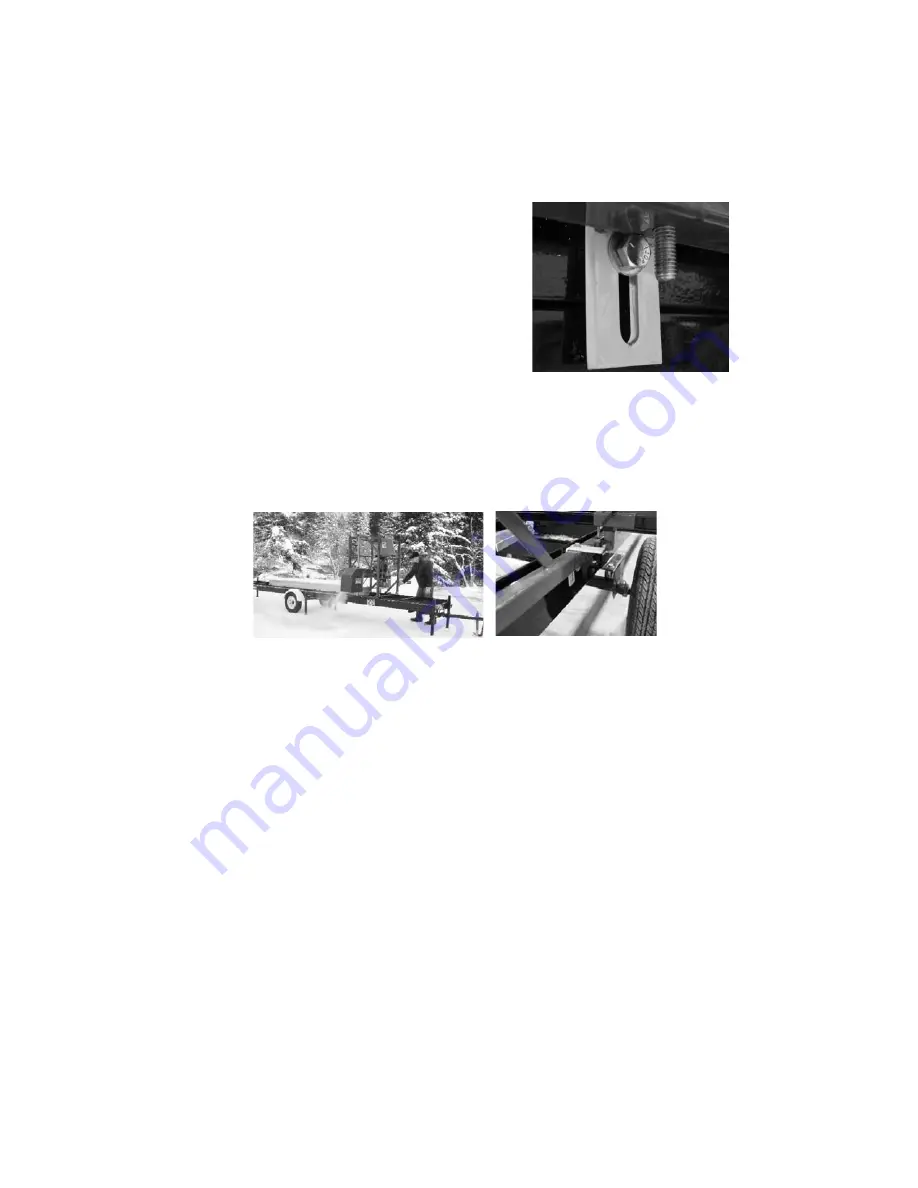
Correct
trailer set
up. All legs
are level;
head should
not move on
its own.
Mill Head is
locked into
place with
brackets.
Head will not
move during
transport.
10
Before operating the Hud-Son Saw Mill
the following procedures need to be performed:
When installing travel brackets line up
holes, put track side bolt in first, snug
up, then put the bolt into the mill frame
hole, on both sides. Then tighten bolts
securely. (see fig G)
1 -
Put tow hitch back in tow position, tighten bolt and
safety pin, remove jack from center of trailer, put it
back on tow hitch. Lock Mill head into travel
position.
2 - Raise rear legs and lock in upright position.
3 - Raise front legs and lock in raised position.
4 - Raise jack to desired height, hook hitch to vehicle.
Remove pin and rotate to horizontal position. Plug
in lights and brakes. Hook-up safety chains and
break-away switch. (If applicable)
5 - Lift front legs and lock in transport position.
6 - Be sure to clean unit of all loose debris,
including all bark, sawdust and dirt.
Transport Instructions
Follow all the steps to safely transport the
Hud-Son Saw Mill Trailer Model
1 - Check oil and fuel levels
2 - Check blade lubrication and
hydraulic levels (if applicable)
FOR BLADE LUBE USE:
Summer
Months use tap water and to prevent pitch
build up on the blade, add 1 oz. of dish soap
or pine sol to 1 gallon of tap water. This will
help keep the blade clean and cooler.
In the Winter Months Use regular wind-
shield washer fluid (usually blue in color) To
prevent pitch build up on the blade add 1 oz.
of dish soap or pinesol.
Adjustment: Before starting the engine,
adjust the flow of lube to the blade by adjust-
ing the flow valve closest to the tank so there
is a constant drip. If more lube is necessary,
adjust the valve until the there is a constant
drip. If more lube is needed, continue to adjust
the valve until the desired flow is acquired.
3 - Be sure the blade is sharp and tight
4 - Be sure all levers and switches are in
the neutral/center position before
starting the engine (if applicable)
5 - Be sure all persons are clear of the
equipment
6 - Make sure the unit is level and stable.
Do not use: petroleum products,
petroleum based products, flammable
products, or vegetable oil based
product. The above products mixed
with water or straight will cause the
blade to come off, fluid will be too
slippery between the blade and wheel
belting causing the blade to come off.