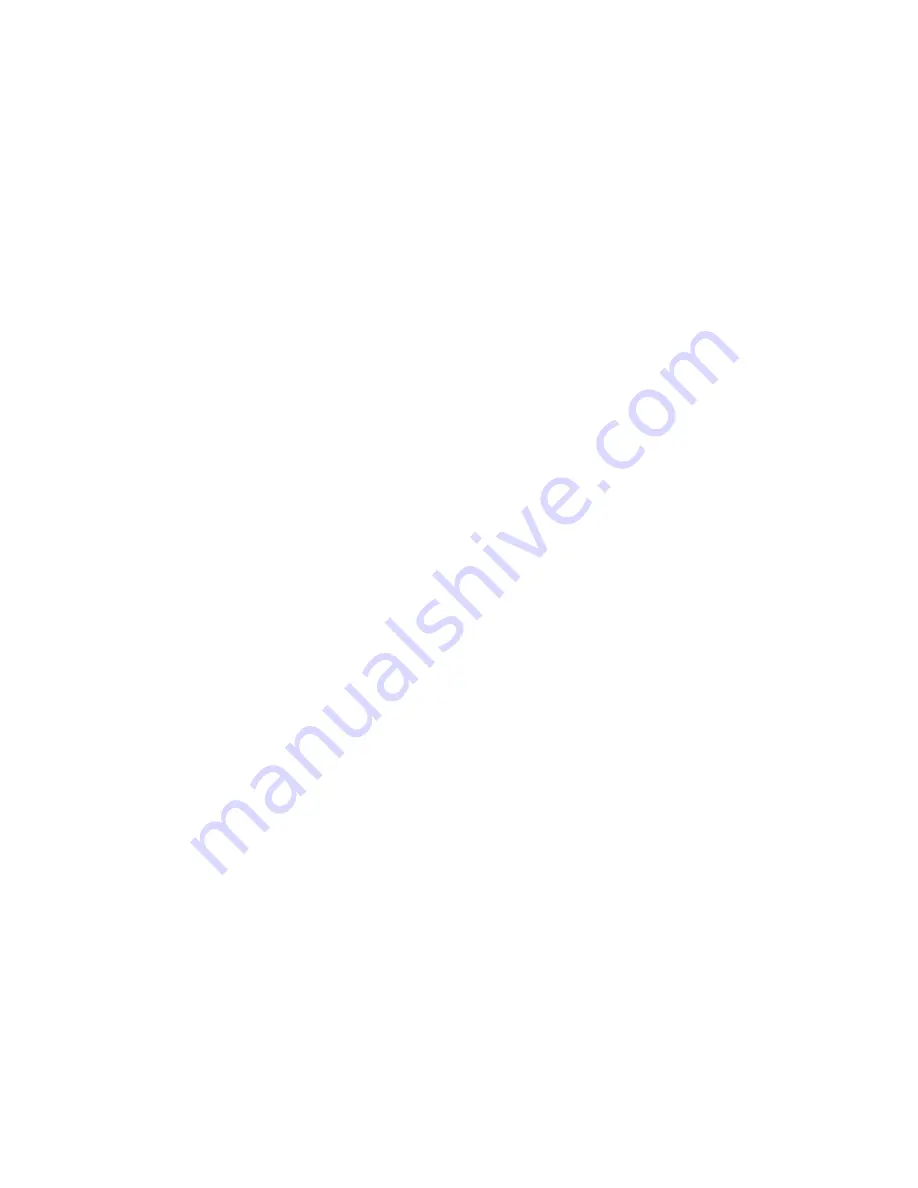
IGSV-ASCS-0303
36
dually scaled in Celsius and Fahrenheit shall be accurate to 1°C
(1.8°F). Temperature measuring devices that are scaled only in
Fahrenheit shall be accurate to 2°F. The thermometer should be
checked for proper calibration. (It should read 32°F when the stem
is immersed in an ice water bath).
b) LOCATION – The probe or sensing element of the thermometer
should be located in the airstream where the air first enters the
display or storage area, and not more than 1 inch away from the
surface and in the center of the discharge opening.
c) READING – It should first be determined that the refrigerator is
refrigerating and has operated at least one hour since the end of
the last defrost period. The thermometer reading should be made
only after it has been allowed to stabilize, i.e., maintain a constant
reading.
d) OTHER OBSERVATIONS – Other observations should be made which
may indicate operating problems, such as unsatisfactory product,
feel/appearance.
e) CONCLUSIONS – In the absence of any apparent undesirable
conditions, the refrigerator should be judged to be operating
properly. If it is determined that such condition is undesirable, i.e.,
the product is above proper temperature, checks should be made
for the following:
1. Has the refrigerator been loaded with warm
product?
2. Is the product loaded beyond the “Safe Load Line”
markers?
3. Are the return air ducts blocked?
4. Are the entering air ducts blocked?
5. Is a dumped display causing turbulent air flow and
mixing with room air?
6. Are spotlights or other high intensity lighting
directed onto the product?
7. Are there unusual draft conditions (from heating /
air-conditioning ducts, open doors, etc.)?
8. Is there exposure to direct sunlight?
9. Are display signs blocking or diverting airflow?
10. Are the coils of the refrigerator iced up?
11. Is the store ambient over 75°F, 55% RH as set forth
in ASHRAE Standard 72 and ASHRAE Standard 117?
12. Are the shelf positions, number, and size other than
recommended by Hussmann?
13. Is there an improper application or control system?
14. Is the evaporator fan motor/blade inoperative?
15. Is the defrost time excessive?
16. Is the defrost termination, thermostat (if used) set
too high?
17. Are the refrigerant controls incorrectly adjusted?
18. Is the air entering the condenser above design
conditions? Are the condenser fins clear of dirt, dust,
etc.?
19. Is there a shortage of refrigerant?
20. Has the equipment been modified to use
replacements for CFC-12, CFC-502 or other
refrigerant? If so, have the modifications been made in
accordance with the recommendations of Hussmann
equipment? Is the refrigerator charged with the
proper refrigerant and lubricant? Does the system use
the recommended compressor?
APPENDIX D. – Recommendations to user -
Refrigerated
1.0 Hussmann should provide instructions and recommendations for proper
periodic cleaning. The user will be responsible for such cleaning, including
the cleaning of low temperature equipment within the compartment and
the cooling coil area(s). Cleaning practices, particularly with respect to
proper refrigerator unloading and warm-up, must be in accordance with
applicable recommendations.
1.1 Cleaning of non frozen food equipment should include a weekly cleaning
of the food compartment as a minimum to prevent bacteria growth from
accumulating. Actual use and products may dictate more frequent cleaning.
Circumstances of use and equipment design must also dictate the frequency
of cleaning the display areas. Weekly washing down of the storage
compartment is also recommended, especially for equipment subject to
drippage of milk or other liquids, or the collection of vegetable, meat,
crumbs, etc. or other debris or litter. Daily cleaning of the external areas
surrounding the storage or display compartments with detergent and water
will keep the equipment presentable and prevent grime buildup.
1.2 Load levels as defined by Hussmann must be observed.
1.3 The best preservation is achieved by following these rules:
a) Buy quality products.
b) Receive perishables from transit equipment at the ideal temperature
for the particular product.
c) Expedite perishables to the store’s storage equipment to avoid
unnecessary warm-up and prolonged temperature recovery. Food
store refrigerators are not food chillers nor can they reclaim quality
lost through previous mishandling.
d) Care must be taken when cross merchandising products to ensure
that potentially hazardous vegetable products are not placed in non
refrigerated areas.
e) Display and storage equipment doors should be kept closed during
periods of inactivity.
f) Minimize the transfer time of perishables from storage to display.
g) Keep meat under refrigeration in meat cutting and processing area
except for the few moments it is being handled in processing. When
a cut or tray of meat is not to be worked on immediately, the
procedure should call for returning it to refrigeration.
h) Keep tools clean and sanitized. Since mechanical equipment is used
for fresh meat processing, all such equipment should be cleaned at
Summary of Contents for ASCS
Page 38: ...IGSV ASCS 0303 38...