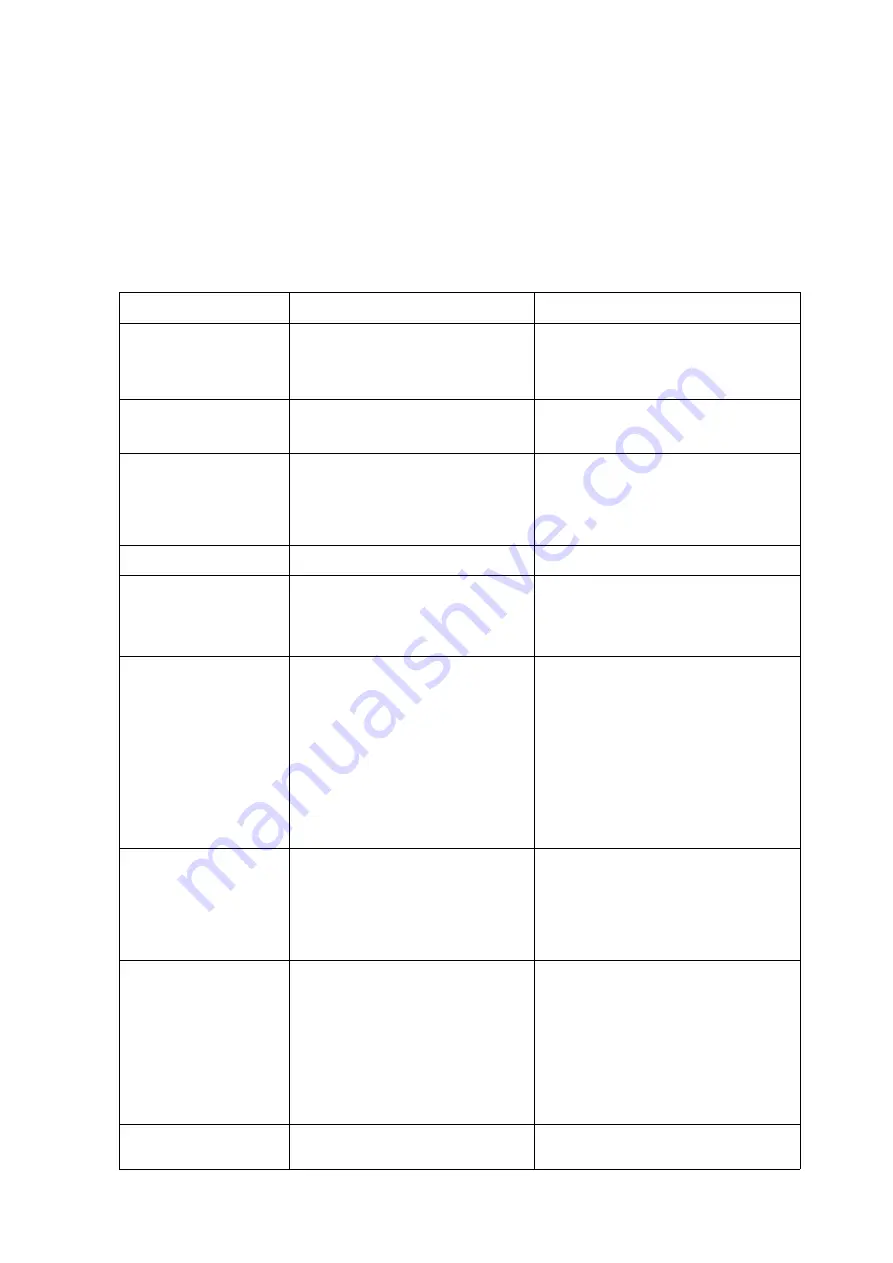
20
9, Common faults and eliminating methods
If there some problems that can not be judged or solved, please do not hesitate to
contact our company to get some technical assistance. Please do not repair or open the
machine arbitrarily. There is high voltage after cutting power for 10 minutes, only qualified
electrician can operate!
Common faults and eliminating methods: (see below sheet)
Table 9 Common faults and eliminating methods
Faults
Reasons
Eliminating methods
1
.
Put power on, the power
indicator do not light,
digital display meter don't
work
1.Open phase of three phase power;
2.The power switch is old and damaged;
3.The 1.5A fuse of power control is melt;
1.Check the three phase power switch;
2.Replace power switch;
3.Replace the fuse;
2
.
Welding machine do not
work, under
1
.
Open phase on three phase power;
2
.
Under voltage on three phase power;
Check three phase supply power, make sure
supply voltage fit the required voltage;
3
.
Welding machine do not
work, the over-heating
indicator lights
1.The environment temperature is too
high;
2.There is something wrong with the
cooling fan;
3.The temperature relay is damaged;
1.Make welding machine rest for a moment;
2.Check the power of cooling fan or replace
cooling fan;
3.Replace the temperature relay;
Faults
Reasons
Eliminating methods
4. There is wire feeding, but
no current spark, or there is
noise in machine
1.The fast recovery diode is damaged;
2.IGBT is damaged;
3.Circuit or other components are
damaged;
1.Check and replace the damaged fast
recovery diode;
2.Replace IGBT or PCB;
3.Check and replace the damaged parts;
5
.
Press torch switch, wire
wheel moves, but there is
no wire sending out from
torch, or the wire feeding is
unstable
1.The wire wheel is not tighten;
2.The diameter of wire slot is not same as
electrode wire;
3.The contact tip is blocked by spatter;
4.The wire reel slog is abraded;
5.The wire feeding pipe of torch is
blocked;
6.The torch cable is excessive bended;
1.Fasten the wire wheel;
2.Replace wire slot;
3.Eliminate the spatter on contact tip;
4.Replace wire feeding wheel;
5.Clean the dirty or dust in wire feeding pipe
by dry compressed air or replace it with a
new one;
6.Make the bending diameter of torch cable
larger than 300mm;
6
.
Press torch switch, the
wire feeding wheel do not
move or there is no no-load
voltage
1
.
Control cable of wire feeder is
damaged;
2
.
Open circuit on control cable of
welding torch switch;
3
.
The PCB is damaged;
4. The wire feeding motor is damaged;
1
.
Check the control cable;
2
.
Repair the wire feeding motor or replace it
with a new one;
3
.
4. Repair or replace motor;
5. Repair or replace PCB;
7
.
There are too many air
holes on welding seam;
1.CO
2
gas is not pure;
2.The gas flow is not enough;
3.There is grease dirt or rust on welding
seam;
4.The wind in the welding place is too
heavy;
5.CO
2
gas circuit is blocked or blab;
6.Gas valve doen`t actuate;
7.Deformation on nozzle;
1.Use high purity CO
2
gas;
2.Adjust the gas flow;
3.Eliminate the grease dirt or rust on welding
seam;
4.Do something to reduce the wind in
welding place;
5.Check the gas circuit, dredge it or block it;
6.Replace the nozzle of welding torch;
8. Current and voltage can
not be adjusted
1.The potentiometer of current and
voltage is damaged;
1.Replace potentiometer;
2.Repair or replace the PCB;