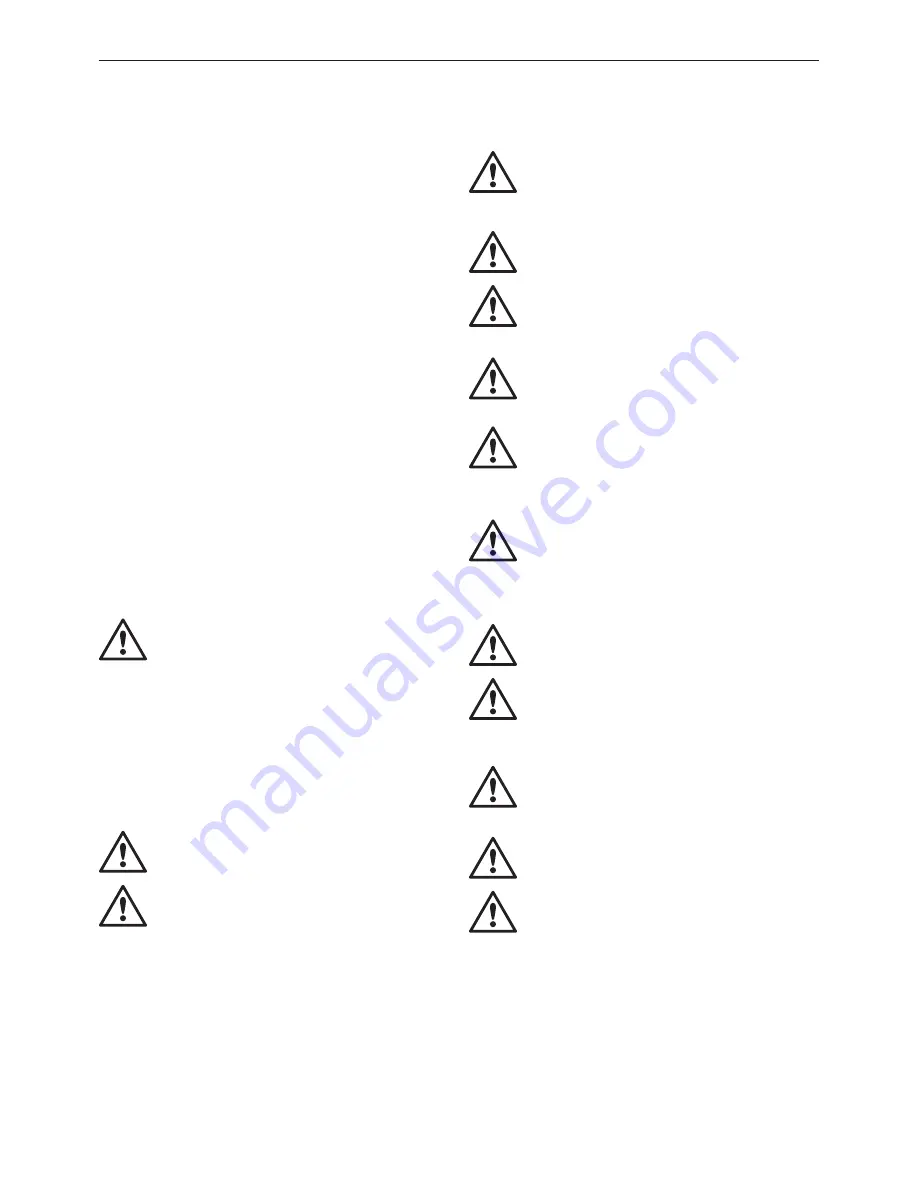
English – 3
1 Introduction and safety regulations
1.1 General
This workshop manual gives a full description of how to
do troubleshooting, repair and test of the high pressure
washer. It also gives safety instructions that the
personnel must obey during repair work.
1.2 Revisions
If there are changes to the product, these are gradually
introduced into ongoing production. These changes can
have an effect on servicing and/or spare parts. This can
cause sections of the workshop manual to become out of
date. Servicing information is sent out for each change.
To make sure that the repair and servicing instructions
are complete and up to date, always read the workshop
manual together with all servicing information applicable
for the high pressure washer.
1.3 Target group
This workshop manual is written for personnel with a
general knowledge of how to repair and do servicing on
high pressure washers.
All personnel that repair or do servicing on the high
pressure washer must read and understand the
workshop manual.
1.4 Safety instructions
WARNING: All personnel that repair or do
servicing on the high pressure washer
must read and understand the safety
instructions.
1.4.1 General safety instructions
The service center that repairs the high pressure washer
must have safety devices that comply with local
regulations.
Warnings and cautions are used to point out specially
important parts of the workshop manual.
WARNING: Used if there is a risk of injury
or death if the instructions are not followed.
CAUTION: Used if there is a risk of material
damage if the instructions are not followed.
Note: This information makes the product easier to
use.
1.4.2 Special safety instructions
WARNING: Do not use accessories and/or
do changes that are not approved by the
manufacturer. This can cause injury or
death to the operator or other persons.
WARNING: Always use original spare parts
and accessories.
WARNING: Disconnect from electrical
power supply before carrying out user
maintenance.
WARNING: Use approved hearing protec-
tion. Noise from the product can result in
permanent hearing loss.
WARNING: High pressure jets can be
dangerous. Never direct the water jet at
persons pets, live electrical equipment or
the machine.
WARNING: The operator and anyone in the
immediate vicinity of the site of cleaning
should take action to protect themselves
from being struck by debris dislodged
during operation. Wear goggles during
operation.
WARNING: Never try to clean clothes or
footwear on yourself or other persons.
WARNING: Never use the machine in an
environment where there could be a danger
of explosion. If any doubt arises, contact
the local authorities..
WARNING: It is not allowed to clean asbes-
tos- containing surfaces with high pres-
sure.
WARNING: This high pressure washer must
not be used at temperatures below 0°C.
WARNING: Never let any persons stay
under the product when stored on the wall.
Introduction and safety regulations