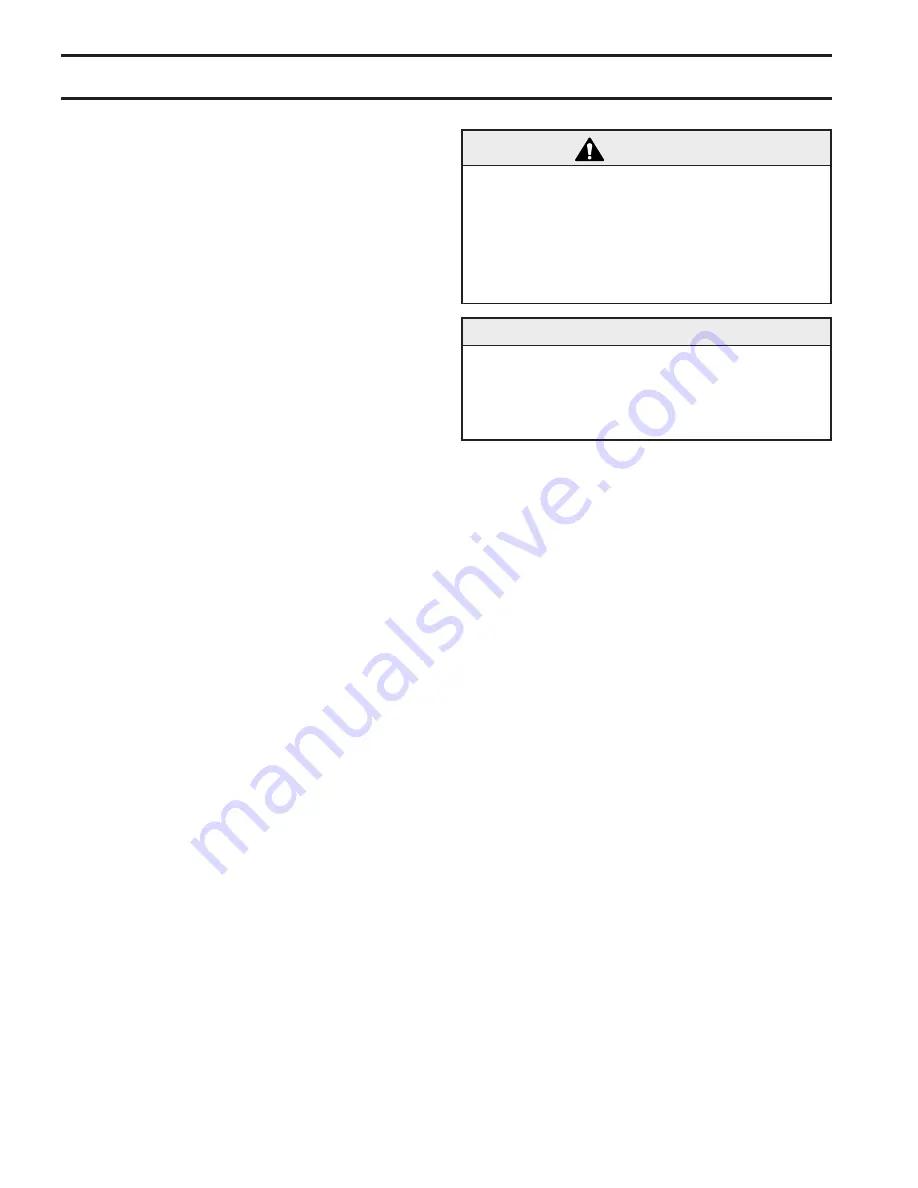
TROUBLE SHOOTING
DIAMOND CORE DRILLING VARIABLES:
Below are some factors that influence diamond core
performance.
• Amount of Water.
• Rigidity of drill rig.
• Drill Motor Speed (RPM).
• Feed Pressure Applied to Bit.
• Amount of Steel in the Material.
• Amount and size in exposed steel.
• Age of Concrete.
• Size and Type of Aggregate in Material.
• Type of Sand (Manufactured or River) in Material.
• Bit Run out.
DIAMOND CORE BIT BINDING & GLAZING:
Diamond Core Bit Binding is caused by a dull (glazed)
bit, or a poorly stabilized drill rig.
Causes of Diamond Core Bit Glazing:
• Wrong RPM for Bit Diameter.
• Excessive or Low Feed Pressure.
• High Steel Content or Large Hard Aggregate in
Work Surface Material.
• Excessive Water.
• Low Motor Power.
SHARPENING DIAMOND CORE BITS:
To work properly, diamond core drill bits must main-
tain diamond exposure. An erosion of the tools dia-
mond segment must occur to allow the bit to continue
operation. When the “erosion” of the diamond segment
is altered, the diamond bit can become dull or “glazed”.
Glazing is noticeable when the bit feed rate slows dra-
matically, or the bit will not “cut” (actually “grind”). Stop
the machine and examine the diamond segments on
the bit. If the diamonds are flush with metal, they are
underexposed, or “glazed”. To correct the glazing:
1. Reduce water flow until it becomes “muddy” in
appearance. Continue reduced water flow until
feed rate can be increased.
2. If the diamond core bit segments do not “open
up” (diamonds become exposed), remove bit from
hole and add a thick layer (1/4” or 6mm) of silica
sand (coarser is better) to bottom of hole.
3. Resume drilling for 3 to 5 minutes with reduced
water flow and at a lower RPM if possible.
4. Gradually increase water flow to flush sand from
the hole.
5. Repeat steps 1 to 4 if required.
NOTICE
Removing cores with diameters greater than
twice their length can be difficult. The core may
have to be broken into smaller pieces and then
removed. Electric hammers and chisels are ideal
for breaking cores.
WARNING!
When coring through floors, cores may drop from
bit. Provide proper protection for people / prop
-
erty below the coring area.
ALWAYS check work area for hidden hazards
before operation! Hidden hazards may include
buried electrical , gas, sewer, or water lines below
or inside the work surface.
RETRIEVING CORES & DEEP DRILLING:
When coring holes that are longer than the diamond
core drill bit, follow the steps below:
• Begin coring the hole as usual. When you have
cored the length of the bit, raise the bit out of the
cored hole and stop the motor.
• Remove the core. A chisel, wedge or similar device
can be placed between the core and work surface.
Use this tool to break the core from the bottom of
the hole.
• Use tongs, bent wire, anchor bolts or similar device
to remove core from hole.
Summary of Contents for DS 700
Page 24: ...24 2007 32 504 80 58 01 ...