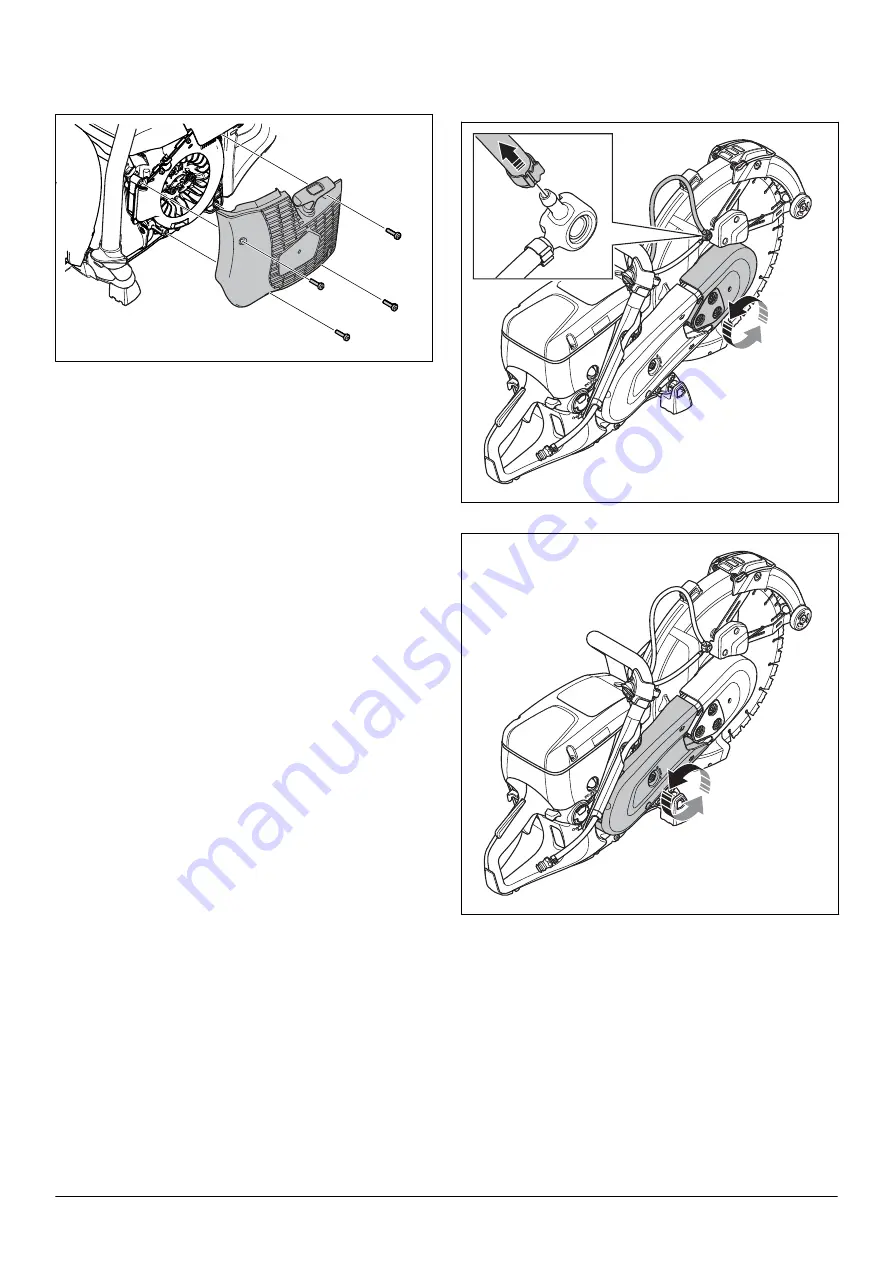
5.2.1 To remove the starter
1. Loosen the 4 screws on the guard.
2. Remove the starter.
5.2.2 To remove the cutting head
1. Loosen the hose clip. Refer to
wet system on page 66. Loosen the 3 nuts on the
front belt guard.
2. Loosen the belt tension with the adjuster screw.
1453 - 001 - 02.04.2020
Product overview for repair and
servicing - 15
Summary of Contents for K770 SmartGuard
Page 1: ...Workshop manual K770 SmartGuard English 1453 001 02 04 2020 ...
Page 6: ...3 2 Tightening torques 3 5 4 6 4 6 4 6 2 0 7 9 3 5 4 6 6 Servicing data 1453 001 02 04 2020 ...
Page 7: ...11 12 10 12 5 7 11 13 11 13 11 13 7 9 17 23 1453 001 02 04 2020 Servicing data 7 ...
Page 9: ...13 6 8 20 25 5 5 6 10 12 6 6 4 3 5 7 5 6 8 25 30 9 11 1453 001 02 04 2020 Servicing data 9 ...
Page 74: ...74 Wiring diagram 1453 001 02 04 2020 ...
Page 75: ...1453 001 02 04 2020 Wiring diagram 75 ...
Page 76: ...114237727 2020 04 02 ...