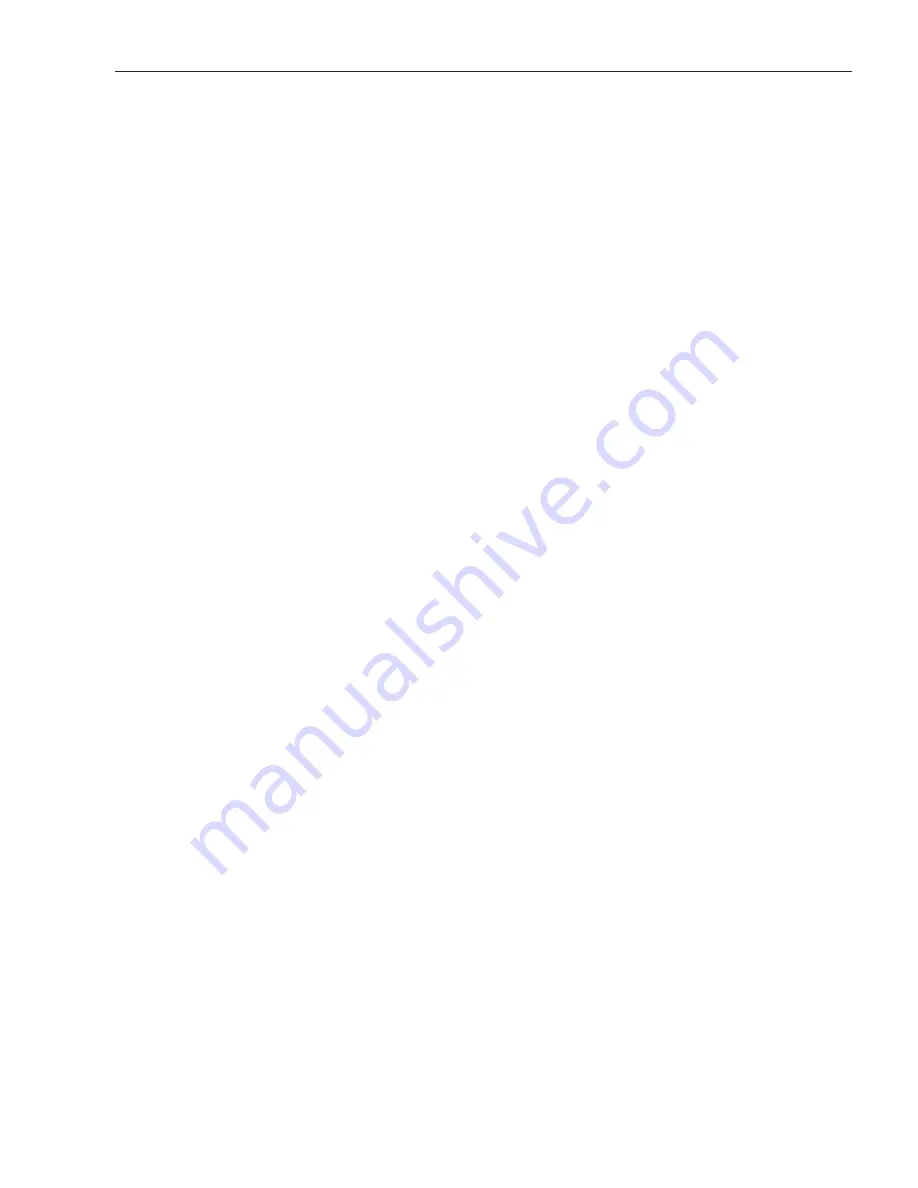
27
1.1 The following recommendations are made
for the purpose of arriving at easily taken and
understood data which, coupled with other
observations, may be used to determine whether
a display refrigerator is working as intended:
a) INSTRUMENT - A stainless steel stem-type
thermometer is recommended and it should
have a dial a minimum of 1 inch internal
diameter. A test thermometer scaled only
in Celsius or dually scaled in Celsius and
Fahrenheit shall be accurate to 1°C (1.8°F).
Temperature measuring devices that are
scaled only in Fahrenheit shall be accurate to
2°F. The thermometer should be checked for
proper calibration. (It should read 32°F when
the stem is immersed in an ice water bath).
b) LOCATION - The probe or sensing element
of the thermometer should be located in
the airstream where the air fi rst enters the
display or storage area, and not more than
1 inch away from the surface and in the
center of the discharge opening.
c) READING - It should fi rst be determined
that the refrigerator is refrigerating and has
operated at least one hour since the end
of the last defrost period. The thermometer
reading should be made only after it has
been allowed to stabilize, i.e., maintain a
constant reading.
d) OTHER OBSERVATIONS - Other
observations should be made which may
indicate operating problems, such as
unsatisfactory product, feel/appearance.
e) CONCLUSIONS - In the absence of any
apparent undesirable conditions, the
refrigerator should be judged to be operating
properly. If it is determined that such
condition is undesirable, i.e., the product is
above proper temperature, checks should be
made for the following:
1. Has the refrigerator been loaded with
warm product?
2. Is the product loaded beyond the “Safe
Load Line” markers?
3. Are the return air ducts blocked?
4. Are the entering air ducts blocked?
5. Is a dumped display causing turbulent air
fl ow and mixing with room air?
6. Are spotlights or other high intensity
lighting directed onto the product?
7. Are there unusual draft conditions (from
heating/air-conditioning ducts, open
doors, etc.)?
8. Is there exposure to direct sunlight?
9. Are display signs blocking or diverting
airfl ow?
10. Are the coils of the refrigerator iced up?
11. Is the store ambient over 75°F, 55% RH
as set forth in ASHRAE Standard 72 and
ASHRAE Standard 117?
12. Are the shelf positions, number, and size
other than recommended by Hussmann?
13. Is there an improper application or control
system?
14. Is the evaporator fan motor/blade
inoperative?
15. Is the defrost time excessive?
16. Is the defrost termination, thermostat (if
used) set too high?
17. Are the refrigerant controls incorrectly
adjusted?
18. Is the air entering the condenser above
design conditions? Are the condenser fi ns
clear of dirt, dust, etc.?
19. Is there a shortage of refrigerant?
20. Has the equipment been modifi ed
to use replacements for CFC-12,
CFC-502 or other refrigerant? If so,
have the modifi cations been made in
accordance with the recommendations
of the equipment manufacturer? Is the
refrigerator charged with the proper
refrigerant and lubricant? Does the system
use the recommended compressor?
Appendix D. - Recommendations to User
1.0 Hussmann Corporation provides instructions
and recommendations for proper periodic
cleaning. The user will be responsible for
such cleaning, including the cleaning of low
temperature equipment within the compartment
and the cooling coil area(s). Cleaning practices,
particularly with respect to proper refrigerator
unloading and warm-up, must be in accordance
with applicable recommendations.
Appendices (Cont'd)
Summary of Contents for CR3HV-F
Page 3: ...3 Cut and Plan Views...