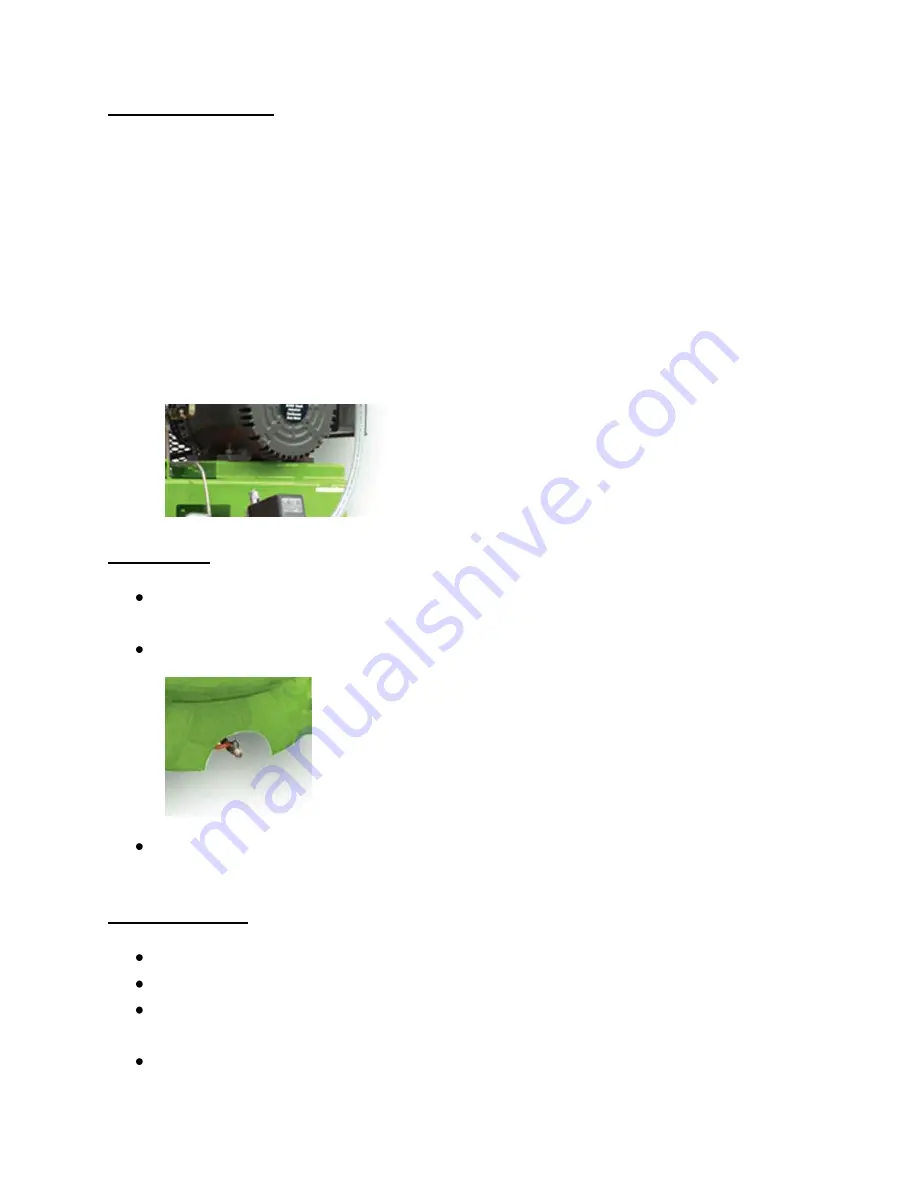
5HP 80 gallon 1 Stage Single Phase 3 Cylinder Air Compressor –HP05V080Y1
7/18/2011
6
BELT ADJUSTMENT
Always pull the motor disconnect switch before working on the belts so the motor cannot
start up unexpectedly.
When belt tension is adjusted properly, the belts can be depressed at a
point midway between the motor pulley and the flywheel approximately one half inch. Loose
belts will slip on the motor pulley and cause excessive heating and wear. A belt that is too tight
will overload the bearings. Adjustments can be made by sliding the motor along its base. When
installing new belts, it is necessary that the motor bolts be loosened and the motor moved
toward the compressor. The new belts can be installed without damage or strain. Overtime
belts stretch and it is recommended that all belts be changed at the same time. To adjust the
belts loosen the four motor frame nuts and adjust the single bolt head on the belt tensioner. (
Fig.1)
Fig. 1
DAILY CARE
Check oil level in crankcase and, if necessary, add sufficient oil to bring to (but not
above) halfway level in the sight glass (without the motor running).
Drain moisture from air receiver.
Stop, look, and listen for unusual noises, failure to compress, overheating, vibration, or
belt slippage. Correct before damage occurs.
MONTHLY CARE
Check and tighten all bolts as required.
Check air connections and joints for air leaks.
Check all unloading lines for air leaks. Air leaks in the unloading lines will cause the
unloaders to chatter and could cause short cycling.
Check “V” belts for any possible misalignment and tightness. See “Belt Adjustment”.