically shorten bulb life.
Clean splatter off the bulbs immediately with a soft cloth.
When handling bulbs, wear cotton gloves or use a cotton rag /
towel.
10.
When “freshening” foods such as macaroni and cheese with
added water, heat the water in a clean container until it is
10
°
to 20
°
F above the desired holding temperature of the
food. This will keep the food at a safe serving temperature.
Depending on the amount of water, the temperature can drop
10
°
to 20
°
in as little as five minutes.
11. When transferring hot foods in the heated merchandiser to
clean pans, preheat the clean pan. Transferring hot foods to
room temperature pans can cause the temperature of the food
to drop 20
°
or more thus causing food to be at an unsafe
serving temperature.
12. Clean spills as they happen simply by wiping with a cloth. Be
sure to use a dry cloth on very hot surfaces to prevent steam
burns.
APPENDICES