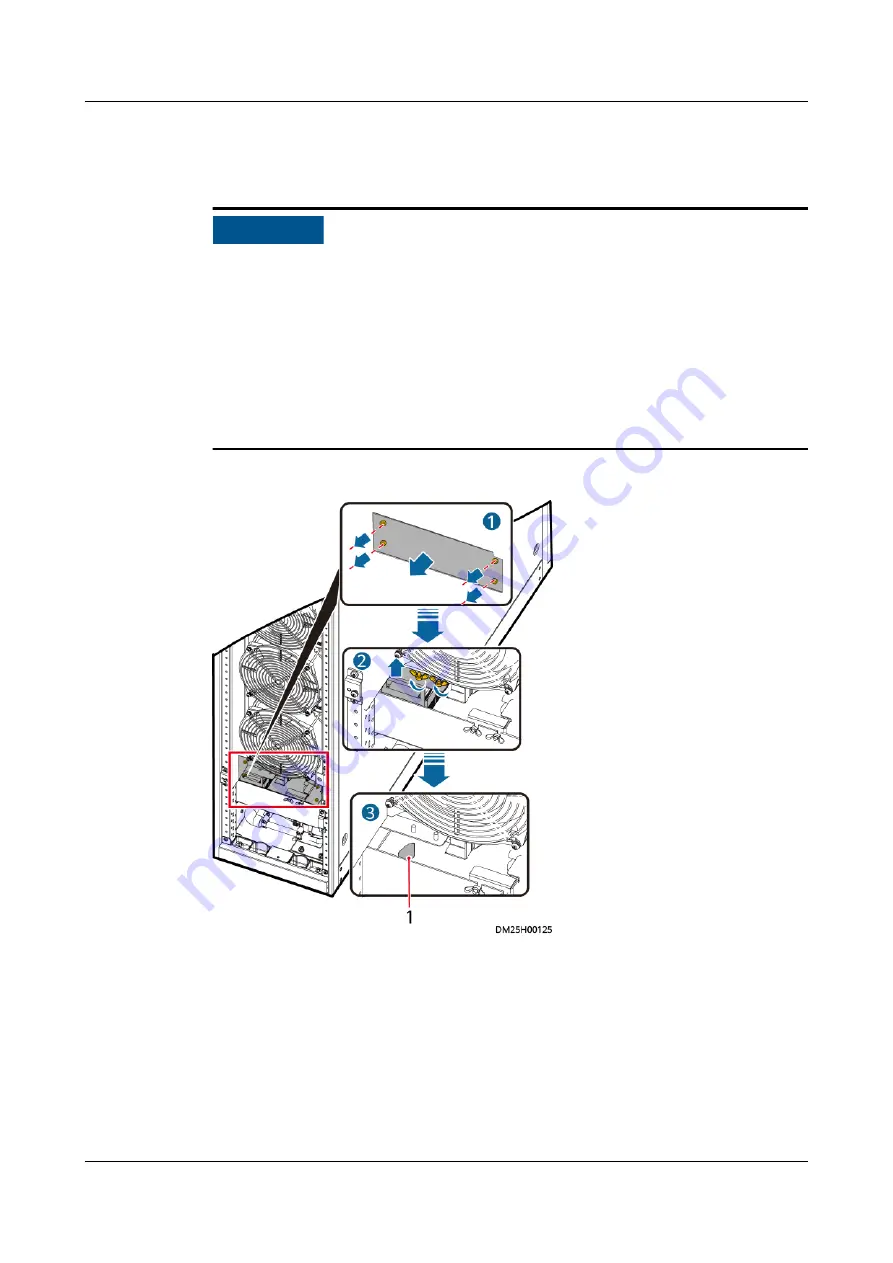
Step 4 Remove the disc nut from the filter, remove the filter.
Step 5 Block the inlet and outlet of the water pump.
NO TICE
● Before removing the water pump, block the water inlet pipe and drainpipe of
the water pump to prevent water overflowing out of the water pan and water
pipe.
● At the front end of the water pump, block the drain outlet (shown in
) of the water pan using a proper object, such as a cloth based on the
actual condition.
● At the rear end of the water pump, bend the white drainpipe (shown in
) and tie it securely using a proper object, such as a cable tie or rope based
on the actual condition.
Figure 4-35 Water pan hole
(1) Water pan hole
FusionDC1000A Prefabricated All-in-One Data
Center
Maintenance Guide (IT Scenario)
4 Parts Replacement
Issue 01 (2021-04-20)
Copyright © Huawei Technologies Co., Ltd.
92