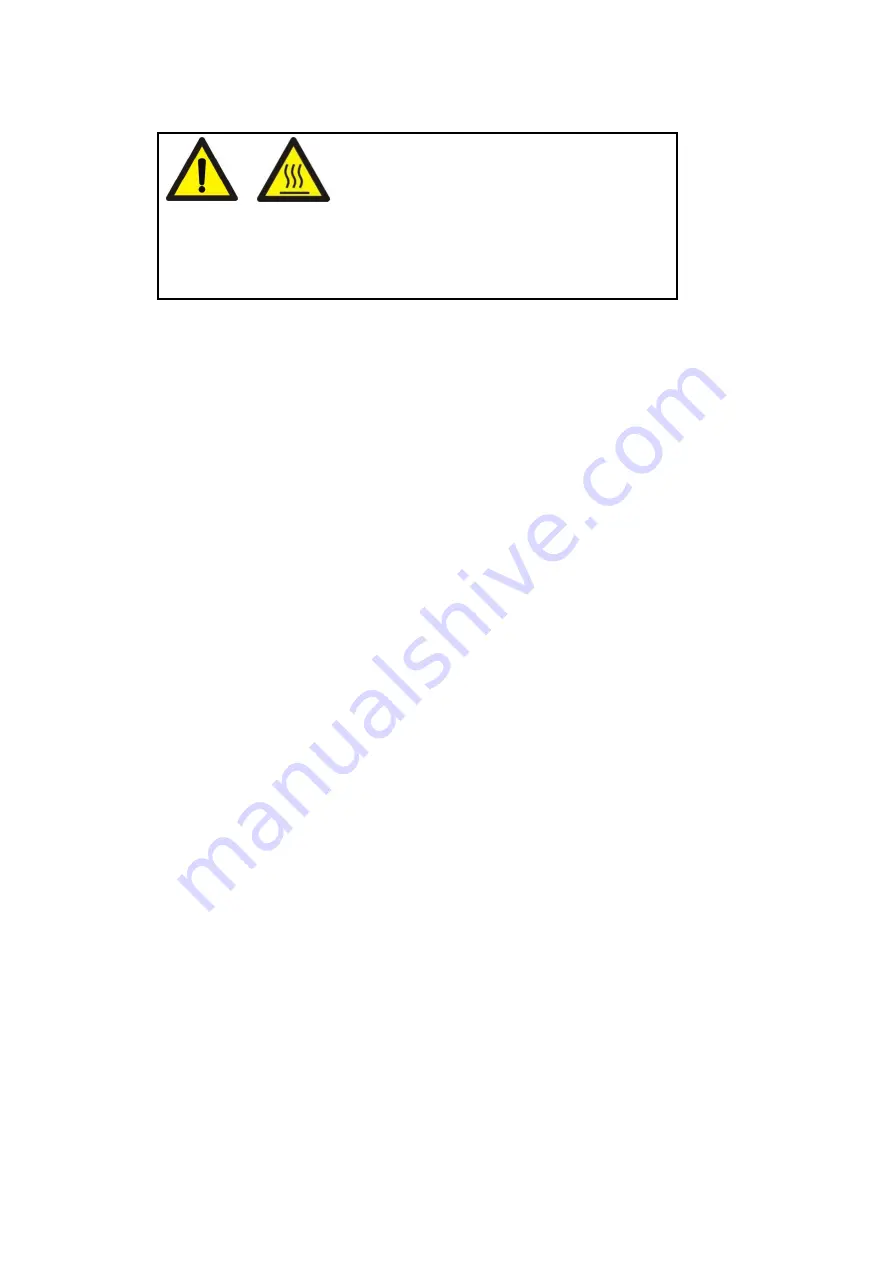
21
5. Replacing Teflon Cloth & Heating Wire
Take care
!
Scald
!
The temperature of heating plate can reach higher than 200
℃
when heating.
Even after cooling, the surface of heating plate is still with high
temperature.
The sealing quality, to some extent, depends on the maintenance of heating plate and silicon
strip.
Regular maintenance
: Use a wet clean cloth to daily clean the heating plate and silicon
strip. Check weekly the heating plate and silicon strip. If the surface of heating plate is not
flat or sealing quality is not good, please replace the heating wire, Teflon cloth and silicon
strip in time.
The average maintenance cycle of the Teflon cloth and the flat heating wire is at least once
every three months. (The prerequisite is the machine is used regularly for packing standard
products with standard vacuum packing material.)
Summary of Contents for HVC-260T/1A
Page 35: ...34 J Electric Circuit Diagram...
Page 36: ...35 K Gas Circuit Diagram...